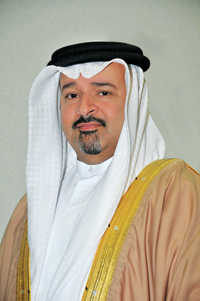
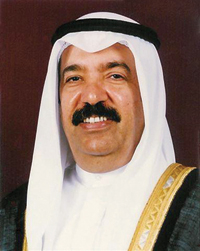
BAHRAIN-BASED the Gulf Petrochemical Industries Company (GPIC) had achieved outstanding success in 2012 producing approximately 1.5 million tonnes of ammonia, methanol and urea at a rate about 0.3 per cent higher than planned for the year.
Moreover, continuing on that success, GPIC has recorded its highest-ever monthly production in January 2013.
Company president Abdulrahman Jawahery says the total 140,258 metric tonnes (mt) production in January included 61,549 mt of granular urea, 39,995 mt of ammonia and 38,714 mt of methanol.
“This record follows the company completing its biggest-ever periodic maintenance of its plants and facilities in November,” Jawahery says.
“We spent a significant amount on capital expenditure projects to carry out continuous improvements which helps the company maintain the plants at an optimum efficiency,” he says.
The company’s products being of high quality, it was able to export everything produced, exceeding by 1.1 million tonnes the quantity planned for export to various global markets, says Jawahery.
He explains that this was nearly 1 per cent higher than planned. The company liquidated all inventory of products and marked the closure of the financial year with a low rate of inventory for export, which had positive impact on the results for last financial year.
During 2012, the company was able to fully achieve its marketing objectives by successfully meeting customer expectations especially with regards to the quality and timely delivery of its products. Although 2012 marked the biggest plant turnaround year in the history of GPIC, it still managed to export a total of 1,105,093 tonnes of ammonia, urea and methanol to the world markets, which included 62,566 tonnes of ammonia, 630,602 tonnes of urea and 412,925 tonnes of methanol, Jawahery tells OGN in an exclusive interview.
GPIC also carried out $41.711 million worth of capex projects in 2012. The main project undertaken was the turnaround, he says.
The US took the highest share of exports, about 40 per cent of the total exports of the company for the period in question. The US market imported nearly 445,000 tonnes of methanol and urea, including 380,000 tonnes of urea, this figure accounting for 60 per cent of the company’s total urea exports. The People’s Republic of China is the largest importer of methanol with a share of about 62 per cent or approximately 258,000 tonnes of the company’s total exports.
![]() |
Jawahery ... maintaining the highest levels |
With regard to financial targets, Jawahery says that the company achieved high returns on sales of ammonia, methanol and urea, which increased returns by 20 per cent over the planned budget.
The company also provided the local Bahraini market with 1,285 tonnes of urea fertiliser in response to farmers’ needs.
He stresses that all these achievements were the result of joint efforts and continuous cooperation between the relevant departments of the company itself and its marketers, Saudi Basic Industries Corporation (Sabic) and Petrochemical Industries Company (PIC) of Kuwait.
The GPIC president expresses his great pleasure at the company’s distinguished achievements during 2012 including record numbers in terms of production, export, maintenance and safety, “all of which make the company a good example of fruitful cooperation and a shining model of excellence”.
Jawahery identifies the emphasis on safety as one of the key elements of success and describes this aspect as the backbone of the remarkable continuity witnessed by the company’s operations. In a unique achievement, the company clocked more than 3,900 working days without a lost time incident, boosting levels of productivity.
He adds that credit goes also to the durability of precautionary safety measures adopted by the company and the ongoing evaluation of these procedures whenever the need arises, according to the best global standards approved.
Jawahery stresses that comprehensive maintenance performed on a regular basis had contributed to ensuring the continuity of plant operations for more than 30 months, indicating that the ammonia and methanol plants have been able to maintain continuity of work since September 2010, more than 900 days without stop and the urea plant more than 600 days, which confirms the effectiveness of the safety procedures and maintenance plans pursued by the company. All these allowed the company to fulfil its contractual obligations with customers and to obtain high prices for its products on the world market, he says.
Excerpts from the interview:
What was GPIC’s total production target for 2012? How much of it was achieved? Could you give us a split up of how many tonnes of ammonia, urea and methanol did GPIC produce?
GPIC’s total production target for 2012 was 1,449,235 tonnes.
