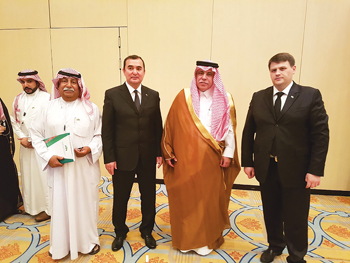
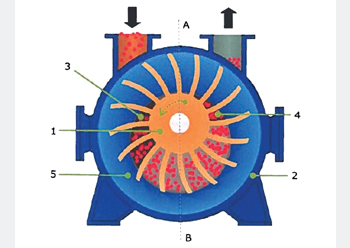
To prevent accidents it is advisable to engage only vacuum trucks with liquid ring pump, like the ones SNSI offers, for pressure discharging hazardous products
Industrial cleaning specialists offering cleaning and maintenance solutions for different industries need to tailor each solution to suit the respective site requirements.
Often these companies are faced with a dual challenge -- keeping the entire plant running at optimal operating conditions while performing cleaning and maintenance and also having to handle the responsibility of raising safety standards to operate in a safe, environmentally sustainable and responsible manner.
Cleaning specialists using technologically advanced mobile vacuum loading equipment to provide routine cleaning services to the downstream oil and gas process industries often require dealing with hazardous and flammable products, says Frank O’ Gara, managing director of Bahrain-based Sarens Nass Smet Industries (SNSI), a leading manufacturer of high performance vacuum loading equipment.
Research and investigations reveal that most accidents at industrial installations/waste treatment plants involving vacuum trucks are caused while loading/discharging hazardous and flammable products. The source of ignition for these accidents are often d heat/sparks from rotary parts of the pumps/compressors used to create negative pressure (vacuum)/positive pressure inside the tanks, he says.
As a precaution against incidents/accidents it is advisable to engage only vacuum trucks with liquid ring pump for vacuum loading/pressure discharging hazardous and flammable products with low flash points. As the name suggests, the liquid ring pump features a liquid ring, explains O‘Gara.
The sketch above shows the operation of a liquid ring vacuum pump. The impeller (1) turns from the centre (eccentrically) in the body/casing (2) and is connected on both sides through intermediate sections with a slight clearance. In one or both intermediate sections, the inlet port (3) and the pressure opening (4) are installed that are, respectively, connected with the inlet and discharge block of the pump.
The pump must be filled with water during use. When the pump starts, the impeller slings the liquid sealant by centrifugal force to the outside walls of the body, forming a ring of liquid (5) at the outside walls of the body that rotates virtually concentrically.
As seen in the sketch air chambers are formed between the hub of the impeller, the impeller blades and the liquid ring that become larger when turning in the direction of the arrow from point ‘A’ to point ‘B’ and become smaller when turning from point ‘B’ to point ‘A’, he continues.
A ‘vacuum’ is created inside the body/casing when the chambers are increased and, therefore, gas is suctioned through the inlet port (3). When the chambers become smaller again due to further turning, the gas is compressed, and it leaves through the pressure opening (4). A continuous supply of liquid is required to supplement the liquid ring as part of the liquid supplied leaves the pump through the pressure openings with the gases while the pump is in operation.
A liquid ring pump is a rotating positive displacement pump. It is typically used as a vacuum pump but can also double up a gas compressor. The function of a liquid ring pump is similar to a rotary vane pump, with the difference being that the vanes are an integral part of the rotor and churn a rotating ring of liquid to form the compression chamber seal. They are an inherently low friction design, with the rotor being the only moving part.
Liquid ring pumps offer distinctive advantages. Liquid (water) that is continuously supplied to the pump ensures that there is no mechanical contact between the moving parts of a liquid ring pump and thus eliminates friction and maintains the relatively low temperature of the whole system. It is vibration free, operates silently, causes least wear and tear, keeping maintenance costs comparatively low and they also have a long service life often more than 10 – 12 years, he adds.