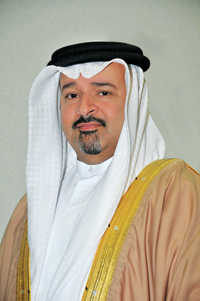
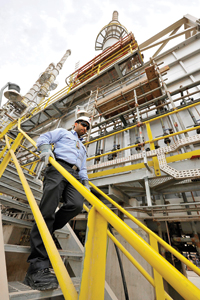
BAPCO continued with its long term strategy plan that was developed in detail during the last quarter of 2010. The company’s strategic plan outlines a strategy for growth in four key areas, refining, marketing, human resources and oil and gas development and supply.
Bapco’s corporate priorities have been re-focused and consolidated into three priorities as follows:
• Future Bapco: Increased shareholder value through the Bapco modernisation programme (BMP) and supporting initiatives that are critical to the enablement of BMP;
• Increased Competitiveness: Operational excellence by improving systems, processes, policies, work flows, standards and procedures, gap assessments and gap closures, increased productivity eg smarter way of working and/or innovative technology to reduce fixed and variable costs and increased shareholder value through revenue growth eg capex projects with payback by 2017, new markets, products, customers, increased revenue from existing customers; and
• Government / Noga projects: Provide technical and business expertise to carry out projects on behalf of Bapco shareholders.
Under these three strategic priorities, 23 corporate initiatives were developed for implementation in the years 2013 – 2018.
During 2012, departments /divisions developed additional 58 initiatives to maximise the overall performance of the business portfolio.
The project management office (PMO) responsible of overseeing the implementation progress of all the initiatives became fully functional. The PMO laid the foundation to ensure delivery of the prepared strategies.
BAPCO MODERNISATION
The world continues to demand better quality products. The GCC announced a required shift in the near future, for the local markets, to a higher quality gasoline. Bapco produces large volumes of high sulphur fuel oil and very low quality gasoline. The world will demand very low sulphur fuel oil and gasoline specifications. Bapco needs to address these two main products in order to stay competitive and enhance its strategic position.
Bapco conducted several studies in 2011 as part of the refinery master plan project. The studies completed in 2011 are due diligence study, financing options study and decision risk analysis study.
Bapco’s board of directors met in November 2011 and decided to move ahead with the Bapco modernisation programme known then as the refinery master plan project.
The board approved the new refinery configuration which will increase the capacity to 450,000 barrels per day (bpd) from the current 265,000 bpd. The project also involved several upgrading units which will convert black oil products to more valuable white products like diesel. Also, Bapco’s energy efficiency will increase drastically. Overall, Bapco will become one of the most competitive and sophisticated refineries.
Following from the board of directors approval, the strategy and business development division engaged Chevron Lummus Global (CLG) to start a “unit definition study” to better define the envelop around the new refinery and commence preliminary engineering work on the selected configuration.
![]() |
Bapco currently has two liquid LPG treating |
The project was subject to a major review towards the end of the unit definition study stage. Bapco executives decided to rename the project, “Bapco Modernisation Programme (BMP)” and to enlarge the envelope to include all the other projects related to future Bapco.
BUSINESS DEVELOPMENT
The major objectives of the business development department are to diversify Bapco’s interests into downstream hydrocarbon and chemical related businesses, increase the company’s exposure with international companies and increase career opportunities for Bahrainis in both local and international markets.
In 2012, the Bapco board of directors approved a five-stage business evaluation procedure which was developed by the business development department to identify good joint venture or acquisition opportunities for Bapco.
A total of 25 target companies were identified and studied in 2012 which are now at different stages in the evaluation process. Three target companies have been approved by the board of directors for further study by a consultant, who will be appointed before the end of the year, to produce an independent report on each opportunity. These reports will assist the board of directors to decide if approval should be given to proceed to the final ‘Confirmation and Closure’ stage which will lead to Bapco making a formal proposal to form a joint venture with, or take a share in, the target company.
Detailed discussions have commenced with two of the target companies and good progress has been made. The third target company continues to express interest but no detailed discussions have commenced to date due to their remote location.
The business development department anticipates that at least one business opportunity could be realised in 2013.
While 2012 was dominated by a slowdown in global economic growth, the key benchmark crude prices remained high predominantly above $100 per barrel during the year mainly supported by the concerns over supply disruptions due to geopolitical tensions in the Mena region.
Abu Safah crude exports totalled 48.2 million barrels in 2012 compared to 54.7 million barrels in 2011. This lower export during the year was due to the drop in production from Abu Sa’afah field due to the unexpected technical problems in the submersible pumps starting from first quarter 2012.
