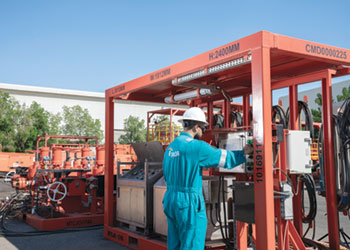
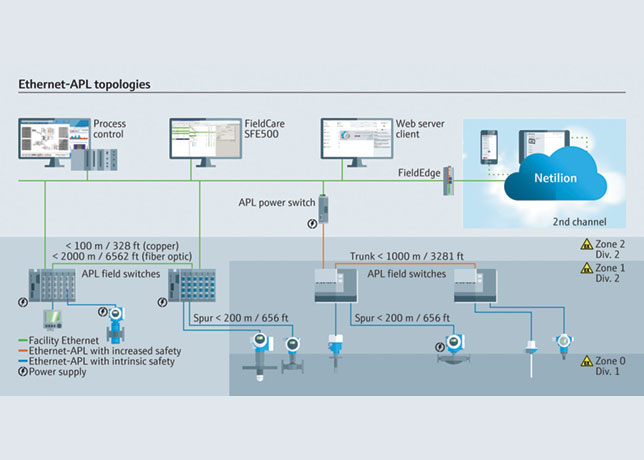
Smart instrumentation, simple connectivity, fast implementation, secure operation: With its compelling performance, Ethernet-APL is preparing for a triumphant march through process control plants, Jan Strohmeier and Karl Büttner tell OGN
Field level connectivity and data access are crucial to support trends like digitalisation and Industry 4.0 which uses valuable data from the field for optimisation of processes.
Even though this is already possible with established technologies, there are limitations such as low speed, limited bandwidth, and complexity by required protocol conversions. However, all this changes with ‘Ethernet with an Advanced Physical Layer’ Ethernet-APL.
Jan Strohmeier, Digitalisation Manager, Endress+Hauser, Middle East, and Karl Büttner, Product Manager - Platforms, tell OGN energy magazine what exactly Ethernet-APL is.
WHAT IS ETHERNET-APL? IS IT A PROTOCOL?
Ethernet APL is not a protocol; it is a physical layer to connect the field device. Through the Ethernet-APL switch, the field devices are directly connected into the operation technology (OT) Ethernet backbone.
The main purpose of the Ethernet-APL switch is to provide communication and power to the field device via a two-wire cable.
On the other hand, it takes on the already known RJ45 Ethernet connection or fibre optic connections to the plant Ethernet backbone.
The communication and data exchanges are based on protocols like PROFINET or Modbus TCP.
ADVANTAGES OF ETHERNET-APL
• Ethernet acts as a data highway and the content is sent in the form of packages between the source and destination. Because of this, limitation of proprietary protocols is removed.
• With this functionality the same connection can handle independent and different protocols simultaneously. This means the controller is receiving the measured value and the configuration software can access the device at the same time without any additional connection or second channel setup.
• With direct device connectivity from the controller to the field device the remote input/output (I/Os) are not required anymore.
• As there are no 4-20mA or pulse I/Os required to transfer the measured value, the currently used setup of input cards with the correct unit and scaling is obsolete. Not only are the setup and configurations reduced on both sides, but also, there are fewer sources of failures. Due to this, field loop checking, and simulation is not required anymore during the startup phase.
• Ethernet-APL is based on 2-WISE (2 Wire Intrinsically Safe Ethernet; according to IEC TS 60079-47) and thus enables, for the first time, to not only use Ethernet over a single wire-pair, but also in hazardous areas including Ex Zone 0 and 1 or Cl. I Div 1.
HOW FAST IS THE DATA COMMUNICATION?
Each field port at the switch will connect to one field device with a speed of 10 Megabits per second (Mbit/s) full duplex.
For the backbone network, connection up to 1 Gigabit per second (Gbit/s) per ports are available via RJ45 and fibre optic.
