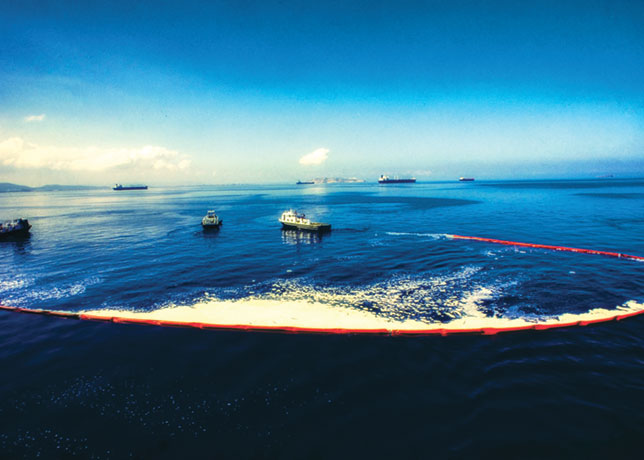
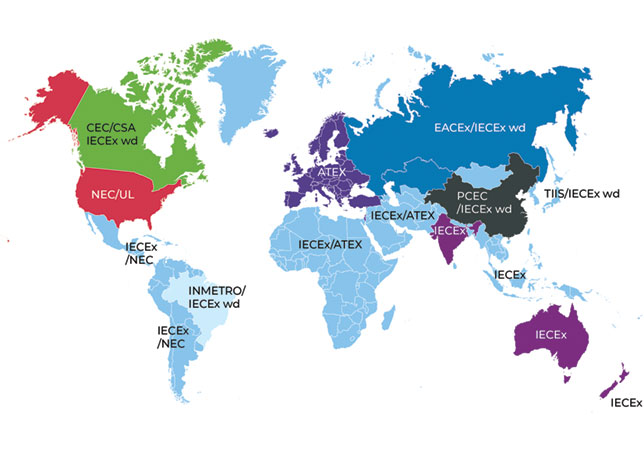
The Cygnus 1 Ex is the only gauge certified safe for Zone 0 and thus can be used within hazardous areas at any time without needing a hot work permit, David George, Technical Director at Cygnus Instruments, tells OGN
Several crucial aspects must be considered when operating in a potentially explosive atmosphere, including understanding the potential hazards and choosing the correct tools for the identified hazardous areas.
Globally, the term Ex is recognised for explosive atmospheres and the schemes used to prevent explosions.
Hazardous areas are locations with a risk of fire or explosion due to the presence of ignitable or flammable substances in the air.
These substances include gases, vapours, and dusts at concentrations high enough to produce an ignitable mixture.
Hazardous area can be classified into (Figure 1):
• Zones, the term used within the European ATEX scheme.
• Classes, Divisions and Groups, the terms used in the North American NEC/UL scheme.
![]() |
Figure 1 … hazardous areas can be classified as Zones or Divisions |
Plants and facilities will have many different Zones or Divisions. Once these hazardous areas have been established, signs must be installed to warn and inform anyone entering the area.
It is important to be aware that these area labels can change, especially as a result of a leak. For example, if a welded joint, flange, or valve leaks, the Zone around it can be elevated from Zone 1 to Zone 0.
EX SCHEMES & STANDARDS GLOBALLY
The International Electrotechnical Commission (IEC) provides an international standard for the classification of hazardous areas and Ex-equipment as well as a standardised labelling system.
The IEC standard is a UN-endorsed standard that provides a common point of reference for understanding the various Ex rating standards used worldwide.
The ‘IECEx system’ is the IEC system for certification to standards for equipment used in explosive atmospheres.
Most systems around the world are based on IECEx. Figure 2 shows the type of schemes and standards adhered to in each country.
Regions like the European ATEX Standard and the North American NEC/UL Standards use the IEC 60079 Standard as a source.
Cygnus 1 Ex gauge has been approved to IECEx, ATEX and UKEX requirements and is the ONLY gauge that meets the highest classification of ATEX Zone 0, equivalent to NEC (UL) Class I Division 1 Group 'ALL'.
In both the IECEx and ATEX Systems, hazardous areas are classified into Zones based on an assessment of the frequency of the occurrence and duration of an explosive atmosphere:
• Zone 0: An area in which an explosive gas atmosphere is continuously present or for long periods. Zone 0 is the most hazardous area.
• Zone 1: An area where an explosive gas atmosphere is likely to occur in normal operation.
