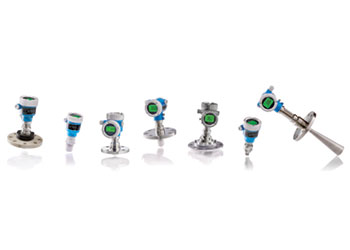
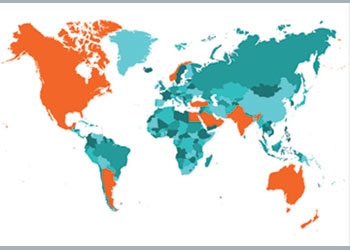
The mechanical thruster has been designed to be configurable and optimised to fit every environment on every drilling project across the globe, saving customers’ time and cost
Proprietary to TAQA, the mechanical thruster is a niche drilling tool engineered to enhance drilling performance by creating consistency in drilling parameters and reducing downhole dysfunction.
This proven technology has amassed over 9,500 runs downhole, resulting in many major operators including the tool as a standard bottom hole assembly (BHA) component.
"Over the years, the product has undergone several iterations as we believe continuous improvement is key to meeting and exceeding ever-changing market requirements," says a TAQA spokesman.
The product has been designed to be configurable and optimised to fit every environment to save customers’ time and cost on every drilling project across the globe; from the initial design of a single configuration, single acting tool to a dual acting configuration that can be tailored to just about any drilling condition from shale drilling and extended reach drilling (ERD) to deep geothermal applications in metamorphic rock.
How does a mechanical thruster work?
The tool balances counter acting forces to provide a consistent depth of cut while absorbing detrimental downhole vibrations.
This is not a simple task; the applications group require a variety of offset downhole data and BHA design to understand the customers wells and objectives.
The tool is then tailored internally to fit the specific operation and placed appropriately within the BHA.
Once the initial runs are completed, a thorough analysis is performed to validate KPI and overall tool performance. This system is called Plan, Execute, Learn and Refine.
At the beginning, TAQA works with end users to understand the operation at hand, analyse data for specific KPI’s and come to a mutual conclusion on what is expected from the application of the mechanical thruster (Plan).
At that time, TAQA moves into field deployment where its team works to monitor the operation and work with the on-ground teams to assure success and confirm its tools are functioning optimally across the customer’s wellbore (Execute).
The TAQA team then goes through a process to understand what went well, what may have not gone well and what could go better on the next iteration (Learn).
Since wells from one region to the other and even from one formation to the next can be very different, therefore, the final phase consists of tailoring the tools to better fit customer-specific application.
Work is done in coordination with the drilling engineering and directional drilling teams to optimise a tool that will be more and more effective every well until the point is reached where the tool is perfectly fit for customer application (Refine).
PRIMARY APPLICATIONS FOR THE MECHANICAL THRUSTER
The mechanical thruster will perform from simple surface hole sections, utilising packed assemblies, to difficult ERD wells with lateral lengths greater than 6,000 m.
In surface sections where effective weight is limited by available string weight, the tool will utilise the pump open force to keep a consistent depth of cut at the bit, effectively eliminating bit bounce scenarios.
In an extended reach well where weight transfer becomes inefficient and parameters from torque to differential pressure become erratic, the tool will utilise the balance of hydraulics and mechanics to keep the consistent depth of cut and effective weight to bit to eliminate dysfunction and provide more consistency in the noted drilling parameters.
In vertical/tangent sections where there are interbedded formations that require consistent alteration in surface parameters to meet the next formations’ requirements, the tool acts instantaneously to keep the bit fully engaged and eliminate the large shock events typically seen at these transition zones.
This results in reduced damages and DBRs, and allowing the driller to continue ahead without tripping out of hole for damaged bits and BHA components.