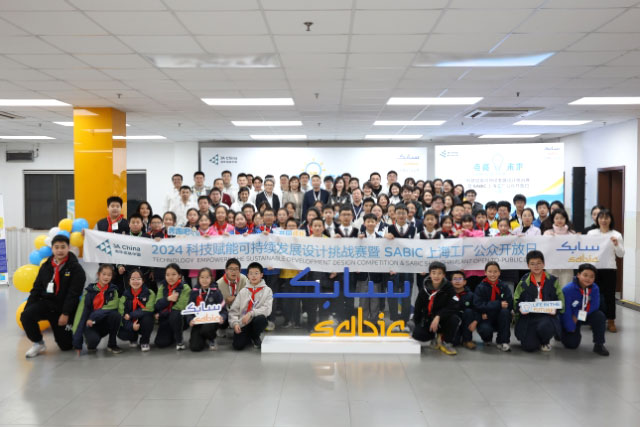
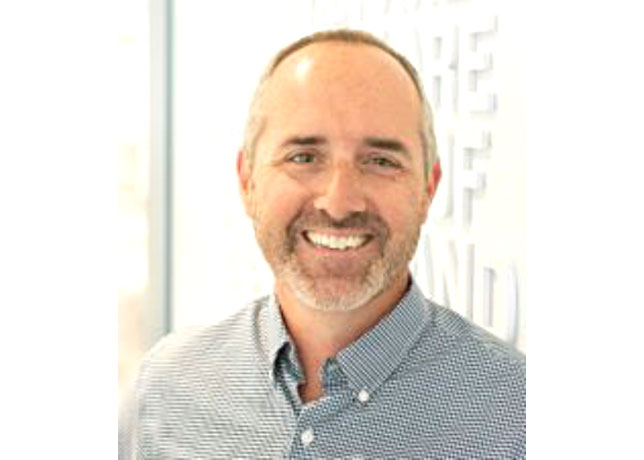
Effective plant turnarounds rely on early planning, supplier engagement, training, prefabrication, and quality control to ensure efficiency, reduce costs, and enhance long-term system reliability, Mike Aughenbaugh tells OGN
Plant turnaround is a major undertaking for chemical plants and refineries around the world. These complex events often involve hundreds of technicians from multiple vendors, working simultaneously to complete a variety of important maintenance, revamp, and renewal activities across a specific system or an entire plant at once, Mike Aughenbaugh, Associate Target Market Manager, Swagelok, tells OGN energy magazine.
Since a turnaround involves taking processes offline, thereby stopping production, it is in the owner/operators’ best interest to complete these projects as efficiently as possible.
Additionally, protracted turnaround projects involve keeping contractors on-site for longer, thereby increasing cost and risk.
For larger facilities, turnarounds may involve years of planning, and they represent massive investment on the operator’s behalf it is not uncommon that turnaround accounts for a major portion of the organisation’s annual maintenance budget.
For these reasons, a mismanaged turnaround can cause a major financial hit to an organisation.
![]() |
Figure 1 ... Switching to pre-engineered and preassembled grab sampling panels can reduce the potential for poor |
With all of this in mind, there are seven best practices that owners/operators can follow for more effective turnaround management:
1. Engage early with trusted suppliers: Planning for turnarounds is an extensive process, often beginning years before the work itself starts, and for good reason. Being as prepared as possible can help eliminate unforeseen project pitfalls.
Major fluid systems are complex entities, some requiring specialised parts and components made from highly specific alloys, depending on the process.
Lead times on obtaining these engineered-to-order parts are typically longer than stock stainless steel components, but early engagement with your supplier can help map out these needs well in advance.
2. Identify areas of new opportunity: While the goal of turnarounds is to restore all parts of the system to optimal working condition, turnarounds are also great opportunities to make additional system improvements that can result in higher reliability and performance.
Making these improvements requires advanced planning. System changes typically must be approved well ahead of the turnaround event itself due to management of change (MOC) requirements, and prior to the project’s engineering freeze.