The average price realised for Abu Safah crude was $110.1 per barrel compared to $106 per barrel in 2011. With the continued strong demand on medium and heavier grade crudes throughout the year; the marketing team managed to achieve higher premiums for the contractual volumes of Abu Sa’afah crude and which directionally contributed positively to the kingdom’s national budget/wealth.
Bahrain holds an equity share of 150,000 barrels per day (bpd) in output from the joint Saudi Arabia – Bahrain Abu Safah offshore field. All our crude exports were destined to East of Suez markets; Far East 70 per cent, South East Asia 16 per cent, Indian Subcontinent 9 per cent and Australia 5 per cent.
Along with Bapco’s yearly planned maintenance schedule, the petroleum products exports during 2012 totalled 83.6 million barrels compared to 82.7 million barrels in 2011. Middle distillates accounted for 56 per cent, followed by fuel oil 21 per cent sold primarily to the Middle East bunker market and naphtha 19 per cent sold mostly to Asian petrochemical manufacturers.
Like the previous years, Middle East (mainly GCC Countries) accounted for the highest share of total sales (at 49 per cent), followed by Far East (mainly Japan) and South East Asia (at 20 per cent), Africa (at 16 per cent), Europe (at 12 per cent) and Indian Subcontinent (at 3 per cent).
All of Bapco’s sulphur, approximately 421,000 barrels-equivalent, was exported to Asia, with the Indian Subcontinent being the main/key consumer (92 per cent) followed by South East Asia (8 per cent).
To meet the company’s objectives to maximise its profitability, Bapco continued to capture market opportunities throughout the year and imported a mix of feedstock and blending stocks which contributed to total benefits of about $6 million.
A total of 12,127 barrels per day (bpd) of Jet A-I fuel was supplied to Bahrain Aviation Fuelling Company (Bafco) at Bahrain International Airport, of which Bapco’s share amounted to approximately 7,300 bpd.
The overall refinery margins remained close to the 2011 level, an average of $7.1 per barrel.
The total volume of local refined product sales amounted to 9.7 million barrels (a y-o-y increase of 10 per cent), led by high octane (Mumtaz) gasoline (37 per cent of sales), diesel (27 per cent), low octane (Jayyid) gasoline (22 per cent), LPG (6 per cent), Kero/Jet (4 per cent) and Asphalt (4 per cent).
The Bapco bulk diesel station has been commissioned in August 2012 at a cost of $30 million. This is the latest state of art facility that has been designed and built to the safest international standards of handing petroleum products and to serve the local market requirement of diesel. This top loading facility has the capacity to handle 40,000 bpd, with its four bays that can handle four tankers simultaneously.
PLANT ENGINEERING DEPARTMENT
Bapco’s plant engineering department (PED) handled in year 2012 various investment projects from inception to completion. Chevron’s Project Development and Execution Process (CPDEP) was adopted in the development and execution of all the engineering projects. This is a process that improves decision making and execution by fostering better planning, collaboration and communication.
PED also provided engineering support to all company operating areas including TandI’s and non-operating areas. Below are highlights of some of the key projects handled in year 2012.
REFINERY ENGINEERING SECTION
Upgrade and Refurbish Platformer GT3650: Installed cost of project: $5.5 million, Project status: Completed during April 2012.
The platformer gas turbine was installed and commissioned in May 1982. Since commissioning, the original gas turbine had run over 15,0000 plus hours with 483 fired starts. The gas turbine GT3650 is the driver for the operationally critical hydrogen recycle gas compressor (K3650). A thorough inspection carried out on the turbine in September 2009 resulted in recommendation to replace the hot gas path components including the rotor and stator blades of the turbine. This had been recommended based on the damage reported to components due to corrosion, erosion and some foreign objects. In addition, all of the hot gas path components had exceeded the estimated running life.
During April 2012 Platformer/Unifiner TandI, a major overhaul and upgrade was completed for GT3650 recycle compressor gas turbine. Both the HP and LP rotors of GT3650 were renewed along with upgrade of the hot gas path components.
This is one the first major project in PED that has been completed using the methodology of CPDEP process that helped really well in shaping-up the project.
3SRU Modification Project: Installed cost of project: $25 million, Project status: CPDEP Phase 3, ETC: Q2 2014
The purpose of the sulphur recovery plant is to process amine acid gas and sour water stripper off-gas that is generated in the refinery.
