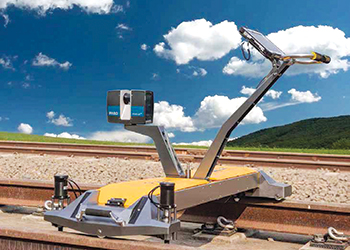
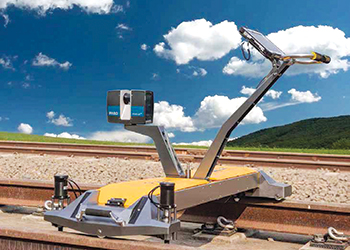
As China vigorously develops intercity high-speed railways and urban rail transit, a key concern is safe production and operation management.
Government departments and safety monitoring organisations are sparing no effort to enhance sustainable development capabilities.
To help the sector, Guangzhou South High-Speed Railway Surveying Technology, also called South High-Speed Railway, is deploying precision surveying technology and equipment for high-speed railways, subways, tunnels, dams, slopes, etc. It also provides special precision measurement solutions for mines, ports and pipelines.
To further its objectives, the company has established the South Special Precision Surveying Institute, which undertakes related independent research and development of software and hardware.
When doing tunnel excavation using drilling and blasting methods, over or under excavation becomes inevitable. The regulation about quality and safety of railway construction projects implemented on January 1, 2018 states the importance of initial liner and lining thickness. If not dealt with in time, these problems will not only increase the construction cost of the project, but will also have a serious impact on the construction quality and operational safety of the tunnel.
![]() |
Faro Focus Laser Scanner ... accurate measurements |
Water seepage, lining cracking, concrete peeling and falling off will also occur in the completed tunnel due to geological conditions, material performance degradation, and train vibration, resulting in safety hazards. Therefore, safety detection has become an indispensable procedure for tunnel construction.
Due to the special nature of tunnel construction, continuous operation is required during excavation, making it difficult to have a long stoppage for surveying. This makes real-time survey a problem.
With firm roots in the railway industry, the South High-Speed Railway began the exploration of track detection years back.
"We started research and development of track detection equipment in 2008. After 10 years of technology accumulating and depositing, we established a formal Monitoring Division in 2018," says Li Zhongli, the Manager.
The company offers a three-dimensional solution that can cope with the harsh working environment in tunnels. It has also developed a track-moving tunnel detection system based on the Faro three-dimensional laser scanner for metro and high-speed railway tunnel inspection during the operation and maintenance period.
In 2018, the South High-Speed Railway successively purchased two Faro Focus 3D laser scanners, FocusS 350 and FocusM 70, and launched a mobile tunnel detection system based on the Faro FocusS 350. This system detects in a dynamic and uncontrolled manner with reduced dependence on the design data. It can efficiently obtain point cloud data of the tunnel and provide great data support for tunnel detection, greatly improved the work efficiency.
CHALLENGES IN TUNNEL DETECTION
![]() |
The Faro scanner can finish scanning the inner wall of the tunnel in minutes |
Also, at the stage of excavation and initial lining, the four walls of the tunnel are extremely unstable, and there is also risk of rock falling off from the tunnel’s vault. Moreover, a dim construction site, poor ventilation and dusty air, uneven road and dark trenches adds to the environment’s harshness.
Before 3D laser scanning technology was used, surveyors usually relied on their own experience combined with a total station device to detect over- or under-excavation.
They would often observe sags and crests inside the tunnel with the naked eye and use the total station to make cross-section surveying at the obvious bulge. However, both manual estimation and surveying with total station has limitations.
Manual observation cannot give accurate and real data, and misjudgment often occurs. On the other hand, although the total station device can give accurate data, the number of points selected in the process is limited and the interval of sections is large. Therefore, the surveying results might not conform to actual site conditions.
The South High-Speed Railway uses the Faro 3D laser scanner mainly for tunnel detection during tunnel construction, operation and maintenance. During construction, the amount of concrete can be calculated by over- or under-excavation analysis and point cloud data comparison to provide guidance for safe construction. At the period of operation and maintenance, it can provide real and reliable data support for safe traffic by detecting tunnel deformation and convergence diameter.
For detection of over- or under-excavation, usually the ground track has not been laid yet by then. The 3D laser scanner is set in the tunnel and scans the segment, which needs to detect over- or under-excavation. At the same time, the total station is used to collect spherical prism mirror coordinates for late conversion for absolute coordinates.
After the data acquisition is completed, the point cloud data and the tunnel design model with absolute coordinates are both imported into the tunnel three-dimensional monitoring software, and the tunnel over/under excavation analysis and concrete amount calculation can be performed to provide effective safety guidance for tunnel construction.
The Faro scanner scans very fast, recording up to 976,000 points per second, and can finish the scanning of the inner wall of the tunnel in minutes. This not only improves the productivity of the surveyor on site, but more importantly, it can restore the inner walls of the tunnel to the most extent, thus avoiding omission of information and saving time, labour and financial costs.
With a maximum scanning distance of up to 100 m in the tunnel, the FocusM 70 is fully capable of meeting the scanning needs at the excavation phase. "After entering the site, it takes only 3-5 minutes to complete the scan," says Zhongli.
For tunnel detection at the period of operation and maintenance, the South High-Speed Railway uses the mobile tunnel detection system based on Faro three-dimensional laser scanning technology.
The mobile laser scanning technology acquires data faster than the traditional station scanning technology, and does not require data splicing. It is more suitable for tunnels with a short stoppage time at the period of operation and maintenance.
With 180 m of measurement verification, it has a mobile acquisition speed of 1.4 kmph, and only needs 2-3 people for the field operation. At the same time, its relative accuracy of point cloud data can be up to 3 mm.
With the point cloud data being analysed and processed by software, the surveying results of the cross-section analysis, convergence diameter, clearance section and orthophoto of the tunnel structure can be obtained.
Currently, the South High-Speed Railway is cooperating with Shenzhen Construction Engineering Quality Inspection Center to carry out operation and maintenance detection for Baoan Airport section (non-operational) of Guangzhou-Dongguan-Shenzhen Intercity Railway using the mobile trolley surveying technology developed by combining the Faro scanner.
The Shenzhen Construction Engineering Quality Inspection Center provides technical support to the Construction Administrative Department, which enforces concerned laws, supervises and manages the quality of construction projects, and coordinates with the municipal quality supervision organisations.
On the site, an engineer of the Geotechnical Department of the Shenzhen Construction Engineering Quality Inspection Center said: "The scanning trolley has greatly improved the efficiency of track detection."
Speaking of subsequent technical improvements, the engineer said he hopes to further consider the influence of the slope on the fixed uniform speed and improve the accuracy of the mobile scanning, so as to obtain more optimized scanning results.
FARO is one of the world’s most trusted source for 3D measurement and imaging solutions. The company develops and markets computer-aided measurement and imaging devices and software for several vertical markets, including 3D Manufacturing, Construction BIM, Public Safety Forensics, Personnel, 3D Design, and Photonics.
Faro’s global headquarters is located in Lake Mary, Florida. Its European regional headquarters is in Stuttgart, Germany, and the Asia-Pacific regional headquarters in Singapore. Faro has other offices in the US, Canada, Mexico, Brazil, Germany, the UK, France, Spain, Italy, Poland, Turkey, the Netherlands, Switzerland, India, China, Malaysia, Thailand, South Korea, Japan, and Australia.