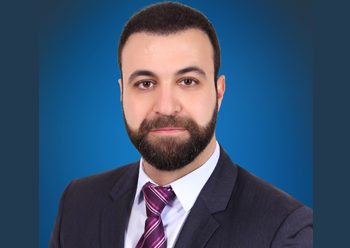
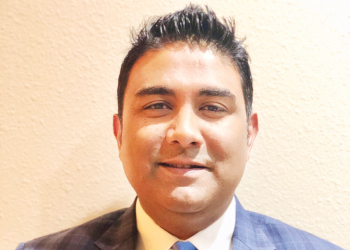
BD Energy Systems, LLC, a world leader in plant revamps and modernisations, had a profitable 2018 with projections and forecast for the 2019 fourth-quarter showing similar success for FY 2019 and a strong carryover of project backlog to 2020.
The company is in discussions with all major producers in the Middle East Region – ammonia, methanol, hydrogen and ethylene producers – sharing its new technologies that have been successfully implemented in plants around the world. Potential work is in the bidding phase and BD Energy Systems is looking forward to supporting producers in the region in a manner similar to the successful revamp projects it has executed globally, says Praveen Reddy, Director of Sales & Business Development, BD Energy Systems.
Having successfully executed more than 190 projects ranging from process studies to turnkey revamps on furnaces and syngas plants, BD Energy Systems has now established a regional presence through its local partners in Saudi Arabia, Kuwait, Bahrain, Oman and Qatar.
'We have executed projects globally and managed them successfully with support from our corporate office in Houston, Texas, USA and our European office in Milan, Italy. The furnace revamp focus includes Steam Methane Reformers, Ethylene Cracking Units, and Refinery Fired Heaters. The execution philosophy of each project was bespoke to each furnace and syngas plant, meeting local code requirements and focusing on efficiency improvement, production increase, reliability improvement, NOx emissions, etc.,' he says.
Among the flagship projects BD Energy Systems implemented recently in the region is the QAFAC or Qatar Fuel Additives Company (2018 – 2019) project. The plant was required to reduce its NOx emissions to meet local regulations. BD Energy Systems was contracted to conduct a process study as part of a Feed Phase to review options to reduce the NOx emissions from the methanol plant steam-methane reformer. This study was successfully executed with a recommended path forward using a Selective Non-Catalytic Reduction (SNCR) system. BD Energy Systems provided the detailed engineering, supply of equipment, construction advisory services, and start-up/performance test advisory services in 2019. Plant targets and contract guarantees of NOx emissions < 62.5PPM and NH3 slip < 5PPM were successfully achieved.
In addition, BD Energy Systems has begun to support Sabic on energy saving studies for their petrochemical plants.
On the technology side, in addition to successfully executing the installation and performance of the SNCR system at QAFAC to reduce NOx emissions, BD Energy Systems also installed the Blasch Precision Ceramics StaBlox flue gas collection tunnel system with the BD Energy Systems patented Tunnel Optimal Performance (TOP) flow distribution technology in two ammonia plant primary reformer furnaces in North America.
The firm was also awarded two significant EPC projects -- a turn-key revamp project with a major ammonia producer in Europe and a turn-key GTL plant revamp/revival project in Trinidad and Tobago.
TYPICAL EPC SCOPE OF WORK
BD Energy Systems turn-key EPC scope of work for revamps and modernisations of high temperature furnaces and syngas plants typically begins with a detailed process study or plant evaluation from BD Energy Systems and Parrish Process Services (part of BD Energy Systems, LLC). For the plant evaluation, operating data and physical data of all critical equipment in the plant is used to carry out a detailed simulation of the complete plant using our proprietary software. Benchmarking of the current plant performance is provided with recommendations as to how to reach efficiency-energy savings, production, or equipment reliability targets in a detailed report.
The plant study report also encloses critical elements from the process evaluation, such as plant heat and material balance, steam balance, and energy use calculations, as well as the performance evaluation of the furnace, exchangers, CO2 removal system, turbines, compressors, catalysts, etc.
Budget estimates to perform the detailed engineering, material supply, and construction are provided in the report along with the anticipated return-on-investment and payback based on product market value and feed pricing. The plant evaluation identifies the proper steps so the economics can be favorable in executing the EPC projects. Future phases include FEED; detailed engineering and supply; construction activities; and commissioning and start-up including test-run to meet performance guarantees. BD Energy Systems provides performance, mechanical and emission guarantees (if applicable) with execution of EPC work.
SYNGAS PLANT RELOCATIONS
BD Energy Systems is also involved in plant relocations where a process study is the first phase as indicated in above section EPC scope of work to define the plant performance and to carry out due diligence to identify the key equipment that needs to be replaced or modified to reach efficiency or production targets. An assessment of the value of the plant assets, presently in running condition and future assessment with improved efficiency and targeted production are incorporated into the commercial proformas taking into consideration potential overhead costs at targeted location, relocation & logistics cost, capital equipment investment, refurbishment equipment cost, construction, onstream factor, utilities - water, electricity, etc. showing complete investment cost and payback period. Typically, the relocated plants can start production 18-24 months in advance of a grassroots project.
