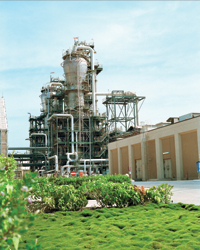
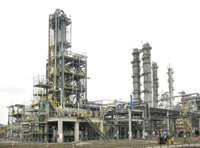
Sabic's Innovative Plastics business has been recognised by the American Chemistry Council (ACC) for its extensive world-class programs designed to improve energy efficiency, taking seven Responsible Care[R] Energy Efficiency Awards, including three for its Mt Vernon, Indiana, manufacturing facility.
This accomplishment marks the second consecutive year in which Sabic’s sustainability initiatives have been honored by the ACC. These multiple awards for a diverse range of projects demonstrate Sabic’s strong leadership, world-class technology and culture of innovation that enables the company to minimise environmental impact while strengthening operational excellence, all of which significantly benefit its customers worldwide.
'We are honoured to receive the ACC Responsible Care Energy Efficiency Awards as we continue to build our sustainability programmes with strong and steadily increasing focus, resources and commitment,' says Mike Walsh, general manager, resins operations, Innovative Plastics, Sabic.
'Sabic works continuously to minimise its operational footprint by reducing carbon intensity, improving energy and water use and increasing material efficiency. This effort complements our drive to meet our customers’ toughest environmental challenges as well as their needs for superior-quality, high-performance sustainable materials.'
The ACC Responsible Care Awards are presented annually to honour companies with energy efficiency improvement projects, including the creation of energy teams, communications, goal setting, recognition and management support. Individual ACC member companies nominate specific projects for recognition; winners are selected by the judging committee. ACC presented 73 awards to 19 member companies.
The seven Responsible Care Awards presented to Sabic recognise a variety of innovative projects to reduce energy usage and greenhouse gas emissions, and reduce waste disposal.
• Sabic’s Bay St Louis, Mississippi, facility, won for a focus on electrical efficiency in three areas: plant lighting, solar, and replacement of a chiller with a centrifugal compressor.
• Sabic replaced a 20-year-old process chiller at its Burkville, Alabama, resin manufacturing plant with a more efficient and environmentally responsible chiller. The old equipment used a refrigerant with high ozone-depleting and high global warming potential. The replacement uses new technology and refrigerants to cut energy usage equivalent to a reduction in greenhouse gas emissions of 432 tonnes per year.
• At Sabic’s headquarters in Pittsfield, Massachusets, the company undertook a multi-year site improvement that featured energy-efficient heating ventilation and air conditioning (HVAC) retrofits. The project led to energy savings and a reduction of 7,000 tonnes of carbon dioxide (CO2) emissions per year.
• Sabic’s Washington site undertook a project to simplify plant and instrument air systems. The redesign reduced total electrical usage by an estimated 2.24 MMkW hours per year and elimination of 2,930,000 lbs/year of CO2 emissions.
• At the Sabic Mt Vernon facility, a process was successfully developed to recover and purify the sodium nitrite from a wastewater stream, and then sell it commercially. Eliminating disposal of the material resulted in reduction in total combined energy intensity for the Mt Vernon production facility and the offsite disposal facility. This project was awarded 'Exceptional Merit' by ACC.
• Also at Mt Vernon, a specialised chemical unit was upgraded to reduce steam usage and operating costs. The reduction in steam demand resulted in a reduction of 4,198 tonnes of CO2 per year and 50,156 mmBtu/year of energy.
• The final award honoured yet another project at the Mt Vernon facility. This project was an upgrade to a Lexan resin unit to recover energy, cut operating costs and reduce greenhouse gases. By reducing the steam demand of the boiler unit, the plant achieved a reduction of 2,006 tonnes of CO2 per year and 24,000 mmBtu of energy per year.