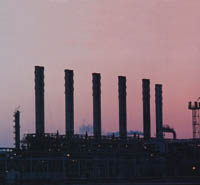
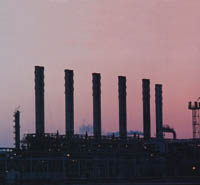
As a leading global producer of ethylene, crude industrial ethanol, ethylene dichloride, styrene, caustic soda and methyl tertiary butyl ether (MTBE), Saudi Petrochemical Company (Sadaf) has played an important part in diversification of Sabic's product portfolio and expansion of output capacities.
A 50-50 joint venture between Sabic and Shell, the complex turns to Shell Global Solutions for expertise on various aspects of plant operations.
For example, Sadaf's MTBE plant was supposed to be operational in January 1997, but production was delayed until June of that year. In the first year of operation, production was only 10 per cent of nameplate capacity.
''The problem with the plant was of a multiple nature,'' said Abdullah Al Rabeeah, general manager, Operations and Maintenance.
It required significant problem solving and well coordinated teamwork in multiple fields of science and technology - i e fluid dynamics, reaction engineering, heat transfer, fluid bed engineering, catalyst chemistry, plant design, plant operations and other fields,'' he explained.
By mid-1998, Sadaf had realised the complexity of the problem and set up a problem solving and project implementation team.
The team included resources from Sadaf's engineering and operations staff. The team obtained some help and support in specialised fields of science, engineering and project execution. The right mix of specialists were involved and were engaged in a teamwork environment.
''Sadaf's MTBE plant uses a fluid bed reactor system. Shell has experience in operating fluid bed reactors, which are known in the Shell world as `crackers'. So we decided to ask Shell for help in this particular area of expertise, and this was provided by Shell Global Solutions.
''Phase One of the plant performance corrective action plan was successfully defined and implemented in a timely fashion. The MTBE unit is now significantly more reliable. The plant has run for more than a year without mechanical damage, it is easier to run and control, the product is always on-spec and all other Phase One expectations have been met,'' said Al Rabeeah.
''We have achieved a highly improved unit performance and improved the technology. Sadaf is pursuing work to further develop the plant's performance in a Phase Two plan, and this is progressing very well.
''For Sadaf, this has been the most significant technology/technical and operating problem we have ever faced in the history of the company,'' he said.
Sadaf's engineering processes have also capitalised on advanced process control technology.
''At Sadaf, we established an initiative to capitalise on the Advanced Process Control (APC) techniques available in the market to improve the reliability and performance of some of our process units,'' said Ali Al Mosalami, Sadaf's Control Systems Manager.
''APC provides real-time manipulations of the process to maintain key process parameters at targets or within constraints. Computer models of the process are used to predict future changes and a software package calculates the manipulations necessary to meet the control objectives,'' he explained.
''We decided to begin with the MTBE plant and have now successfully implemented APC in two of the three units in the MTBE plant.
''We have also started the execution of an APC project in the ethylene plant and the plan is to introduce APC technology into all the other units in the Sadaf petrochemical complex in the future,'' he said.
''We have chosen to use an APC technology package which is being marketed by Shell Global Solutions, and which is a proprietary Shell product,'' said Al Mosalami
''Until recently, this has only been used internally but Shell Global Solutions are now marketing this system to external customers, and are now competing against packages marketed by other vendors.
''What makes the Shell Global Solutions offer so attractive, and one of the main reasons why we chose it for Sadaf, is that Shell Global Solutions offer support and training to their customers, including managers and engineers, who will implement and use the systems.''