Presently 3 SRU processes only amine acid gas and does not have the capability to process SWS off-gas, whereas 4 SRU has the facility to process both amine acid gas and SWS off-gas. Therefore, with the current configuration, SWS off-gas will have to be flared when 4SRU is out of service.
The project objective for 3SRU revamp is that it can process SWS off-gas and can act as a true spare for 4SRU and ensure that Bapco complies with the government environmental regulations on air emissions
The following are the key components of the new facilities required for 3SRU revamp:
• Replacement of existing reaction furnace (F6611), thermal reactor (C6611) and waste heat boiler (E6611) for processing SWS off gas with new foundations;
• Installation of new SWS gas KOD (C6612), associated piping and SWS gas KOD pumps (P6611A/B) with a common spare;
• Replacement of existing Auxiliary burners with steam re-heaters ( E6612/E6613); and
• Installation of all necessary instruments and control system associated with new and modified equipment.
The Feed for the project has been completed. The bids from four EPC contractors have been obtained that are being presently reviewed. This is one of the first beta projects on which the CPDEP process has been utilised with good results. In addition, this is the first engineering project for which a formal review by industry-leader, IPA-Netherlands, has been carried out for evaluation of Front End Loading (FEL) and Cost Index.
LPG Treating Unit: Installed cost of project: $6 million, Project Status: CPDEP Phase 3, ETC: Q1 2014.
Bapco currently has two liquid LPG treating facilities. No2 polymerisation plant (2Poly) treats olefin LPG from the gas concentration unit (GCU). No1 lpg treating unit (1LPG) treats LPG from the naphtha rerun complex (NRC). Both 2Poly and 1LPG are in the fluid catalytic cracking unit (FCCU) area. Existing LPG treating facilities are in service for over 60 years. H2S in sour feed LPG is removed using caustic and the spent caustic is discharged into the sea via sea water return channel having an environmental impact. Limitations encountered in 2Poly treating facility during the FCCU low throughput trial which will be the post-LBOP operation. Treating capacity is limited during FCCU HVGO and LBOP operating modes meaning loss of LPG.
The objective of the project is to address EHS issues related to caustic handling/disposal and ensure enhanced LPG recovery during HVGO and LBO mode of operation.
Engineering design package (EDP) work completed by JGC for the low cost option by reusing redundant column 8V402 and adding cooler/booster pump on amine circuit. Feed by JGC is complete.
Upgrade 1VBU Heaters Transfer Line Metallurgy: Installed cost of project: $1.6 million, Project status: Completed during March 2012 TandI of 1 VBU and KRU.
Upgrade of the metallurgy of transfer line to stainless steel type-347 has been competed during March 2012 TandI of 1VBU. The transfer line was original 1936 installation, constructed from 5 per cent Cr steel material. It had been recommended to replace it with stainless steel type-347 material due to higher corrosion/erosion rates encountered since the increase in the unit feed rate to 24 mbpd from 22 mbpd in March 2006. Feed increase decision was based on the financial benefit of about $2 million per year by additional processing. The project has been completed as planned in TandI considering SS-347 material long lead item and critical stress analysis with major change in the line routing by incorporation of expansion loops and new hangers.
Replace Kerosene Pumps and HSR Pumps of 1/2CDU: Installed cost of project: $800,000. Project status: Completed during March 2012 and October 2012.
Replacement of two kerosene pumps (P2119 and P2204) for 1and 2 CDU was competed early last year. HSR pumps (P2110 and P2111) were replaced during recently completed in October TandI of 1/2 CDU. The existing pumps had long been identified as bad actors due to high failure frequency and routine maintenance requirement contributing significantly to maintenance cost. Pumps casings were constructed from cast iron which is unsafe for use in hydrocarbon service and not complying with the existing API 610 standard for pumps. Installation of new pumps as per latest API-610 will significantly reduce the failure rate and maintenance cost and will improve the overall reliability of the unit.
O S&E ENGINEERING SECTION
Bulk diesel top loading facility at Sitra marketing terminal: A considerable quantity of diesel was dispensed in bulk through various service stations on the island. This practice was unsafe and encouraged misuse of product. It was believed that significant quantities of diesel were smuggled outside the country due to the high differential between the Local and International prices. The bulk diesel top loading project was developed to eliminate the unsafe bulk diesel loading in these outlets and to meet needs for bulk diesel of local customers while stopping unauthorised export of diesel.