Actual production: 1,454,298 tonnes (0.35 per cent higher than budget).
Breakdown:
• Ammonia – 411,260 tonnes
• Urea – 626,985 tonnes
• Methanol – 416,053 tonnes
Is the total production target for 2013 higher than that of 2012? If so how did the company beat the general slump that has affected the petrochemical sector adversely? What was its winning market strategy?
Yes, the total production target for 2013 is higher than that of 2012 (see table 1).
GPIC carries out rigorous corrective and preventive maintenance work to keep the plants at optimum efficiency and reliability. The company spends a significant amount on capital expenditure projects to carry out continuous improvements in the plants. The philosophy of continual improvement helps the company in keeping the plants running at optimum level and has a cutting edge.
Safe and reliable operation is directly transferred into profitability at the end of the day. Yes, the market has an effect on profitability of all companies such as ours, however having 100 per cent reliability producing 365 days a year at over 100 per cent capacity in a safe and efficient manner is what makes us successful. GPIC, over the years has demonstrated its excellence in this area. We have had 100 per cent on stream factor at 100 per cent capacity and for the past 10 years, which is a world record.
GPIC’s long term organisational culture and ‘One Team Spirit’, has created a professional work culture and atmosphere for all to work towards common organisational goals, which is achieving beyond excellence.
What was the capacity utilisation at all the three plants during 2012?
The capacity utilisation for each plant per operating day in 2012 was as follows:
• Ammonia plant – 103.04 per cent
• Methanol plant – 100.82 per cent
• Urea plant – 108.92 per cent.
What were the export statistics for 2012? How does it compare with 2011? What is the projection for 2013?
A total of 1.106 million tonnes of product was exported in 2012. The exports in 2011 were 1.17 million tonnes and the target for 2013 is 1.17 million tonnes.
2012 proved to be another challenging and quite demanding year for world markets but GPIC has still managed to conclude it on a promising note both in terms of achieving attractive netbacks on all its products and also in terms of volume of products exported to world markets.
![]() |
The GPIC board of directors |
During 2012, the company was able to fully achieve its marketing objectives by successfully meeting customer expectations especially with regards to the quality and timely delivery of its products. Although 2012 marked the biggest plant turnaround year in the history of GPIC, it still managed to export a total of 1,105,093 tonnes of ammonia, urea and methanol to the world markets, which included 62,566 tonnes of ammonia, 630,602 tonnes of urea and 412,925 tonnes of methanol.
The above results have only been made possible through the intense dedication, hard work, sound planning and close coordination of the company’s marketing department with both the marketing partners in Sabic and PIC along with all the other stake holders.
For 2013, GPIC is fully geared up and looking forward to achieving premium returns on the company’s exports by capitalising on the markets created by the reduction in the supplies of the major consuming countries and at the same time exploring new and attractive opportunities and markets for its products through its marketing partners.
How much of CO2 is being treated daily after the commissioning of the Middle East’s first carbon capture system by GPIC?
As part of our environmental drive GPIC installed a carbon-dioxide recovery unit, in December 2009, at a cost of $52 million. The unit recycles 450 tonnes of carbon-dioxide per day and despite the fact that GPIC installed this unit as part of its environmental drive to reduce carbon-dioxide emissions, it has yielded an IRR of over 22 per cent. The unit recovers the carbon dioxide from the flue gases of the methanol plant and uses it to increase the production of urea and methanol by 80 and 120 metric tonnes per day respectively.
201,000 NM3 of CO2 is being treated daily after the commissioning of the Middle East’s first carbon capture system.
How much worth of capex projects were undertaken by GPIC in 2012? What were the main projects undertaken?
GPIC carried out $41.711 million worth of capex projects in 2012. The main project undertaken was the turnaround which was the largest in GPIC’s history. This included and was not limited to the following:
1) Replacement of:
• 13.3 kV switch board at substation 2;
• Primary reformer tube in the ammonia plant;
• Ammonia converter basket;
• Critical heat exchanges;
• Major catalysts;
• Field instruments and critical control valves;
• Auxiliary service panel boards; and
• bucket elevators.
2) Carried out a urea plant reliability enhancement project;
3) Installing urea handling PLC update project; and
4) Installing a new steam boiler in the utilities plant.
