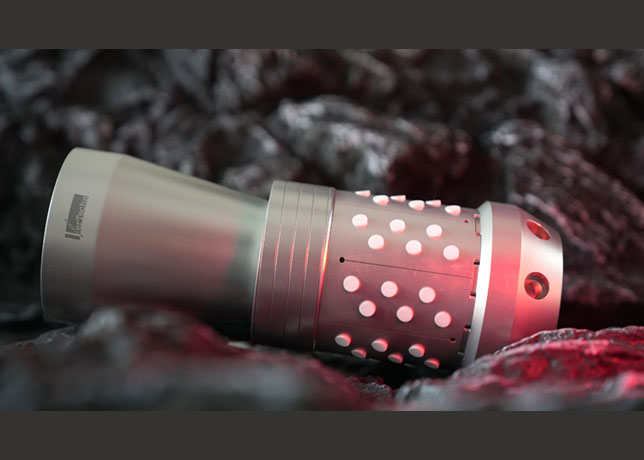
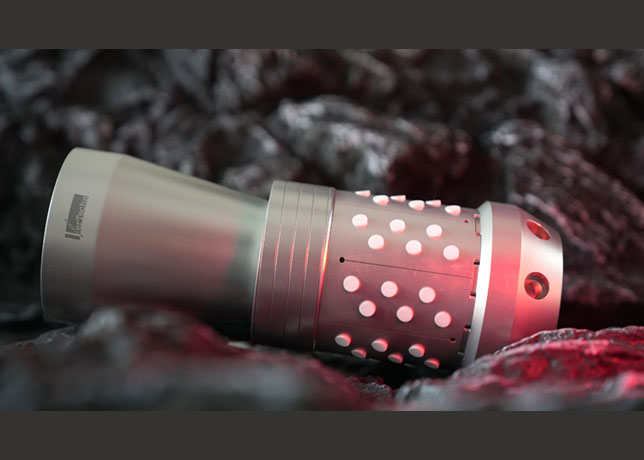
Dissolvable frac plugs boast a smaller outer diameter (OD) and specialised isolation and anchoring mechanisms, designed for the complexities of irregular casings. The slimmer OD of these plugs facilitates passage through common restriction sizes typically encountered in 4.5” and 5.5" deformed casings, says Jinlu Wang – Product R&D, Technical Marketing, Vertechs Group
The dynamic process of running frac plugs into wells presents a unique set of challenges. While the objective is to ensure efficient stage isolation and maximise production, the irregular shape of oval casings introduces complexities.
This invisible uncertainty creates an obstacle associated with plug and perf operation and hydraulic fracturing. Exploring and understanding how such conditions can impact isolation, lead to plug failure, casing erosion, and ultimately result in lost production or extended operation time is important for every completion.
Casing deformations are not uncommon. It can occur due to various factors, including geological shifts, uneven wellbore trajectories, dramatic temperature changes, poor cement bond, and more. Based on extensive field data and case studies, successful pump down and achieving a proper fit for frac plugs becomes increasingly difficult in these challenging wells, jeopardising the integrity of stage isolation during hydraulic fracturing process.
![]() |
Jinlu Wang |
Frac plugs are designed to withstand high-pressure environments and maintain isolation integrity during hydraulic fracturing. However, when deployed in deformed casings, the risk of pump down and plug failure escalates significantly.
One of the primary concerns faced by operators is the occurrence of frac plug getting stuck in the wellbore during RIH. When encountering downhole restrictions, the plug and perf Bottom Hole Assembly (BHA) risk becoming completely stuck, halting the pump down process and rendering wireline retrieval ineffective. This issue is prevalent in certain unconventional development areas, leading to costly delays and necessitating remedial measures. Typically, the standard approach involves setting the plug in place and coordinating coiled tubing for plug drill out. However, situations may require breaking wireline, resulting to fishing operations. The coiled tubing operations often spans 3 to 4 days, sometimes extending over weeks in severe cases.
To keep in mind, once the fishing operation is completed, the presence of downhole restrictions still persists and casing deformation has the potential to deteriorate further as fracking operations progress. Therefore, another and many more plug and perf run failures may reoccur in the future.
