
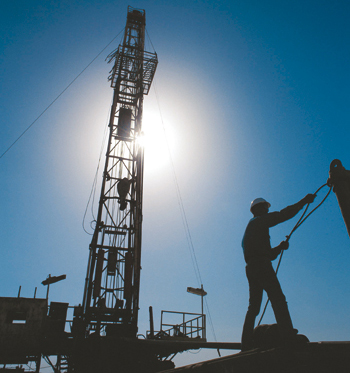
BAPCO’S commitment to achieving a zero-injury, zero-incident work environment was reflected in a range of initiatives in 2014 which sought to reinforce the company’s ‘no compromise’ safety culture and sharpen the safety awareness tools and innovations at its disposal.
Unfortunately a serious of events early in 2014 led to several Lost Time Injuries (LTI). These were deemed unacceptable and steps were taken to refocus the organisation on the importance of using OSOOL Bapco and the 4 Keys to Safety, the basic building blocks of the company’s Operational Excellence (OE) Management System, to revert the disappointing trends.
The fruits of this organisation-wide endeavour was apparent when Bapco and its contractor employees completed five million man hours without LTI in November. The strong focus on personal safety culture ensured the year ended with six million hours worked without LTI.
To reinforce its vigilance and effort to prevent injuries, Bapco will continue to channel its efforts towards deploying Behaviour Observation Observes Safe Trends (Boost), the 4 Keys to Safety, and OSOOL Bapco, which are proven operational excellence tools, and will treat them as part of daily activities.
Hand safety campaign: Bapco’s Environment, Health and Safety Committee (EHSC) initiated a hand safety campaign in February in response to statistics showing that the number of hand injuries had increased since the last campaign in September 2012. In 2011, hand injuries accounted for 36 per cent of all injuries; in 2012 it was 42 per cent and 41 per cent in 2013. The 2014 campaign sought to enhance awareness among employees and contractors of hand safety, and highlighted its importance in on-job and off-job activities, as well as the importance of wearing the correct Personal Protective Equipment (PPE).
Slips/trips/falls campaign: In line with Bapco’s commitment towards a realistic target of zero incidents and zero injuries, a comprehensive campaign was conducted in the fourth quarter of the year to raise awareness among employees, their families and contractors of slips, trips and falls (STF). Held under the theme ‘We Know Better’, the campaign featured quizzes, information sessions and competitions to increase awareness of STFs, a major cause of head and back injury, broken bones, lacerations and cuts, sprained muscles and potentially death.
More than 770 employees responded to a survey held before campaign launch, with the aim of measuring employees’ knowledge and understanding of STF causes and prevention. Safety videos, emails and mail-drops were distributed to employees with video clips on STF safety. In addition to inspections being carried out throughout the company, Boost observations, conducted since the beginning of the campaign, focused mainly on STF.
The company’s new Crisis and Emergency Response Plan (CERP) kicked off with two emergency response tabletop exercises in February for the Incident Management Team (IMT) and Level 1 response. These exercises were part of preparations for the company’s migration in June from Major Incident Procedure (MIP) to an Incident Command System (ICS)-based CERP.
A series of intensive training courses, including a full-day CERP exercise, were also held to support the new CERP, with employees participating from the IMT and Crisis Management Team (CMT) Levels 1, 2 and 3.
The new CERP greatly enhances Bapco’s ability to manage all types of emergency, centralising crisis control, offering logistical support for all involved, and providing an internationally-recognised organisation structure for sustaining the business after the event.
The company successfully met the requirements of the third periodic audit OHSAS18001:2007 management system by DNV in February, thereby reconfirming that the organisation’s Occupational Health & Safety (OH&S) management system is capable of meeting applicable statutory, regulatory and contractual requirements.
OHSAS18001 is designed to enable organisations to control OH&S risks and improve their health and safety performance, in addition to controlling risks, thereby reducing accidents and ill-health; preventing personal injury claims; avoiding damage to equipment and loss of productivity.