What were the tasks undertaken by the maintenance department in 2012 to improve reliability? How many orders were undertaken for preventive maintenance, corrective maintenance and modifications?
The main task was the execution of a major turnaround in a safe and reliable manner.
• Preventive maintenance orders: 7,807 (Routine – 6,276 + Turnaround – 1,531)
• Corrective maintenance orders: 3,189 (Routine – 2,013 + Turnaround – 1,176)
• Modification orders: 218 (Routine – 78 + Turnaround – 140)
Regarding profits what was the scenario in 2012? How much profit did the company post in 2011?
In 2012, our focus was to safely and efficiently execute the biggest maintenances Turnaround in GPIC history, which took place during November. We had over 4,000 contractors at the GPIC site and implemented maintenance and capital investment projects exceeding $85 million to ensure that production continues to be safe and reliable. That was achieved within time and budget but most importantly without any accident or environmental incident. Due to the planned shutdown our net profit was lower than 2011.
However our sound business module enabled us to continue the strong financial performance and post a profit of $211 million against $265 million in 2011 which is a 20 per cent reduction due to the loss of production during the planned turnaround. In other words, if the profit in 2011 was adjusted for the loss in production during the shutdown, financial performance in 2012 was in line with that of 2011.
The secret of our success is very simple, we are very passionate and relentless in issues relating to health, safety and care for the environment. We never relax and always strive to improve. We seek small but steady improvements which have significant cumulative effects rather than leaps and bounds. The reason why we do this is because we want to ensure sustainability and create a culture in all our employees (old and new) of this passion.
How did GPIC enhance and strengthen its health, safety and environmental (HSE) management systems in 2012? What were the achievements?
At GPIC safety is not regarded as a commodity but a necessity for the sustainability of our operations. With that operational excellence becomes the fruit of such a strategy and programme.
Technically, it is the attention to details that we give to every aspect starting from design, engineering, and quality control to execution. This is complemented later on by strict operation and maintenance management to ensure maximum reliability of the equipment and plants. The environment for us is something else. We do not believe in restricting ourselves to adhering to legislations and standards only.
We always stretch ourselves to go much beyond the requirements. Our efforts to enhance environmental protection is not limited to our complex or locally but also globally; the launch of International Dilmon Environmental Award (IDEA) in 2006 is but one testimony. To win the Kingdom of Saudi Arabia Best Environmental Management Award for two consecutive years in 2006 and 2008 is also another recognition for our environmental commitment.
We continuously strive to enhance our SHE Management system and to do this we bring in outside auditors from the “Responsible Care”, British standards Institute, British Safety Council and Insurance Companies. They check the effectiveness, robustness and resilience of our SHE Management systems. We listen to their advice on areas of improvement and utilising best practice. We benefit from these world renowned experts and put into place their recommendations. This enhances our safety performance and we are now very close to exceeding over 15 million man hours without Lost Time Accident. We bench mark our SHE system and received the prestigious Royal Society of Prevention of Accidents RoSPA Chemical Sector Award for 12th time and the British Safety Councils International award. I am pleased to say I gratefully received a personal Safety award given by Lord Jordan of RoSPA for services to promote SHE. Which I accepted in recognition for all the hard work carried out by GPIC’s employees and leaders in relation to SHE.
How much has GPIC invested so far for the objective of improving safety, reliability, performance and preservation of the environment?
GPIC invests heavily in time, effort and money on these issues, an investment of $63.5 million in 2011, $41.7 million in 2012 and an allocated budget of $38.7 million for 2013. We pride ourselves in being a “Responsible Care Company” and both the Board and Management recognise that investment in these areas is good for business. The reasons being we have a high quality workforce, working in a world class safe working environment. We look after all the stake holders and our customers want to deal with a dependable world class company with a sound reputation for safety, health, environment and community.
How many man-days did turnaround 2012 achieve?
Maintenance department statistics are as follows:
• Direct hire manpower – 43,891 man days
• Package contracts – 21,478 man days
• Vendor service – 531 man days
• GPIC employees – 16,899 man days
How much did the in-house spare part manufacturing programme save for the company in 2012?
GPIC started the programme of making specific spare parts especially the ones which have long lead time. During 2012 the actual savings were BD200,893 ($ 532,366).
Link for Ammonia exports by destination 2012
Link for Urea exports by destination 2012
Link for Methanol exports by destination 2012