Two ports can be used to create a network ring to have redundancy in the backbone connection (Profinet: Media Redundancy Protocol, MRP).
ETHERNET APL DEFINING THE FUTURE OF INSTRUMENTATION
• Ethernet-APL removes the need for protocol conversions and gateways, providing barrier-free and parallel accessibility and providing the extra speed required in a data-driven economy.
• Plant efficiency is becoming an increasingly important topic in process automation. For this purpose, it must be ensured that a process plant operates reliably, provides information on future maintenance intervals for the instrumentation, is easy to diagnose in case of failures, and works with devices from different device manufacturers.
The basis for these aspects is the continuous collection and analysis of data from the installed base. Ethernet-APL supports all the requirements of a highly efficient process plant.
• This increased accessibility to each device may lead to new IIoT solutions.
WHO WAS INVOLVED IN CREATING THIS INNOVATIVE TECHNOLOGY?
![]() |
The Ethernet-APL organisation and key features |
Ethernet-APL with all specifications, guidelines and interoperability certification was developed in a global project setup.
This project was backed by leading industry standard development organisations like FieldComm Group, ODVA, OPC Foundation and PI (Profibus and Profinet International), as well as major industry suppliers of process automation to consider as many aspects as possible and to have a broad acceptance in the phase of implementation and roll-out.
The partners involved (in alphabetic order): ABB, Emerson, Endress+Hauser, Krohne, Pepperl+Fuchs, Phoenix Contact, Rockwell Automation, Samson, Siemens, Stahl, Vega, Yokogawa.
The project was finished in 2021 and went to the standards organisations for further maintenance and caretaking.
WHEN IS THE NEW TECHNOLOGY AVAILABLE?
The technology was launched in 2021 after 6 years of preparation and standardisation.
After the launch, the manufacturers applied the standards and developed the devices.
The first Ethernet devices and network switches were released into the market in mid-2023, and the portfolios of devices from different manufacturers are increasing month by month.
CHALLENGES OF FIELD INSTRUMENTATION TODAY AND HOW TO OVERCOME THEM
![]() |
The Ethernet-APL story in one picture |
Process plants today compete to produce more products with less waste, and thin profit margins require increased output yield with increasing quality.
Digital transformation has made it increasingly worthwhile for companies to consider making investments to obtain more plant data from process automation systems and instrumentation.
However, to do so, new procedures and products are required to gain access to this data from every part of the plant and to extract more value on every production run.
To do this, we need access to not only measured values but also additional data that the device produces, which, with the existing setup is not possible or restricted.
This access was extremely limited especially when we consider hazardous areas. However, with Ethernet APL, this data can be easily accessed from anywhere within the plant.
One of the options to retrieve this data is by actively connecting to the device with the configuration software.
This connection can be established either through a second channel or via the service interface at the device itself.
All the data generated in the device can give insights into the application in real time and with these insights smarter decisions can be made.
Besides, many process values can be used to improve production, for example, a Coriolis flow meter provides mass flow and density, temperature or viscosity information.
Additionally, monitoring values can be used to optimise processes, for example, information about the echo quality when doing radar level measurements.
Simple connectivity of Ethernet-APL devices can be considered as one of the key features allowing us to overcome the challenge of designing a network and the complications it comes with.
With most field protocols the network needs to be designed and when in EX areas an additional EX calculation needs to be carried out to ensure the safety of the plant.
![]() |
The Ethernet-APL 2-WISE EX concept |
Extension or modification during operation needs planning efforts to ensure safety. These challenges of designing and modifying existing networks were considered when Ethernet-APL was designed.
Field devices are connected with a single pair cable which is a point-to-point connection from the switch port to the device. This removes any challenge for the design and even when considering the cable length, the EX-calculation is completed (2-WISE).
For any 2-wire device available today in the market, the Ethernet-APL connection will also supply the power needed to power up the device.