• Zone 2: An area in which an explosive gas atmosphere is not likely to occur in normal operation and, if it occurs, will only exist for a short time.
In the North American NEC/UL Ex scheme, Divisions are used instead of Zones:
• Division 1 = Zones 0 and 1.
• Division 2 = Zone 2.
EX STANDARDS VERSUS OTHER TESTING METHODS
There are other methods for testing equipment in hazardous areas, but it is important to be aware of how they differ from Ex standards.
The MIL-STD-810G only tests a piece of equipment to see if it can cause an explosion on the day of the test. It does not consider use in the field, being dropped, becoming faulty, or short-circuiting batteries. This means it provides no guarantee that the equipment cannot cause an explosion.
The Ex standard, on the other hand, provides assurance that the equipment, even if faulty, cannot cause an exposition.
Ex equipment must be designed to be safe. Redundant safety circuits are incorporated into the design so that if one fails, the next will still provide protection.
Equipment is drop tested, IP tested, and batteries are short-circuited to check they don’t explode or get hot. Materials used must be anti-static to avoid static charge buildup that can cause sparks.
INTRINSICALLY SAFE VERSUS EXPLOSION-PROOF
![]() |
The Cygnus 1 EX ... certified safe for Zone 0 Credit: Mirko Torrez Contreras (2021) |
‘Intrinsically safe’ is one of the protection concepts used to define Ex equipment designed for safe operation in hazardous locations.
The Cygnus 1 Ex gauge uses intrinsic safety protection to limit the energy present in its system, meaning it is insufficient to ignite a hazardous atmosphere under any conditions.
This includes low power levels and low stored energy. Intrinsically safe equipment can be Ex-certified to Zones 0, 1 or 2.
Another concept often used is explosion-proof (or flame-proof). This type of equipment is sealed and rugged, such that it will not ignite a hazardous atmosphere.
However, it is possible for a spark or explosion to be generated within the equipment itself. For this reason, explosion-proof equipment can only be Ex certified to Zones 1 or 2.
This means that only Intrinsically safe equipment can be used in Zone 0.
What you need to know about Equipment Protection Levels (EPLs)
All certified Ex equipment (portable or fixed) designed for operation in hazardous areas, will have an Ex Certificate of Conformity (C-of-C) that states its Equipment Protection Level (EPL), represented by a ‘G’ code.
Table 3 below shows the correlation between Zones, EPLs and different protection concepts. Cygnus uses the Intrinsically Safe protection type for its Ex products.
HOT WORK PERMITS
Hot work permits are used to mitigate the risks of hot work tools or processes capable of creating a spark or generating enough heat to ignite a gas.
Thanks to its intrinsic safety design, the Cygnus 1 Ex gauge does not generate sufficient energy to cause an explosion and, therefore, can be used safely within hazardous areas at any time without needing a hot work permit.
This saves a lot of hassle, as obtaining a Hot Work Permit is normally costly and time-consuming. A formal application with a risk assessment and methods to remove or reduce the risks is required.
Typically, for a permit in a hazardous area:
• The permit must be authorised by a senior person.
• A competent person is required to check gas levels.
• Oxygen levels and flammable substances must be frequently monitored.
• Persons should be competent in emergency response and first aid.
• Specialist rescue equipment on standby is required.
• Pipes and tanks may need to be purged with nitrogen.
• Plant operations should be shut down.
Hot work permits can be very inconvenient and must be planned. It would be far easier to use Ex equipment.
The Cygnus 1 Ex is the world’s only Zone-0 UTM gauge certified to ATEX, IECEx, and UKEX for use in all hazardous Zones 0, 1 and 2.
Featuring three measuring modes and the deep coat function, this versatile UTM gauge can measure the wall thickness of various materials through thick coatings or extreme corrosion.
The A-Scan and B-Scan functions provide additional measurement verification and cross-sectional display, whilst the data logging capability records measurements with A-Scans for hassle-free reporting and analysis.
Furthermore, the manual measurement mode allows manual gates and gain to be configured to suit your application.
When coupled with Cygnus’ high-temperature Ex probe, the gauge transforms into a high-temperature thickness gauging kit for efficient corrosion inspection on hot assets in service without needing a plant shutdown or hot work permit.
Despite various advanced functionalities, the Cygnus 1 Ex gauge is surprisingly easy to operate, thanks to four measurement screens, four function keys for easy controls and dynamic views, and an intuitive menu.
Like all Cygnus products, the Cygnus 1 Ex thickness gauge is manufactured in the UK and has a three-year warranty.