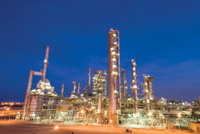
THE packaging industry is evolving to meet consumer lifestyle changes like growing demand for convenience food and an increased awareness about their health. Sabic is helping its customers in packaging respond to these needs and the continually evolving regulations that accompany them.
At K 2013 Sabic showcased the latest advances in both flexible and rigid packaging such as Sabic LDPE nExCoat 5 for extrusion coating and its new multi modal high density polyethylene (HDPE) portfolio for blow moulded packaging applications.
Along with enabling its customers to meet the ever changing consumer demands, these material applications also enable Sabic customers in industries like food and beverage to stay ahead of advancing regulations for safety.
This is especially true in Europe where Sabic is one of the first companies to comply with a key EU regulation around packaging safety, more than three years before it goes into effect.
Along with these important benefits for end consumers, Sabic’s packaging materials are also optimised to help processors reduce their material and energy usage.
“Sabic has developed a relevant set of products, that help its customers deliver convenient, safe and sustainable packaging solutions that meet the demands of the modern packaging industry,” says Mark Vester, business director LD/LLDPE, Sabic.
“The portfolio of packaging solutions, on display at this year’s K Show, are making significant contributions in enabling processors to improve the performance of their products, often while achieving savings in materials usage and energy consumption.”
Sabic has been working with its customers in the packaging industry to help reduce the environmental footprint of plastic packaging. According to Plastics Europe, the average plastic packaging weight over the past 10 years has been reduced by 28 per cent without sacrificing the performance and durability of the product.
As manufacturers continue to focus on reducing packaging weight, and the consequent carbon footprint of plastic packaging, Sabic is supporting them by developing new plastics like Sabic LDPE nExCoat5 which has up to a 20 per cent lower carbon footprint in comparison to standard market grades.
This advanced resin is produced by Sabic’s CTR tubular process with additional proprietary technology. Along with supporting the footprint reduction objectives of customers it also helps them save money by delivering a one-grade solution, creating opportunities for them to reduce their inventory and transportation costs.
Consumers want to know that the products they are buying meet the highest safety standards available. For the food and drink industries, this is of even greater importance. Packaging materials can affect the smell and taste of food and this has led to tougher regulations. In Europe for example, the Plastics Regulation (EU) 10/2011 (PIM) has been developed to further increase the safety of packaged foods.
Among the requirements, producers of plastics must include more stringent testing on products that are used in food packaging. Sabic is one of the first producers to have its food contact declarations updated in line with these changes, three years ahead of the required 2016 deadline.
Sabic’s product development team puts a strong focus on creating safe packaging solutions for customers. The company’s new blow moulding grade for the production of milk and juice bottles, Sabic HDPE B5260ULS, features good organoleptic properties, which are important when using in-bottle sterilisation, where the packaging, as well as the product, is subjected to tough thermal and mechanical conditions.
Additionally, the new grade has high stiffness, impact resistance and environmental stress crack resistance (ESCR), which helps to prevent breakage and potential contamination.
Superior ESCR is also one of the primary qualities of Sabic’s new multimodal HDPE portfolio, developed for household, industrial and chemical (HIC) packaging applications.
The resistance achieved for this new range, which includes Sabic Vestolen A BI5822 and Sabic Vestolen A BI5828, is more than double the ESCR recorded by comparable materials, making it ideal for aggressive chemical products.
Moreover, this range opens up the possibility to enhance the efficiency of the production process, offering Sabic customers a high performing, stiff, lightweight and robust material that meets the demands of the packaging industry for safe, durable and sustainable packaging solutions.
Sabic also announced the launch of an additional new range of multimodal grades which can be used in applications varying from small bottles to standard and UN approved jerry cans and 220 litre drums (tight and open head).
The new grades have excellent low die swell characteristics that meet the packaging industry’s most stringent demands, for example the (UN) packaging of dangerous goods requirements.