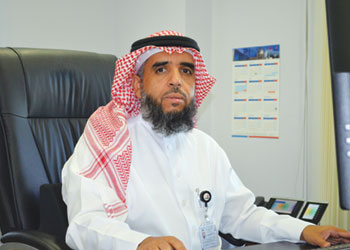
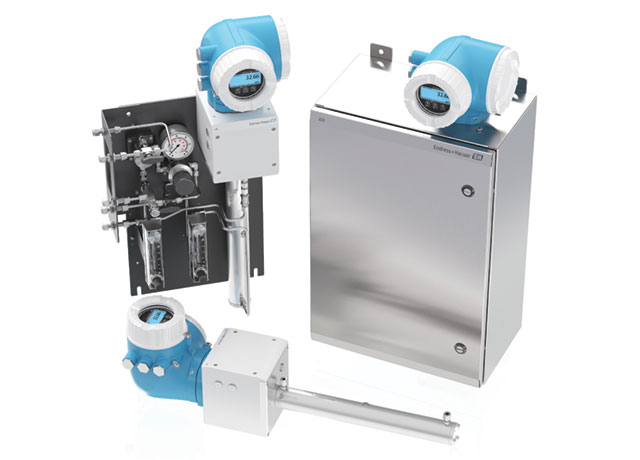
Tunable Diode Laser Absorption Spectroscopy (TDLAS) analysers utilise a laser absorption spectroscopy technique to detect and measure the concentration of analyte molecules (H2O, H2S, CO2, NH3, and C2H2) in process gas streams.
This basic technique has been applied to gas measurements since the invention of the laser over 40 years ago and is an ultra-fast and highly accurate technology for petrochemical plants, refineries, and gas processors.
Recent advances in semiconductor lasers have made the development of tunable diode laser analysers for process gas monitoring applications technologically and economically viable.
OPERATING PRINCIPLE OF TDLAS TECHNOLOGY
TDLAS analysers perform online, real-time measurements of impurities in process gas streams from sub-ppm (part per million) levels to percentage levels. The technology is widely used for measurements of moisture (H2O), carbon dioxide (CO2), hydrogen sulfide (H2S), ammonia (NH3), acetylene (C2H2) and other compounds.
In operation, process gas from a sampling probe is introduced to the sample cell of the TDLAS analyser. A tunable diode laser emits a light with a specific near-infrared (NIR) or visible wavelength that can be absorbed by the target analyte. The laser light enters the sample cell, passes through the gas, gets reflected by one or more mirrors, and is finally aimed into a photodiode detector.
A sapphire glass window isolates the laser and detector from the process gas. This design allows measurements to be performed with absolutely no contact between the process gas (and entrained contaminants) and critical analyser components. Analyte molecules in the gas sample absorb and reduce the intensity of light in direct proportion to their concentrations according to the Lambert-Beer law.
The system measures the transmitted laser intensity as a function of the scanned laser wavelength as depicted in Graph 1 and 2 in in Figure 1.
Graph 1 has no absorption and Graph 2 has significant absorption as indicated by the "dip" in intensity at a specific wavelength. To improve detection sensitivity over simple direction absorption spectroscopy (DAS), wavelength modulation spectroscopy (WMS) with second harmonic (2f) detection is employed.
The 2f signal is illustrated in Graph 3. WMS-2f can be 1-2 orders of magnitude more sensitive than DAS because it uses a lock-in amplifier to pick up the 2f signal in a narrow bandwidth while eliminating lower and higher frequency noises.
This approach significantly improves the signal-to-noise ratio supporting high-sensitivity measurements. The 2f signal is processed using advanced algorithms to calculate analyte concentration in the process gas.
![]() |
Figure 1 ... Graphs 1,2 and 3 |
OPERATING PRINCIPLE OF DIFFERENTIAL SPECTROSCOPY FOR SUB-PPMV MEASUREMENT
The measurement of trace level contaminants in hydrocarbons is a challenge while using TDLAS technology.
Endress+Hauser TDLAS analyser systems, powered by TDLAS technology, include a patented spectral subtraction technique that enables trace-level (sub-ppm) measurements of H2O, H2S, or NH3 to be made when a process gas sample contains very low levels of an analyte and background gas interferences.
Differential Spectroscopy (Figure 2) enhances the sensitivity of the TDLAS analyser to measure the sub-ppmv levels of analyte with better signal to noise ratio.
![]() |
Figure 2 … differential spectroscopy |
![]() |
Figure 3 … TDL analyser with multi-pass Herriott cell |
In operation, the TDLAS analyser performs a sequence of steps to obtain a "zero" or "dry" spectrum and "process" or "wet" spectrum that are used to calculate analyte concentration by spectral subtraction as depicted in Figure 3.
The dry spectrum is obtained by passing the process gas sample through a high-efficiency scrubber or dryer which selectively removes the trace analyte without altering the process gas composition and background absorbance.
The analyser records the resulting dry spectrum of the process gas and automatically switches the sample gas flow path to bypass the scrubber and collect the wet spectrum.
Subtraction of the recorded dry spectrum from the wet spectrum generates a differential spectrum of the trace analyte which is free of background interferences. The analyte concentration is calculated from the differential spectrum.
APPLICATIONS
![]() |
Figure 5 Cracked Gas Dehydration |
Cracked gas dehydration: Cracked gas exiting a caustic wash tower is saturated with water vapour. Water must be removed before the gas undergoes cryogenic fractionation to avoid formation of hydrates and ice.
Gas from the caustic wash tower is compressed and then cooled to remove as much entrained water as possible before it is sent to molecular sieve dryers. Molecular sieve (Mol-sieve ) dehydration dries the cracked gas down to < 1 ppmv H2O.
On-line monitoring of H2O: Multiple molecular sieve dryer vessels are typically operated in parallel with a piping system that allows a saturated adsorbent bed to be taken off-line for regeneration with heated gas. Monitoring H2O in cracked gas at the outlet of molecular sieve dryer vessels helps detect H2O breakthrough and prevents gas with elevated levels of H2O from entering downstream cryogenic separation equipment.
SOLUTION
Tunable diode laser absorption spectroscopy (TDLAS) is a technology that has proven highly effective for this critical measurement.
TDLAS analysers have an exceptionally fast response to changes in H2O concentration, an important performance characteristic for detecting breakthrough in molecular sieve beds.
Endress+Hauser patented differential spectroscopy technique enables detection and quantitation of sub-ppmv levels of H2O in cracked gas.
An integrated permeation tube supports automated validation checks to verify the analyser is operating properly during the extended periods of time when H2O is not present in the gas. Laser and detector components are isolated and protected from process gas and contaminants avoiding fouling and corrosion and ensuring stable long-term operation and accurate measurements.
The composition of a cracked gas stream in an ethylene plant is determined by the plant design and feedstock.
Plants are characterised by the location of the De methanizer and acetylene converter. In front-end plants, the acetylene converter is located upstream of the De methanizer. And in back-end plants, the acetylene converter is located downstream of the De methanizer (Figure 4).
The location of the De methanizer determines the amount of light gases (methane, hydrogen, carbon monoxide) that will be present in the cracked gas stream entering the acetylene converter.
Endress+Hauser calibrates each TDLAS analyser built using a calibration gas mixture blended to simulate the process gas stream. To do so we require the background stream composition of the cracked gas, with typical, minimum, and maximum expect values for each component, especially H2O the measured component.
![]() |
Figure 4 … plant design and cracked gas stream composition in a back-end plant |