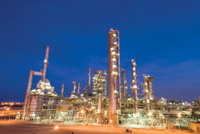
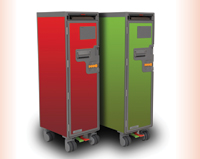
SABIC is helping its customers in the rail and aviation segments of the mass transportation industry address the growing demand for high performance, lightweight components, driven in large part by regulatory and fuel efficiency demands.
Sabic’s multi-faceted solutions, touch multiple parts of the industry, from an award winning in-flight trolley to parts made through additive manufacturing for hidden spaces – all of which comply with the various global, regional and OEM safety norms and greenhouse gas (GHG) emissions standards, such as Federal Aviation Administration’s (FAA) flame-smoke-toxicity (FST) safety regulations for aircraft, and European standards for fire safety in railway interiors.
These innovative materials help customers in the mass transportation industry bring their designs to life, reduce weight and improve safety, while also reducing emissions and improving fuel efficiency, enabling its customers to solve key challenges across mass transportation industries worldwide.
“Our materials help our customers comply with industry standards and fire safety regulations while also enhancing the aesthetics and comfort of the train or aircraft cabin environment,” Kim Choate, director of Marketing for Mass Transportation, Sabic’s Innovative Plastics business, says.
“Compared to traditional materials used in air and rail interiors, Sabic material solutions can significantly lower system costs through consolidation of parts to streamline production, as well as lowering shipping and fuel consumption costs by reducing weight. The ability to custom colour select materials also avoids the need for secondary operations such as painting.”
The challenge of carbon emissions reduction has been compounded by ever-increasing fuel prices, which account for more than a quarter of the operating costs in the aircraft industry, according to the Air Transport Action Group.
Delivering opportunities for aircraft OEMs to meet the critical challenges of weight-out, regulatory compliance, sustainability and improved flying experience, Sabic has expanded its Lexan XHR film and sheet portfolio with velvety texture aesthetic and co-extruded opaque sheet grades, as well as multilayer lamination film grades for aircraft interior applications.
The Lexan XHR sheet portfolio, which includes Sabic’s new super low gloss Lexan XHR6005 and Lexan XHR5000 (co-extruded) sheets, delivers superior weight-out of up to 12 per cent vs. traditional PVC/PMMA products, delivering improved fuel economy while fully complying with the Ohio State University (OSU) 65/65 standard and OEM’s material specification for aircraft parts and FST requirements (FAR 25.853) of major airlines for seating, cockpit linings, window surrounds and shades, door shrouds, and other interior components. It can also be colour-matched in sheet and resin form for co-ordinated thermoformed and injection-moulded parts.
In addition, the new Lexan XHR A13 film adds robustness in multilayer laminate constructions, used in decorative interior applications, increasing overall design functionality and reducing weight compared to traditionally used materials.
Sabic has helped its customers LSG Sky Chefs and Norduyn reduce weight by supporting the development of award-winning in-flight trolleys, certified as the lightest in the world. They incorporate UV-resistant Ultem resin for the extrusion profiles and door latch, while also incorporating ultra-tough Noryl resin.