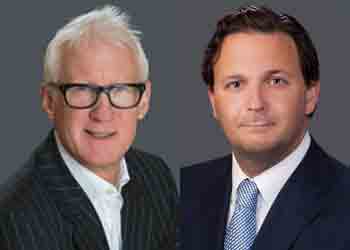
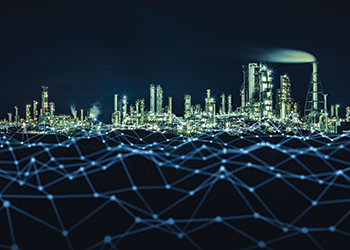
Oil and gas producers must constantly seek ways to reduce total cost of ownership to remain competitive in a post-Covid world. Smart universal marshalling can minimise downtime, simplify operations and deliver better TCO, Roger Highton, MTL Product Line Manager, Eaton, tells OGN
The oil and gas industry has traditionally been relatively robust in terms of its ability to absorb the effects of market fluctuations: but the global pandemic, coupled with calls to build back better and greener, means that the sector must look for permanent ways to cut costs and make the future price per barrel more palatable. Digitalisation and automation play a big part in improving efficiency and safety in the oil and gas sector. But for this data to be leveraged, it has to be collected, which is where marshalling comes in.
![]() |
Smart universal marshalling can deliver 30-50% space savings |
Traditional marshalling aims to provide reliable interconnections between field instruments and a central control system. It may include provision for intrinsic safety, signal conditioning, relay interfaces, surge protection and loop disconnect. While the task seems simple in principle, there are challenges to manage from the outset, because initial assumptions about I/O loops change during detailed engineering design.
Changing a marshalling system design is complicated and time-consuming. A typical cabinet will have 20 different marshalling components and may require up to eight interconnections on each loop. That means eight opportunities for a wiring error. A single change affects design drawings, Bill of Materials (BOMs) and cabinet layout.
Once a system is live, marshalling changes become even more complicated. Failure in a wiring connection has the potential to cause immediate and severe incidents, potentially triggering a plant shutdown costing millions of dollars. Eaton has developed Smart Universal Marshalling (SUM) to provide solutions to these challenges. They offer both practical and financial benefits while reducing risks — all of which contributes to an improved TCO.
• Standardisation: Smart universal marshalling solves the problem of complexity by reducing the number of different types of components. Traditional marshalling design considers each function as a separate entity. Smart marshalling allows for the integration of these functions into single components. For example, one MTL SUM5 universal ADIO isolator module can replace 20 different MTL4500 single-channel modules. Standardised modules reduce the number of items on a Bill of Materials for the same reason.
Standardisation comes into its own when design changes occur during detailed engineering. Replacing modules or adding functionality after the conceptual phase adds uncertainty to a project. This uncertainty can result in overruns and, therefore, delays in productivity. Using standardised modules allows engineers to make changes to the system design without changing module specifications.
• Simplicity and compactness: Smart universal marshalling eliminates the need for separate cabinets for each function and uses modules to make design changes much easier to handle. Changes are effected simply by switching out standard modules for different functionality. This saves time during installation and commissioning, as well making changes of use easier and less time-consuming to accommodate during operation.
![]() |
Eaton’s MTL SUM5 ... compact design |
Smart marshalling solutions are also compact. The design of standardised modules caters for maximum packing density. Two or three columns fit into each side of an 800 mm wide double-sided cabinet, providing all marshalling functionality for 512 or 768 channels. More modules per cabinet mean fewer cabinets in total – saving valuable space and reducing weight on production platforms.
• Flexibility: Oil and gas production facilities must be able to respond to changes in market demands or supply chain disturbances quickly. Marshalling systems must, therefore, allow changes to configuration without extensive rewiring and delays. An ideal marshalling solution also has connectivity to 5G and Artificial Intelligence (AI) technology and integrates seamlessly with automation systems. Traditional marshalling solutions cannot meet these requirements, but smart marshalling solutions can.
The MTL SUM5 allows for changes to module configuration in the cabinet. There are fewer hardware changes required when new designs or operational changes are needed. The modular infrastructure also makes it easy to add a new component to the system without rewiring.
CONTRIBUTION TO TCO
• Initial cost: Smart universal marshalling can deliver space savings of between 30 and 50 per cent compared to traditional marshalling. Eaton has worked with partners to quantify savings in initial costs for smart marshalling solutions. An 82 per cent reduction compared to traditional marshalling solutions is possible.
• Operational costs: Both the hardware design and simplified maintenance associated with smart universal marshalling can deliver significant savings. Comparisons of operational costs using traditional marshalling versus smart marshalling indicate a 65 per cent saving can be achieved, due to reduction in spares holding, lower air-conditioning needs and simpler maintenance processes.
![]() |
MTL SUM5’s modular design delivers 65% cost savings |
In addition, a 65 per cent reduction in spare component types means a lower stock holding and more efficient procurement process. Maintenance technicians benefit from reduced complexity of standardised cabinet designs. Each terminal holds its own configuration information, making it easy to swap out modules seamlessly — all of which lowers the risk of human error during maintenance.
• Real estate cost: Space is at a premium in oil and gas facilities. Centralised control rooms are generally built to exceptionally high blast-proof specifications, making them an expensive investment. Reducing the number and size of marshalling cabinets reduces the requirement for building space and, therefore, the capital cost.
But it is not only the cost of the building itself that is a factor. More cabinets require more cables, a larger floor area, and greater air-conditioning needs. Marshalling cabinets require temperature and humidity control to prevent damage to electronic equipment or corrosion that impacts loop integrity. All these factors add to operational cost.
Eaton calculations show a saving of 69 per cent in terms of end-user costs for a smart marshalling project versus the traditional solution. Most of these savings come from the reduction in cabinet space required.
• Lowering the risk of an incident: Connection failures and human error are the most common cause of incident for traditional marshalling solutions. They can result in anything from unplanned downtime to a major incident (with all the reputational, legal, environmental and safety aspects that ensue). Smart universal marshalling lowers the risk by simplifying the system to minimise the opportunity for error.
Eaton’s MTL SUM5 meets ATEX, IECEx and North American certification requirements, making it suitable for international use. It is designed for location in Zone 2 hazardous areas and has a wide ambient temperature operating range. Smart marshalling is, therefore, a viable solution for even the harshest operating conditions.
CONCLUSION
The oil and gas industry must look for more permanent ways to cut costs and make the future price per barrel a little bit more palatable if it is to retain market share. Smart universal marshalling meets this need through simplifying system design, installation and maintenance. It is no exaggeration to say that Eaton’s MTL SUM5 offers TCO benefits while enabling the kind of flexibility and connectivity that the oil and gas sector requires to survive in a post-Covid world.