![]() |
3.85” dissolvable frac plug for 5.5” casing greatly reduces the risk of running issues |
Under such circumstances, smaller frac plugs are necessary to pass through the restriction and be set within the casing. Given the imperfections in downhole conditions, it's probable that the frac plug will be deployed and set within the oval section of the casing. The oval shape of the casing presents challenges for the proper engagement and setting of the frac plug.
The misalignment between the plug slips and the casing wall exacerbates stress concentration points, making the plugs susceptible to mechanical failure, and creating unwanted gaps, promoting elastomer extrusion and consequent leakage.
The irregularities inherent in oval casings compromise the ability to create a reliable seal with frac plugs. Inadequate sealing allows fluid migration between wellbore zones, undermining the efficacy of hydraulic fracturing operations. This not only diminishes production efficiency but also increases the risk of plug failure and casing erosion.
For instance, even a mere 1mm clearance at the seal elastomer holds the potential for failure. Despite the negligible impact visible on charts during frac, this minor leak can gradually erode the plug, particularly in the presence of proppant. Over time, this erosion can intensify the leakage, leading to casing erosion and the loss of fluid to the stage below. Consequently, less fluid is effectively diverted into the current stage, compromising the effectiveness of hydraulic fracturing.
The repercussions of frac plugs failure in oval casings extend beyond immediate operational setbacks. The failure to achieve adequate isolation results not only in casing erosion and damage, it also decreased potential production rates, directly impacting profitability. Moreover, addressing plug failures and casing erosion necessitates costly remediation efforts, leading to extended operation times and further additional costs.
While the challenge of casing deformation and ovality remains beyond direct resolution, the industry continuously strives to improve dissolvable plugs for optimal performance in demanding well conditions. Specifically engineered to address such challenges, some dissolvable frac plugs boast a smaller outer diameter (OD) and specialised isolation and anchoring mechanisms, designed for the complexities of irregular casings.
The slimmer OD of these dissolvable plugs facilitates passage through common restriction sizes typically encountered in 4.5" and 5.5" deformed casings. This capability effectively reduces the likelihood of BHA entrapment in tight spots, minimising the need for over-pull, break wireline, or fishing operations.
Moreover, these dissolvable plugs feature specialised isolation and anchoring mechanisms, designed to expand the contact area of the sealing and slips. This ensures a better fit in oval conditions, comparing to tradition designs, thereby enhancing mechanical stress handling and isolation, ultimately optimizing plug performance in challenging wellbore environments.
Another challenge faced by the operators is to drill out frac plugs in deformed casing. Due to restrictions, the size of the bits may not be suitable for the frac plugs requiring drilling. Circulating cuttings and aiding the process with short trips can also prove challenging in deformed casings. This inevitably prolongs the drill-out time and increases the risk of the coiled tubing getting stuck, particularly during short trips where such incidents predominantly occur. Traditionally, short trips are conducted after drilling out every 5 or more plugs, this practice varies among service providers and regions. According to field data, a short trip can span from 4 to 8 hours, dominating a significant portion of the drill-out/clean-out phase. By running dissolvable frac plugs, these time-consuming short trips become redundant, potentially saving up to 50-60% of coiled tubing time.
To address the above challenge, dissolvable plugs offer the advantage of reducing coiled tubing drill out time, as the debris from their dissolution can be effortlessly flowed back without necessitating short trips. In an optimal scenario, dissolvable frac plugs vanish entirely before coiled tubing initiates the drill out process. However, even if complete dissolution doesn't occur downhole, it's not a catastrophic outcome. Drilling out of a dissolvable plug weighing approximately 3kg (less than 7lbs), only a minimal 5-8% (0.3-0.5 lbs) of residual material, often mixed with sand, returns to the surface. This indicates that 92-95% of the plug dissolved downhole.
In conclusion, the development and adoption of specialised dissolvable frac plugs offer a promising solution to mitigate challenges associated with casing deformation and ovality. By enhancing mechanical performance, reducing operational time, and minimising the risks, these field proven innovative solutions pave the way for more efficient and cost-effective completion operations.
By Abdulaziz Khattak