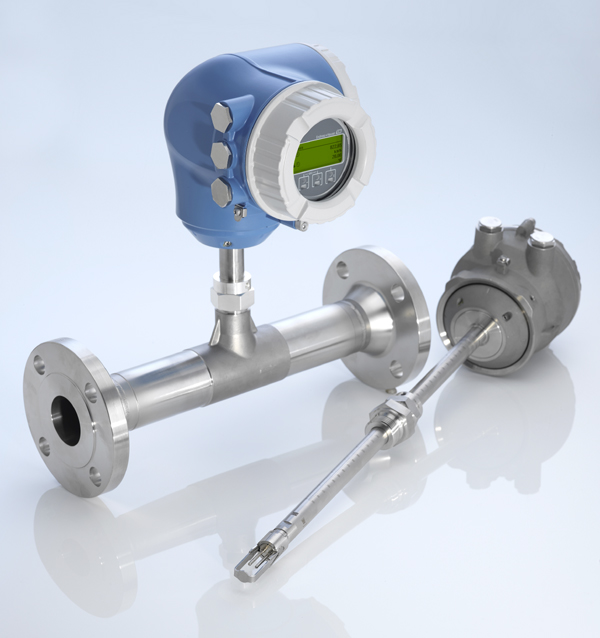
Endress+Hauser has successfully installed over 100,000 t-mass flowmeters worldwide. The proven and robust state-of-the-art measuring technology allows customers to record all kinds of gas flows, whether compressed air, natural gas, protective gas or oxygen.
The t-mass F/I 300/500’s ingenious sensor design and one-of-a-kind monitoring functions leave nothing to be desired in terms of optimum process control. Even when process conditions fluctuate significantly, gas flows can be measured in all industries with unmatched accuracy.
In numerous industries, thermal flow measuring technology has long been used for measuring pure gases and gas mixtures, such as in research and development laboratories, in HVAC (heating, ventilation, air conditioning), for measuring flare stack and flue gases, in utilities with compressed air, oxygen, nitrogen or argon, for monitoring consumption of natural gas in gas-fired boilers or for monitoring carbon dioxide in the food and beverage industry.
As a result, when combined with the comprehensive functionality of the Proline 300/500 transmitters, this opens up new possibilities for process control, quantity measurement, leak detection, cost allocation and energy management.
Even when process and ambient conditions are fluctuating significantly, t-mass ensures high measuring accuracy (±1.0 per cent) with excellent repeatability (±0.25 per cent). Gas flows with low pressure and a low flow velocity can also be measured without any problems thanks to the high turndown (1000:1).
The robust industrial design of t-mass makes it possible to operate the device over the long term without any maintenance, thus saving time and money for the user. t-mass F and I are used at process temperatures up to 180 deg C (356 deg F) and pressures up to 40 bar (580 psi).
For highest flexibility
The t-mass 300/500 measuring system is equipped as standard with a ‘gas engine’. This software model enables, among other things, calculating the mass flow of a gas under the current process conditions.
In addition, the gas engine offers users unbeatable advantages in operation:
• Exact measurement of pure gases and gas mixtures by selecting from up to 22 standard gases as well as creating gas mixtures by combining up to 8 of these gases (special gases on request).
• Calculating flow velocity, reference density, corrected volume and energy flow for current operating conditions.
• Dynamic correction for changes in pressure, temperature and gas composition.
• Changing programmed gases without recalibration.
• Switching function for two predefined gas groups via the status input, for example, for flushing processes with an additional gas.
Industry-optimised
The t-mass F and t-mass I sensors feature maximum robustness, enabling them to withstand such factors as pipe vibrations, solid particles in the gas and process fluctuations (temperature shocks).
Thanks to its patented innovative sensor design, t-mass is suitable for low-maintenance, long-term operation with high accuracy. All wetted parts are made of corrosion-resistant steel and comply with the stringent requirements of NACE MR0175/MR0103. For gases that form unwanted coating in the pipe, the sensor can be removed for cleaning work and reinstalled quickly and easily – without impairing the measuring performance.
Greater process reliability
Because the t-mass 300/500 measuring system has been developed in accordance with IEC 61508 (SIL 2), it can also serve as the preferred system in safety applications. Any device or process errors that may occur are clearly categorised in accordance with NAMUR NE107 and immediately indicated. This makes it possible to take fast and targeted countermeasures.
In addition, t-mass 300/500 is equipped with one-of-a-kind alarm functions that are used for immediately detecting unwanted condensate drops on the sensor or pulsating flow.
In the case of condensate, this can prevent the emergence of long-term corrosion damage in piping systems. Another one-of-a-kind feature is the ability to measure and account for gas flows in both flow directions (bidirectional) and to generate an alarm message for reverse gas flows.
Heartbeat Technology
Heartbeat Technology is another highlight. This testing function is integrated into all Proline measuring devices and enables permanent self-diagnostics with the highest diagnostic coverage (over 95 per cent) as well as a metrologically traceable device verification without process interruption.
For safety reasons, Heartbeat Technology also has a ‘Heartbeat Sensor Integrity’ test function for detecting changes to the measuring electronics and/or sensor as a result of extreme environmental and process conditions. Heartbeat Technology reduces complexity and risks in a system and thus increases its reliability and availability.
Direct data access
Proline 300/500 transmitters include a web server as standard. Using a standard Ethernet cable and a laptop – or wireless via WLAN –, users have direct access to all diagnostic, configuration and device data without additional software or hardware. This enables targeted and time-saving maintenance and service.
HistoROM
The data storage concept (HistoROM) ensures maximum data security before, during and after service. All calibration data and device parameters are stored securely on the HistoROM data storage module and are automatically reloaded after maintenance work. Therefore, installing spare parts is easy, saves time and thus reduces unnecessary downtimes.
Seamless system integration
The t-mass F/I sensors can be combined with two different transmitters: as a compact version (Proline 300) or as remote version (Proline 500) with up to four inputs and outputs.
The digital signal processing begins in the intelligent sensor and is the basis for real multivariable measurement. This means that t-mass can simultaneously record multiple measured values such as mass flow, flow velocity or gas temperature for process control, and forward them to a process control system.
Complete access to all measurement data, including diagnostic data acquired by Heartbeat Technology, is possible at any time – thanks to digital data transmission via HART or Modbus RS485 as well as via WLAN or via the freely combinable inputs and outputs.—Tradearabia News Service