Operators who have already engaged with vendors early are ahead of the curve here, and they can further work with these specialists for expert recommendations on system enhancement.
![]() |
Figure 2 ... Select vendors who offer localised support so they can deliver components in a timely fashion to prevent |
One example of system enhancement includes pre-engineered and assembled grab sampling panels, which can replace traditional grab sampling elements in a system.
This is a practical improvement that does not change the system’s fundamental design, and helps operators more easily draw proper samples (Figure 1).
3. Be prepared for the unexpected: Making allowance for variables and contingencies throughout turnaround is another way operators can ensure overall project efficiency.
For example, because of the large and complex nature of the fluid systems throughout chemical plants and refineries, it is practically impossible to know exactly which, and how many, specific components will be needed throughout the turnaround.
For that reason, it is beneficial to stock a variety of hoses, valves, and adapters prior to the start of the project.
Having some of these basic components already on hand can be a significant time saver versus having to order additional parts once installation is already underway.
4. Ensure the availability of local support: Sometimes, though, the unexpected does happen, and you may not have the right parts on hand at the time when you need them.
When coordinating with your vendors, ensure they can offer localised support near your project for any unforeseen parts sourcing that may occur to ensure timely delivery (Figure 2).
5. Keep a close eye on installation of critical parts: The number of technicians working on a given turnaround project can be staggering, involving hundreds of labourers from different firms and disciplines, oftentimes from around the world.
As such, the level of installation knowledge across these numerous vendors is often inconsistent.
Inconsistency is the last thing an owner wants on a turnaround project. For example, poorly routed tubes on existing fluid systems might be at risk of vibration fatigue, and an inexperienced technician might simply replace system components using the exact same routing and clamping points.
A more experienced technician might be able to optimise routing to eliminate vibration risk.
Additionally, a more inexperienced technician may not give proper consideration to tooling and equipment used to perform installation work, which can potentially damage components and lead to poor performance later on.
How do you ensure consistent installation, using the right tools, across dozens of different contractors?
![]() |
Figure 3 ... Changing seal support systems to standardised panels can make installation, service, and maintenance |
One strategy is to include training and certification within your specification. This ensures that anyone performing work on your system is equipped with certain baseline knowledge and is familiar with sound installation best practices.
6. Seek out prefabricated assemblies: Because of the engineering complexity of many fluid systems in chemical plants and refineries, the more that can be prefabricated, pre-assembled, and pretested prior to the turnaround, the more efficiently contractors can install these critical systems.
Prefabricated assemblies can once again help alleviate expertise and knowledge consistency concerns across numerous vendors and contractors, and can free up labour hours.
Grab sampling panels are one good area of opportunity, allowing for safe, efficient sample capture while meeting your specific plant application needs.
Elsewhere, mechanical seal support systems can help increase mechanical seal longevity. Analytical subsystems, including fast loops, field stations, calibration and switching modules, sample probes, and fluid distribution headers, can bring efficiency and consistency to your operations, with simplified design footprints (Figure 3).
7. Maintain tight quality control: It is in an operator’s best interest to maintain strict control of the quality and consistency of parts being installed during a turnaround.
Specifications that allow too much flexibility may lead some contractors to source less expensive and lower-quality components.
Inconsistent parts quality across different systems can lead to inconsistent performance, premature maintenance needs, or downtime later on.
Keeping a tight, up-to-date specification that allows only for the use of high-quality components in your critical fluid systems is one more way to make your turnaround effective.
In addition, the more consistent an operator is with not intermixing parts from different suppliers and not interchanging for different parts, the easier it will be to maintain systems consistently in the future.
Keeping these tips in mind, any chemical plant or refinery operator can see their way through faster, more efficient turnarounds while potentially improving long-term reliability and performance of fluid systems.
Interested in learning more about effective plant turnarounds? Swagelok can help; our local field engineering team regularly helps chemical processing or refining customers with effective plant turnarounds.
By Abdulaziz Khattak