CHALLENGES – TURN-KEY EPC REVAMPS
'Some of the challenges faced amongst many seen in revamp, modernisation, and relocation of plants is the fact that we are working with existing and old plants which first started up as early as 1968,' notes Reddy.
The existing plants have either undergone revamps or replaced equipment at least a dozen times from plot layout, piping tie-ins, elevations of piping, etc. so the original drawings do not match. Hence, BD Energy surveys the plant equipment and uses 3-D laser mapping for a true 'as built' reference. Additionally, it uses high resolution drones that photograph vertically and overhead (for a virtual plot plan) of potential plants to be relocated.
Choosing a correct piping contractor who can be used through the end of mechanical completion is key during the construction phase. A low-cost piping contractor will not only result in poor productivity, quality, and quality control (X-rays and Hydrotest) but also will lead to time delays with dramatically escalated costs – impacting not only piping but crane time, scaffolding, I&E, insulation and painting as well.
Existing equipment that is to be reused or refurbished was initially designed and fabricated for codes such as ASME, NFPA, etc. When equipment is refurbished or revamped, it must undergo inspections and evaluations to consider any fabrication code changes and API fitness for service and end of life assessments. The destination site may require a code review and a 'pedigree' of documentation to license or recertify to reuse.
BD Energy Systems’ ability to continually execute projects successfully, within budget and on time comes from the depth and experience of its personnel who have worked with various licensor and engineering companies; its flexibility towards a variation of commercial models; its partnerships and collaboration with major sub-contractors and suppliers; its manner towards lessons learned and future risk mitigation; its ability as a private company to react quickly and effectively when facing critical schedule, commercial, and financial issues; its willingness to provide performance and mechanical guarantees; and use of local resources via its local partners for execution of revamp projects.
TECHNOLOGIES
BD Energy Systems has brought to the region NOx reduction technologies and equipment technologies to improve the reliability of petrochemical/syngas furnaces.
Super Radiant Coil (SRC) Technology: The SRC technology patented by Pycos Engineering SRL is marketed and supplied by BD Energy Systems. SRC technology is applied in Ethylene furnaces where it serves to reduce coking and thereby increase run lengths (between decoking), via enhanced heat transfer. The result is that the desired bulk cracking gas temperature can be achieved with a lower film temperature, reducing the degree of over-cracking at the inside film, improving the yield of desired products, and in turn, less coking.
'Top' Tunnel Optimal Performance Technology: The 'TOP' Tunnel Optimal Performance is applied in top-fired design steam methane reformer furnaces. Conventional tunnels incorporate physical features that constrain design efficacy resulting in non-uniform flue gas flow both along the length of the tunnels and among the tunnels. Non-uniform flue gas flow has been correlated to non-uniform catalyst tube convective heating, varied tube temperatures, and early tube failures due to localised overheating.
BD Energy Systems have developed a new patented design to achieve near-perfect radiant flue gas flow uniformity and improved heat transfer uniformity. The TOP design results in reducing the tube metal temperature (TMT) spread and allows operators to safely increase the outlet process temperature and in turn improve production rates while still maintaining the maximum TMT at safe levels. BD Energy Systems uses the Blasch Precision Ceramics designed StaBlox™ system, having mullite bonded high alumina refractory components that include unique features incorporating the TOP design within the StaBlox™ system and allowing the installation of the entire tunnel system without mortar, utilising interlocking features.
TGM – Tube Growth Monitor System: The Tube Growth Monitor (TGM) system can be applied in all high temperature furnaces. The TGM system measures the thermal expansion of reformer tubes, giving accurate information regarding operating conditions relative to tube metal temperatures. Further, because the TGM system detects changes in reformer tube metal temperatures earlier than current instrumentation that provides feedback to the DCS, the TGM system alarm trips before dangerous levels are reached. With early detection this allows for effective protection against tube overheating incidents, provided operators respond appropriately to the information fed by the TGM to the DCS in a timely manner. The TGM temperature alarms are readily apparent to plant operators and will prompt immediate action. Using the relationship between temperature and tube thermal growth, the TGM System provides instantaneous readings of average tube metal temperatures of each tube or set of tubes on which a sensor is installed on spring hanger support system. This allows for more timely responses to upsets in order to protect the catalyst tubes from damage. With enough sensors, operators can also tune the firing in the radiant section to provide more uniform heating of catalyst tubes.
Feed Gas Saturator Coil: BD Energy Systems has an improved Feed Gas Saturator coil design used in steam methane reformer furnaces. This system can be a very effective means of improving reformer and plant efficiency through vaporisation of process condensate at reduced partial pressure. This allows recovery of low level heat from the cold end of the convection section (with thermal efficiency sometimes reaching as high as 94.5 per cent) and reduces the amount of required process steam added the feed. Depending on the particular plant, the reduction in process steam requirement may allow for reduced firing or elimination of a boiler.