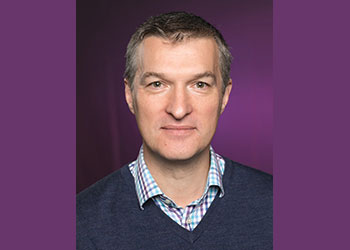
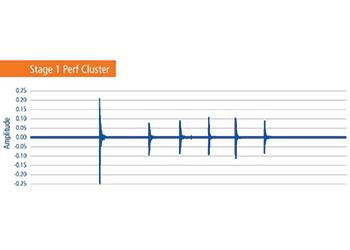
Packers Plus’ innovative ePLUS Retina technology uses an array of sensors to collect data from multiple locations on the wellsite, providing operators confidence in key decisions
At the intersection of precision, reliability, efficiency and cost, pressure and pump charts have been the best compromise in monitoring downhole operations. When uncertainty arises, hours or days can often be wasted on trial-and-error methods to solve operational problems.
Additional operational or downhole data can be gathered using microseismic monitoring, tracers, or cameras, but not all of these can be used concurrently with standard operations. Furthermore, they are generally too costly or time consuming to use on every well.
Finally, there is technology now available that allows operators to acquire that data at a minimal cost. 'The ePLUS® Retina™ monitoring system is a cost-effective way to verify downhole events and completion system operations, independently from other measurements,' says a spokesman for Packers Plus. Using Retina, operators can troubleshoot with accurate information during stimulation operations.
OVERVIEW
![]() |
Graph 1: Completion systems showing 84-100% sliding sleeve shifting efficiency |
Lost stages correlates directly to lost production and ultimately lost revenue. Similarly, shift sleeve malfunctions or ball failures during fracturing operations result in lower production and lower ultimate recovery.
This was demonstrated in a US Midcontinent study, which showed that successful ball seat landings correlate to higher production (Graph 1).
The ePLUS Retina monitoring system uses a proprietary array of sensors to collect and analyse signals from multiple locations on the wellsite. This portable system operates independently from conventional measurement equipment, without interfering with concurrent surface or downhole operations.
The Retina user interface combines real-time measurements from two different types of sensors: acoustic and pressure. A sampling rate of 10,000 data points per second offers more detail and accuracy than standard data van readings, providing operators with real-time confirmation and confidence in key decisions.
A better understanding of downhole operations can improve critical decisions, which affect a wide range of operations, and save valuable time and resources on site. The potential benefits of Retina are highlighted below:
IMPROVE SAFETY
The wellhead is a dangerous area, often called the red zone, where incidents can happen, due to high pressure, explosive potential, or sour gas. During plug-and-perf completions, real-time verification of charges detonating is valuable information. Perforation guns that do not detonate as expected are a major safety risk, particularly when they are brought to surface to be defused manually. Charges may fire unexpectedly if there are problems with the wireline.
In post-stimulation operations, confirming ball recovery and monitoring debris flowback is also valuable safety information. These confirmations reduce the need for personnel to enter the red zone and reduce the risk of accidents.
Increase multi-stage stimulation efficiency: Pressure signatures can be unclear because of low bottomhole pressure, varying pump rates, or low data acquisition rate, while other events are not detected using pressure. This results in an incomplete picture of completion operations.
A ball launch is a surface event that is not detected with pressure measurements. This event is only confirmed later with a pressure increase resulting from the ball landing on the seat. A ball launch can be seen distinctly on Retina charts.
By eliminating issues regarding surface events and providing verification of surface events with accurate, real-time information, operators can troubleshoot effectively and eliminate hours or days of trial-and-error problem solving.
Verify millout operations: In post-stimulation operations, operators can confirm ball recovery during flowback, or identify a milling motor stall or burnout. Motor stalls can occur if fluid circulation is lost, if jets are plugged, or if the torque is too high. Operators can use Retina to verify that flowback and millout parameters are achieving the desired results.
CASE STUDIES
![]() |
Graph 3: Retina shows the ball landing on seat and shifting, both within |
Charge detonation: Retina sensors are intrinsically safe and rated for use onshore or offshore in Zone 1, commonly known as the red zone. On a plug-and-perf completion in the Anadarko basin, Retina sensors recorded the detonation of a cluster of charges occurring within two minutes. This provided the operator with valuable certainty, in real time (Graph 2).
Ball launch: During Stage 5 of a 16-stage completion in Texas, ball launch and seat indications were not seen by either the data van or Retina. Not wanting to spend time shutting down operations and taking the wellhead apart to confirm the ball launch, the operator proceeded to stimulate the well as if the ball had landed. When the ball for Stage 6 was launched, it dislodged the Stage 5 ball that was still in the launcher. Both balls traveled down the wellbore, landing and shifting Stages 5 and 6 just 45 seconds apart. The two events for each stage were clearly captured by Retina. From this information, it can be inferred that Stage 4 was stimulated twice, and Stage 5 not at all. Moreover, the cost and revenue lost in one of 16 stages is significant.
With estimated drilling and completions expenses of approximately $5 million, each stage costs $312,500. Potential revenue from production is also lost, and reserves in the field remain untapped.
Sleeve shift and ball seal verification: Retina has been used to confirm ball seating and sleeve shifting events in a variety of ball-drop completion systems. During a third-party ball-drop completion, several actuation balls were verified to have extruded through the seat.
In each instance, the failure was seen as an abrupt decrease in pressure along with a Retina acoustic indication. This form of dual verification is only possible using the sensitive instrumentation specifically developed for Retina.
A ball failure results in a missed stage, and overall production is lost if the failure is not identified, and the stage is left untreated. Historically, operators have had to guess or spend time interpreting whether a lack of pressure was due to a sleeve not opening, a ball not seating, or a missing pressure signal. Using Retina, it is possible to verify any or all these scenarios and take corrective action, removing guess work and eliminating costly delays during fracture operations.
High sampling rate detects sleeve shift: During a completion in the Granite Wash formation in Texas, a ball landed on the seat and shifted the sleeve but was not detected by the data van (Graph 3).
Retina’s high-resolution sampling rate captured the events, showing that they both occurred within 0.4 seconds. This confirmation allowed the stimulation to continue without downtime.
Cemented limited entry stimulation: Retina was used to monitor a cemented limited entry ball-drop stimulation in the Sooner Trend of the Meramec formation in the US Midcontinent region. The Retina signatures gave the operator confidence that all sleeves in each stage were open before pumping the treatment.
CONCLUSION
Stakes are high during on-site operations. Operators want as much information as possible to be able to run a completion efficiently, and troubleshoot problems effectively and immediately, with minimal downtime.
The goal of Retina is to foster an environment for confident decision-making to save time and costs. Retina offers benefits in addition to visualizing well operations, including:
• Improving safety: By verifying perforation and mill out events, workers have fewer reasons to be in the red zone.
• Increasing accuracy and lowering costs: Detecting events with exact timing allows operators to both troubleshoot more effectively and optimize completions by using fewer resources.
• Reducing uncertainty: Independent confirmation lowers operational risk and gives operators the confidence to make decisions.