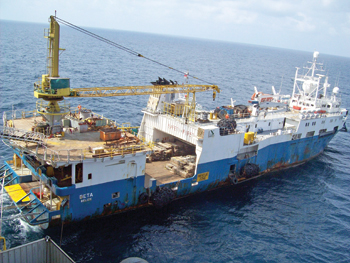
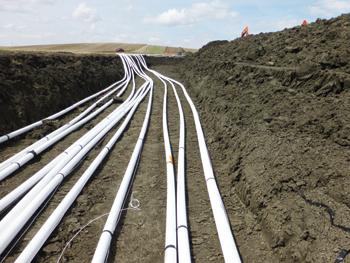
FLEXPIPE Systems, a division of ShawCor Ltd, is the market leader in providing reliable, corrosion-resistant, composite pipeline solutions to the energy sector. Over 23,000 km and 110,000 fittings have been installed successfully throughout North America, Latin America, the Middle East and Australia by the company so far, says Rajan Luthra, vice president, marketing - Flexpipe Systems.
“Our four product lines, FlexPipe Linepipe, FlexPipe Linepipe High Temperature, FlexCord Linepipe and FlexCord Linepipe Anti-buoyant, are based on a three-layer design (thermoplastic liner, a helically wound reinforcement layer and an external thermoplastic jacket). They are used for a wide variety of applications including flow lines, gathering lines and injection lines, and with most service fluids, including sweet and sour oil, water, methane and CO2,” Luthra explains.
Over the last 10 to 15 years, the oil and gas industry has widely accepted the use of reinforced thermoplastic pipe (RTP) as an alternate to steel pipe. RTP is gaining popularity because it provides a 30 to 40 per cent cost savings over traditional pipe. It comes in continuous lengths and therefore can be installed faster than steel pipe, which results in lower material, installation and operating costs.
In addition, the HDPE barrier layer and outer jacket provide resistance to internal and external corrosion. Operators who switch to RTP from steel become strong advocates for this technology as they realise the benefits of using composites.
For a two km pipeline, traditional steel pipe would need 164 welded and tested joints. RTP would only need two to four connections depending on the pipe size, pressure and temperature class. This results in reduced installation costs, faster installation and improved safety for field personnel. And, fewer connections mean less chance of leaking joints.
RTP is used for both surface and buried applications. It is typically used onshore, but operators are now using RTP for shallow water applications where water depths range from 50 to 100 ft. If used as a surface line another benefit of RTP is the potential to re-spool the pipe for re-deployment at another site like zero flaring temporary flowback lines in the Middle East, Luthra says.
Joint integrity is critical for any pipeline system. RTP manufacturers offer different kinds of connection systems, but hydraulically crimped or swaged connections have had the greatest success. Crimping/swaging technology not only helps minimise human error; it also provides extremely reliable fitting connections, he adds.
Due to the limitation of the amount of pipe that can be spooled onto a reel, RTP is typically available in 2-inch to 8-inch pipe diameters. “With advancing technology, companies are working to expand the application envelope of their product lines to service higher pressure and higher temperature applications. The qualification of spoolable linepipe can be done in accordance with Canadian Standard CSA Z662 and API RP 15S (Qualification of Spoolable Reinforced Plastic Line Pipe). A new revision of API 15S is expected to be released in 2015,” Luthra reveals.
The outlook for RTP is promising. While the environmental footprint of RTP is smaller due to trenching, the global footprint of RTP is growing. Flexpipe Systems is the answer to your next pipeline project, he adds