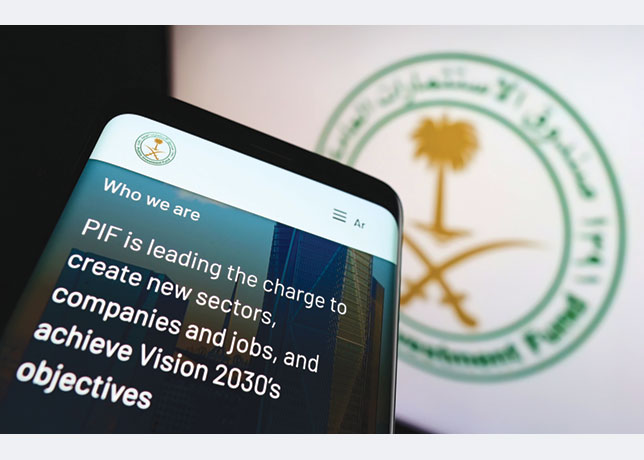
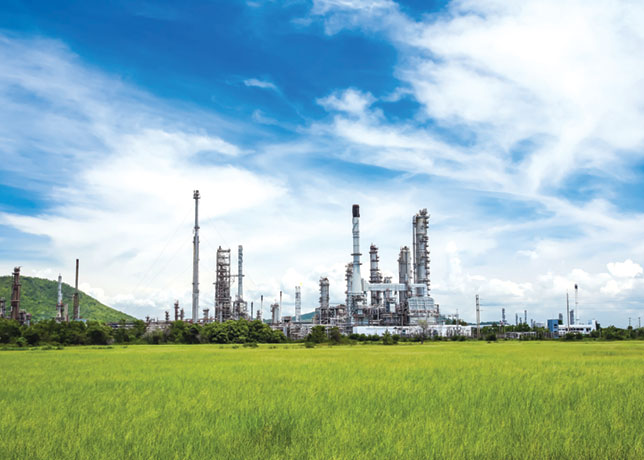
Embracing circularity in asset management processes fosters sustainability, reduces costs, and extends equipment lifespan, while AR streamlines servicing, minimising emissions, Mateusz Zajac, Sustainability Lead, ABB Electrification Service, tells OGN
Keeping costs low, reducing total cost of ownership and improving sustainability doesn’t need to be a trade-off, if circularity is front and centre of your asset management processes.
The circular economy is an economic concept that prioritises, amongst other factors, the lifetime extension, material reduction and reuse and recycling of products.
Contrary to the traditional linear model of ‘take-make-dispose’, in a circular economy, we keep resources in use as long as possible, extracting the maximum value from them, and then recovering and regenerating products and materials at the end of their useful life.
The efficacy of circularity is already well documented, with The World Economic Forum (WEF) estimating that the global material cost savings of adopting a more restorative economic structure could be over $1 trillion per year by 2025.
A large proportion of this saving would be a result of industrial supply chains reusing materials, eliminating waste and reducing resource dependency.
By extending the life of equipment in service, you can avoid emissions, replace capex investments with opex costs, and improve the sustainability of your operations.
![]() |
Retrofitting can help deliver significant cost savings compared to replacing |
There are several factors at play driving this change: Regulatory, economic and competitiveness.
For example, running equipment to the point of failure may cost up to 10 times more than investing in a program of regular maintenance.
Likewise, there are increasing opportunities and incentives for businesses to decarbonise, such as the Corporate Sustainability Reporting Directive (CSRD) from the EU and Inflation Reduction Act (IRA), providing incentives for clean energy in the US.
Using circular economics to avoid operational emissions with circularity is an increasingly popular way of doing business sustainably for those managing power distribution assets.
Thanks to advancements in technology and a more granular understanding of the role industries must play in circular economics, there is now a wealth of tools and techniques to make circularity easier to achieve.
REDUCING DOWNTIME KEEPS WASTE TO A MINIMUM AND PROFITS HIGH
To operate in an everchanging and volatile environment, oil and gas operators need to develop effective resilience strategies, with greater system flexibility, delivered through digital and emerging technology.
The downtime required to replace or upgrade an outdated component is significantly less than the time it takes to install an entirely new system or troubleshoot unknown issues.
By identifying the problem before it happens, predictive maintenance also enables engineers to accurately calculate how much downtime will be required to correct the issue.
Less downtime means less waste, especially in certain applications like the food and beverage sector, as well as time savings that equate to increased profit.
Let’s use switchgear as an example. Extending equipment life using component retrofits when needed results in 80 per cent less downtime (equivalent to one day, instead of one working week), around 40 per cent cost savings, and a remarkable 60 per cent carbon emission avoidance compared to a total switchgear replacement.
By leveraging new technologies and retrofitting dated components with digital upgrades, oil and gas providers can achieve improved resilience, as well as helping deliver performance improvements, investment optimisation and new levels of sustainable efficiency.
Industry 4.0 and IoT connectivity are key drivers for system upgrade programmes.
Subsequently, businesses are investing heavily in automation and digitalisation – cutting short the operational life of many systems that are no longer compatible with future business objectives.
For facilities working towards circular economics, choosing a system specialist that offers retrofits and upgrades of key components rather than the complete replacement of entire systems, can help strike the right balance.
Retrofitting or upgrading technology can not only help organisations to work towards a more circular economy but can also deliver significant cost savings compared to replacing entire systems.
By only upgrading parts of a system that deliver connectivity and advanced digital functionality, not only can much of the equipment remain in service, minimising costly downtime, but it also saves on natural resources – such as copper – and avoids carbon emissions as only the components require manufacturing, transportation and end-of- life disposal.
EXTENDING LIFECYCLE OF EQUIPMENT BY UP TO THREE DECADES
With this approach, ABB customers have reduced the cost of operating equipment by a third while extending the lifetime of electrical infrastructure by as much as 30 years.
In terms of best practice, early adopters are taking a preventative approach, replacing older, nondigital circuit breakers with more intelligent, digitally enabled breakers linked to cloud-computing platforms that enable the seamless provision of value-added services.
These can provide real-time data analysis on asset condition, performance and potential safety issues, helping operators prevent potential hazards before they arise and minimising disruptions to production.
AVOIDING EMISSIONS IN SERVICING WITH AUGMENTED REALITY
Using the latest augmented reality (AR) technologies, servicing equipment is now more efficient and more accurate than ever before, but without the emissions associated with servicing technicians visiting site – saving up to 171 gm of CO2 per passenger-kilometre.
Unlike virtual reality (VR), which replaces physical reality with a computer-generated environment, AR superimposes digital information on the physical world.
Augmented servicing removes the need for an engineer to travel to site, by providing them with a remote real-time view of the equipment via a smart device like an Android or iOS phone.
Information and servicing guides can be overlayed (augmented) into the view of the technician carrying out the service, to provide simple instructions and diagnostic guidance that can provide solutions in hours, not days.
https://electrification-ebooks.abb.com/story/throwaway_culture_oil_and_gas/