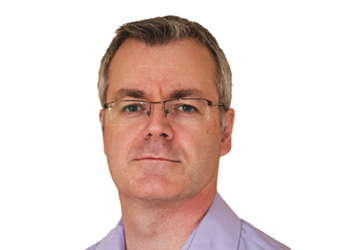
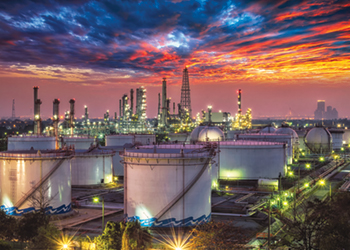
Good inspection programmes and corrosion monitoring are necessary to ensure safe and continuous operation, and OLI has developed the technology and expertise to continuously monitor for corrosion issues, Ezequiel Vicent, Senior Applications Engineer and Consulting Lead at OLI Systems, tells OGN
Process reliability is key to the safe operation of a successful, profitable crude refining plant since unplanned downtime can result in millions in lost production dollars.
The occurrence of corrosion is a large contributor to reduced operations that result in higher costs. In fact, according to NACE, the annual cost of corrosion in the oil and gas industry (upstream and downstream) accounts for $5.1 billion.
To sustain reliability within the plant, good inspection programmes and corrosion monitoring are necessary to ensure safe, continuous operations. Risk-based inspection (RBI) programmes are powerful tools to ensure mechanical integrity of equipment and pipelines. While RBI mitigates risk, these are mostly physical inspections that require equipment to be offline lowering productivity and operations efficiency resulting in higher costs.
In the past few decades, methods have been developed to monitor corrosion non-intrusively, such as X-ray imaging of piping systems that identify wall thickness loss, or online sensors that measure thickness in real time.
These non-intrusive methods, either through inspection or real-time data generation, help identify corrosion potential and allow refiners to constantly monitor for corrosion or erosion.
However, these methods do not provide operators with the precise indicators for the onset of corrosion reason, or prescriptive insights on how to mitigate or avoid corrosion.
OLI Systems provides refiners with the ability to accurately predict the onset of corrosion along with the ability to identify corrosion potential and understand the chemical reactions that cause corrosion inside pipes.
Scientist and engineers who have access to OLI Studio and OLI Flowsheet: ESP can use process simulation to predict the formation of corrosive environments and protective films; they can also develop IOWs (integrity operating windows) for a broad range of process conditions.
These process models are ideal to identify where and why chemical corrosion is happening under a certain operating envelope.
Engineers can then identify operating envelopes that mitigate (or entirely avoid) corrosion while ensuring profitable operations.
NEXT STEPS IN CORROSION MITIGATION
OLI understands the benefit of continuously, and automatically, running these models to provide operations with current information on corrosion potential and predict how changes are affecting corrosion and reliability of the system in real-time.
OLI Systems, through the use of cloud enabled APIs, has developed the technology to continuously monitor several applications in oil and gas, chemicals, and related industries. One example of these applications is the formation of the Ionic Dew Point (IDP) in the crude unit overhead system that is used to predict the corrosion behavior.
![]() |
Figure 1: OLI Systems API powered Overhead Corrosion Monitoring tool |
For example, the atmospheric tower suffers from corrosion on the overhead line leaving the tower and into the overhead condensers.
This corrosion is due to molten salts that form when a neutralizing amine meets HCl in the vapour phase.
In certain conditions the molten salt formation temperature (IDP) may be higher than the operating tower top temperature, depositing an electrolytic, highly corrosive, liquid salt on the bottom of this pipe.
Therefore, it is of upmost importance that refineries enable their technology to deliver a solution to understand the conditions at which the IDP forms to assess the exposure of the atmospheric tower overhead to a corrosive environment n.
The API can calculate the optimal dosage rate for the neutralizing amine that will avoid a molten salt formation issue on the overhead line, while protecting the rest of the equipment from aqueous, acidic corrosion (due to HCl condensation in the aqueous phase).
The software also calculates the per cent ‘free water’ left based on the wash water injected by the refinery.
This value is important because operators need free water to dilute the salts and concentrated aqueous phases that form at the overhead condensers.
More importantly, the API can generate optimal wash water injection rates to both ensure proper aqueous phase dilution and conserve water.
The values, graphs, and notifications encircled with orange in Figure 1 are direct outputs from the OLI API displayed alongside several of the inputs to the model gathered automatically from the plant’s data historian and LIMS system.
The overhead line that leaves the tower top section to the wash water injection point is the most susceptible to IDP corrosion.
In this scenario, corrosion is avoided by having an IDP lower than the operating temperature of the overhead (124 deg C IDP versus 143 deg C operating temperature).
The OLI monitoring solution generates IDP trends, as well as alerts when it identifies the tower operations are close to a corrosive environment (where the IDP is less than the Tower Top T by a couple of degrees) or if it crossed the threshold and a corrosive molten salt phase formed.
Armed with this information, operators and OLI can build analytics that compare optimal neutralizing amine injection rate versus actual injection rate, create KPIs around chemical savings, increase water usage efficiency and enhance reliability.
Continuously monitoring for overhead corrosion not only enhances asset reliability and increases site safety, but it helps in preventing unplanned shutdowns.
A shutdown due to overhead corrosion of the tower top line can shut down the entire crude unit for up to 10 days. At $10 per barrel, a 100,000 barrels per day refinery may lose up to $10 million of product revenue during that shutdown. This does not include labour or capital costs to replace equipment, in addition to the safety risks incurred during this period.
OLI has developed the technology and expertise to continuously monitor for corrosion issues while enhancing asset integrity and reliability, increasing safety, and protecting profits for oil and gas, chemicals, water and wastewater treatment, power generation and sustainability applications.
* Ezequiel Vicent, Senior Applications Engineer and Consulting Lead at OLI Systems, has 11 years of experience in the oil refining and petrochemical industry. He specialies in industrial and operational projects and is currently working on several refining process units - FCC, Alky, and Prime G.
With significant experience in the process modeling of refineries and polymer plants, Vicent has worked on many international projects (as project/process engineer and project manager, mainly in the Americas region).
Vicent was involved in a large Pinch Analysis project focusing on energy savings and carbon reduction. His activities included benchmarking of two large sites, analysis of current heat transfer networks and development of projects and Class 5 cost estimation to close the energy and emissions gap. He has also participated in multiple PSAs for the projects he developed as an advisor on the processes designed or technologies he recommended. Vicent has a BSChE degree from the University of Houston, Texas (US).