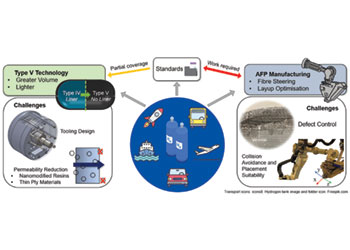
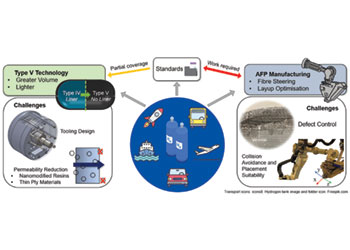
A critical review by researchers of Type IV vessels and Type V CPV technology could provide an avenue for a new generation of high-performance composite pressure vessels for storage of hydrogen, key to climate goals
Hydrogen has been identified as a suitable energy carrier for meeting the climate objectives as outlined by the Intergovernmental Panel on Climate Change (IPCC), which has set a limit of 1.5 deg C above pre-industrial levels to prevent global warming.
A key challenge to enabling the use of hydrogen is storing it with high volumetric and gravimetric density.
Although various methods for storing hydrogen—in solid, liquid and gas forms—are in use around the world, with each method having unique benefits for respective industries, the storage of hydrogen as a gas has emerged as the leading form of hydrogen storage globally.
The challenge here is that because hydrogen is the lightest element, it must be held at very high pressure (350–700 bar) to achieve practical densities.
A common method for storing hydrogen to meet these requirements is within carbon fibre composite pressure vessels (CPVs).
High-pressure gas storage vessels represent one of the largest and fastest-growing markets for advanced composites, particularly for filament-wound carbon fiber composites.
The high strength of carbon fibre allows for the construction of lightweight tanks with gravimetric storage densities of more than four times that of a steel vessel.
Researchers at the University of New South Wales in Australia, including Alexander Air, Md Shamsuddoha, and B Gangadhara Prusty, have reviewed existing work on Type IV and Type V pressure vessels including the challenges facing Type V vessels.
TYPES OF PRESSURE VESSELS
Pressure vessels commonly used in the industry today can be classified into five types:
• Type I vessels: These are the simplest to design and manufacture and make up most vessels in use today.
• Type II, III and IV vessels: These are known as composite overwrapped pressure vessels (COPVs) and commonly utilise carbon fibre to withstand part or all the structural load and a metal or plastic liner for gas containment.
Many ground transport applications use Type IV vessels, as they offer the lightest weight and highest storage densities.
Two well-known hydrogen fuel cell electric vehicles, the Toyota Mirai and Honda Clarity, both use Type IV vessels with an operating pressure of 700 bar.
The plastic liner in the Type IV, commonly HDPE or PA, is used to prevent gas leakage; and the ends of the vessel feature polar openings that are fitted with polar bosses.
The boss is used for filling and emptying the vessel and commonly includes access for sensors.
The boss on a Type I – III vessel is typically integrated with the liner, however in Type IV and V vessels it is a separate metal or composite component.
EVOLUTION OF TYPE V CPVs
Type IV vessels are the subject of intense research due to their current relevance to many industries.
However, the state-of-the-art in composite pressure vessel technology is linerless. Also known as Type V, these pressure vessels have long been a goal in designing carbon fibre composite high-pressure storage tanks.
A Type V vessel does not have an internal liner so the composite acts as both the gas barrier and load bearing structure. As the composite is not overwrapped on a liner, they can be referred to as CPVs.
No liner eliminates the need for strain compatibility between the liner and composite, leading to increased fatigue performance and the potential to achieve a 10–20 per cent weight reduction.
However, the possible operating pressures of Type V tanks are still not yet fully explored.
Traditionally, COPVs/CPVs are manufactured using filament winding (FW), a technique that winds tensioned bands of fibres around a rotating mandrel. Whilst this technique is capable and mature, it has several inherent limitations.
The design of COPVs/CPVs can be improved with the use of more advanced manufacturing methods, primarily automated fibre placement (AFP).
AFP is an evolution of the traditional filament winding technique and provides high accuracy and quality as well as low wastage.
Both Type V design and AFP technology have high potential for increasing the gravimetric and volumetric density of hydrogen gas storage. However, several engineering challenges must be overcome before they can be adopted commercially and offer a reliable alternative to Type IV tanks.
PAST RESEARCH
Type III and IV pressure vessels feature full composite overwraps and have been studied extensively as well as used commercially.
Work on Type V vessels began in the aerospace industry as early as the 1980s. A number of groups have developed Type V tanks for commercial applications or industrial research.
However, the existing peer-reviewed literature available for critical review is highly limited.
Researches in the past have produced numerous Type V test vessels in various sizes and evaluated their helium permeability and mechanical performance.
One design achieved a 15 per cent increase in storage volume and a 25 per cent reduction in mass compared with an equivalent Type I tank.
Another design achieved a pressure of 558.5 bar before helium leakage was detected and a burst pressure of 620.5 bar, which is close to the automotive industry standard operating pressure of 700 bar.
Some researchers also designed and manufactured full scale demonstrator tanks that were proof tested to 41.4 bar and pressure cycled 2,000 times at 27.6 bar.
Fuji Heavy Industry (renamed Subaru Corporation) manufactured two linerless pressure vessels with quasi-isotropic layup patterns.
The vessels were pressurised to 11 bar at liquid nitrogen temperature and helium leak tested.
Strain gauges and acoustic emission testing was used to evaluate damage to the vessels. No damage or leakage was detected at the cryogenic temperature or afterwards.
During investigation of burst pressure prediction in lined versus linerless tanks, accounting for stochastic effects present in the manufacturing process, researchers found that both the first ply failure and burst occurred at lower pressures for the linerless tank.
CONCLUSION
Hydrogen is emerging as a promising future energy medium in a wide range of industries. For mobile applications, it is commonly stored in a gaseous state within high-pressure COPVs.
Type V eliminates the internal polymer gas barrier used in Type IV vessels and instead relies on carbon fibre laminate to provide structural properties and prevent gas leakage.
Achieving this functionality at high pressure poses several engineering challenges that have thus far prohibited commercial application.
Additionally, the traditional manufacturing process for COPVs, filament winding, has several constraints that limit the design space.
Furthermore, AFP, a highly flexible, robotic composites manufacturing technique, has the potential to replace filament winding for composite pressure vessel manufacturing and provide pathways for further vessel optimisation.
And a combination of both AFP and Type V technology could provide an avenue for a new generation of high-performance composite pressure vessels.
By Abdulaziz Khattak