The facilities included buildings for operators work station, schedulers office, security office and operators cabin, access roads, traffic junction at Um Saad Avenue, diesel supply pumps, floating suctions for tanks, loading systems, compressed air system, firefighting system, piping, perimeter fencing, landscaping, LV and HV substations, instrumentation and integration with Terminal Automation system. All major equipment, contracts for piping, buildings and access roads were finalised after obtaining approval from Tender Board. As part of this project we installed the biggest floating suction (18 inch size) in Bapco in tank 966.
The project was commissioned on July 18, 2012. Currently all the genuine customers are being identified and our customers are satisfied with queuing time, reduced filling time, safety and faster turnaround time for filling of truck.
Enhance import of butane from Banagas to refinery: Bapco produces refinery off-gas (ROG) in unifiner, platformer, 2HDU and LSDP which is rich in butane, propane and naphtha. The excess ROGwas supplied to Banagas since 2005 for extraction of butane, propane and naphtha. Naphtha extracted from ROGwas imported by Bapco and the extracted butane and propane were exported by Banagas for Bapco.
LPG production in the refinery had been reduced due to less feed stock available for FCCU post commissioning of LSDP in 2007 and had further reduced with commissioning of LBOP in 2011. However the demand for LPG for domestic purpose in Bahrain is growing at an annual rate of 4 to 5 per cent and the increased demand cannot be met by refinery LPG production. To satisfy the growing demand of LPG, Bapco had decided to import from Banagas the entire quantity of butane (approximately 3,000 BPD) extracted from ROG to blend with LPG.
The project was to install a new 2 km long 4 inch NB pipeline from the Banagas butane shipping line to Horton spheres, install mass flow meters, de-aerators, ESD valves etc. The project was commissioned on July 5, 2012.
Partial replacement of No 5 sealine: This project is for replacement of 12 inch-No 5 sea line from Sitra Tanks Fire Pumps House in the south flume to the Wharf T-Head. The new No 5 sea line has been resized to 14 inch due to operational requirements. 95 per cent of the project is completed and is expected to be commissioned in 2013.
Enhance fire fighting facilities in refinery and Sitra: In December, 2010, a team from Chevron had conducted a field survey to check the adequacy and effectiveness of existing fire protection system at Bapco. Post survey, a presentation was made by Chevron team to Bapco management on their findings and recommendations. Based on the recommendations and as a continual improvement in safety, Bapco has initiated the project “Enhancement of existing fire protection system”, for the refinery and Sitra tank-farm including Sitra marketing terminal. This will achieve optimum level of safety in accordance with internationally accepted latest fire protection standards of NFPA, API and Chevron.
The firewater pumping capacity currently available in the Refinery is 9,000 usgpmand in Sitra Tanks is 6,000 usgpm. Preliminary studies conducted based on latest Chevron/NFPA standards recommends to enhance existing fire water pumping capacity to ~12,000 usgpm in the Refinery and Sitra Tank-farm.
This project will ensure the required flow to fight the worst case fire and minimum residual pressure of 125 psig at the hydrant outlet farthest from the main fire water pumps. As part of project it is envisaged that new pumps and piping network are to be provided by ascertaining the total fire water quantity based on fire protection analysis and sweet water will be used as pressurising medium for fire water network.
Currently the project is in CPDEP phase –II. Also a Project Development Authorisation (PDA) fund has been approved to utilise the services of a reputed Engineering Consultancy firm having substantial experience in fire protection analysis and design of fire water system, for developing Feed of the project and it is in tender stage.
Gas distribution network: Natural gas from Bahrain Fields is transported via transmission lines to the three main distribution points, namely Alba distribution point (ADP), Riffa distribution point (RDP) and Dur distribution point (DDP). From these distribution points the gas is supplied through a network of pipelines, local distribution points and metering stations to various customers across Bahrain. The gas distribution network (GDN) supplies about 1,300 mmscfd (million standard cubic feet per day) of gas to various customers. Plant engineering OS&E section has been responsible for carrying out new projects related to GDN and for providing engineering support to gas distribution – gas planning and sales section since March 2010.
New gas distribution station at Hidd industrial area: The project scope included building a new Hidd industrial area distribution point (HIADP) and a 4.5 km long 10 inch diameter underground gas ring main at Hidd industrial area. The new facility has a design capacity to supply 118 mmscfd gas to various customers in Bahrain International Investment Park (BIIP), Bahrain Investment Wharf (BIW) and the Hidd industrial area.
Construction of the project was completed in June 2012 and the facility was commissioned in July 2012. Currently all customers in Hidd industrial area and BIIP are being supplied gas from the gas ring main. SULB (United Steel Company), a newly established steel company in South Hidd industrial area, is also being temporarily supplied gas from HIADP.