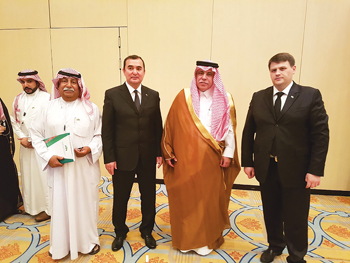
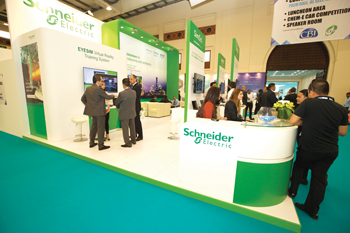
A major US utility company saved $15 million by using PRiSM, while another company saved $500,000, reports ABDULAZIZ MOHAMMED SALAM KHATTAK
Predictive maintenance software by Schneider Electric has helped many major utility companies around the world save millions of dollars by identifying and correcting problems with asset health before costly failures occur.
The global specialist in energy management and automation was at this year’s Middle East Process Engineering Conference and Exhibition (Mepec) held from October 9 to 11 where it showcased a number of its tools for the power, oil and gas, and petrochemical sectors.
Speaking to OGN about its PRiSM software, Martin Turk, director, downstream oil and gas at Schneider, said: 'PRiSM can predict that something bad will happen based on the way the equipment is starting to degrade. But we are not sure when. However, it gives you time to plan for dealing with the problem.'
In addition to alerting to a problem, it can point to the actual portion of the asset from which the problem is arising. So PRiSM tells plant operations and maintenance personnel where to look for the problems, and thus helps in diagnosis and saves plant personnel from spending days or weeks analysing the problem.
Turk said a major US utility company saved $15 million by using PRiSM, while another company saved $500,000 by identifying a compressor problem in one of its gas plants, and another US company saved $7 million
PRiSM was developed by the Instep Software company, which Schneider acquired three years ago and has invested heavily in enhancing its products.
![]() |
Schneider also has the SimSci EYESIM, a 3D tool that uses virtual |
In the region, he said the refining and petrochemical industry was beginning to adopt this predictive approach to maintenance. Major companies like BASF and Aramco are considering the technology, not only for rotating equipment but also for other fixed assets like heat exchangers. In fact, BASF has already adopted the technology and is working with Schneider to deploy it. Saudi Aramco, he said, was piloting the use of predictive analytics software.
But he said adoption by the oil and gas industry will take time. 'Historically, the oil and gas and petrochemical companies are very conservative, so adoption of new technology doesn’t happen quickly. Once they see other industries using this technology and begin to realise the benefits, maybe they would want to look into it. Currently, there is an uptake in the downstream oil and gas industry.'
Turk said the philosophy of preventive maintenance is that the equipment needs to be maintained based on time online. A predictive maintenance philosophy allows plants to wait until an impending problem is identified, giving more time before going for maintenance. So it helps save on maintenance costs.
A study done by the US Department of Energy showed that preventive maintenance can result in 20-30 per cent increase in production, 60 per cent reduction in downtime, in addition to significantly reducing maintenance cost, improving plant reliability, plant uptime, and eliminating catastrophic failures.
Turk said the original application of the predictive maintenance was in the airline industry, where sensing of jet turbine performance was done. The power industry was then the first to adopt the technology after the airline industry, because it of the many pieces of rotating equipment in plants.
Taking it a step further, Schneider is currently working on forecasting when a failure will actually happen.
Another offering from Schneider is Spiral Suite, a unified supply chain management tool for feedstock selection, refinery and petrochemical plant planning and scheduling, and distribution management. It’s basically an enterprise supply chain knowledge management tool across the whole supply chain said Turk.
'Spiral is becoming very much accepted and adopted by the industry. We are doing a lot of projects replacing some competitive systems.'
Traditionally, he said, planning, scheduling and distribution management systems were all standalone applications, which required time and effort to interface or integrate. But Spiral is a unified system.
'So you build one model. And when you want to do planning, you turn off the tankage and just do a 30-day planning for the next month. Or you might turn on the tankage, inventory management, receipts and shipments and do the scheduling using the same model.'He said Spiral is flowsheet based, and is very easy to learn and use.
A major European oil and gas company has adopted the Spiral suite and has expanded the user base from a small number of highly trained uses of supply chain systems to thousands of people in a wide variety of disciplines such as crude and product trading, process engineering and marketing
Turk said some of the really exciting stuff is around enterprise asset performance management.
'Going from what are called traditional monitoring of equipment health through DCS displays and database analysis, we are putting in place automated systems to improve asset health and performance, and to track asset health degradation over time.'
He mentioned a study done by ARC a couple of years ago which showed that only 18 per cent of asset failures come from known causes; 82 per cent are random failures.
'Predictive analytics is designed to capture and identify that 82 per cent of the potential failures modes, and determine very subtle changes in asset behaviour and alert the operators and maintenance personnel that there is abnormal behaviour and if that continues, there is a good chance it might cause the equipment to fail.'
He said the application had brought huge benefit to users. 'This year, one of our customers – a power utility company – had a ‘catch of the year’, which allowed them to prevent a failure and correct it. This saved them money to the tune of $10-20 million, from just one catch.'
Turk said the software uses historical data and builds a model of expected performance using complex sophisticated mathematical data analysis techniques that runs the data against different scenarios to validate that the model is accurate. And then it’s fed with data in real time. So when an expected behaviour deviates from actual behaviour continuously, that gives an alert that something abnormal going on.
Schneider also has the SimSci EYESIM, a 3D tool that uses virtual reality (VR) and/or augmented reality (AR) to connect control room operators, maintenance, and field personnel in a single realistic learning environment.
The VR shows models in an actual 3D representation of the plant. This helps in training maintenance personnel. The AR, meanwhile, is a tablet based system that maintenance personnel can use in the field. By pointing at an asset, they can acquire the configuration of the asset, last maintenance, historical data, etc, right on their tablet. This helps in quickly and correctly fixing problems with the asset.