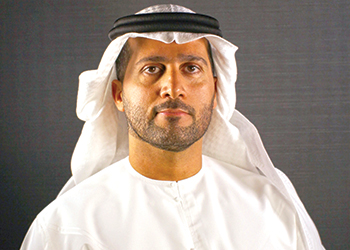
An international leader in filtration and separation, Porvair Filtration Group, is manufacturing key assemblies for the world’s first gas-to-liquid (GTL) refinery in South Africa, further enhancing its highly efficient operation.
PetroSA, South Africa’s national oil company, situated in Mossel Bay, is the world’s third largest GTL facility and produces some of the cleanest fuels on the market by using leading environment-friendly processes.
UK-based Porvair was engaged to supply highly efficient and durable sintered metal powder Triple Element Filters (TEFs) to PetroSA through its Johannesburg-based agents, Sagisa Process Engineering (Pty) Ltd.
Porvair’s scope of supply included innovative 2.4 metre-long TEF assemblies, manufactured in the UK as well as sintered metal mesh fuse assemblies manufactured in tandem at the filtration specialist’s US factory in Ashland, Virginia.
The TEFs and mesh fuses were fitted into tubesheets and installed into five vessels, manufactured and supplied locally by Sagisa.
The complete vessels were then shipped to the PetroSA refinery and are now helping to clean up catalyst fines – very small particles used in the Fluid Catalytic Cracking process (FCC) of most large, modern oil refineries and in the hydrogen process stream at Mossel Bay.
The assemblies were selected by PetroSA for their ability to operate reliably at temperatures in excess of 400 deg C and at a pressure of around 25 bar.
The vessels are located above the Catalyst Reduction Reactor (CRR), enabling the TEF assemblies to be cleanable in situ; therefore operating in a cyclic back flush operation to remove the catalyst cake from the filter surface of the TEFs. The disengaged catalyst then falls into the CRR.As a consequence, the TEFs are able to operate for a prolonged period in an aggressive environment, only periodically requiring to be removed and chemically cleaned before then being re-installed and operating once more at the same high performance level.