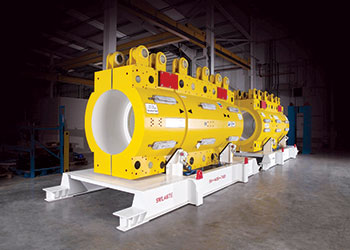
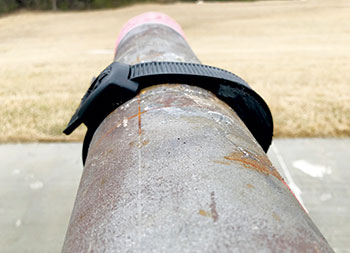
Clock Spring Company, for whom Saudi-based Safari Oil & Gas is the region’s installation and distribution partner, discusses the Clock Spring Leak Stopper
Leaking lines can cause environmental damage, threaten worker safety and impact productivity. Being able to quickly address unexpected leaks is vital to operations because failing to manage unplanned discharges wreaks havoc with worker safety, raises red flags for regulatory bodies and negatively affects the bottom line, says Andrew Patrick, executive vice president, Strategic Opportunities, Clock Spring Company.
Finding practical ways to control leaks and restore line integrity has the potential to improve worker safety, reduce environmental impact, and increase profitability.
CONTENDING WITH DAMAGE
Line damage is one of the most frequent causes of unplanned discharge. Quickly containing a leak is critical, but many of the tools traditionally used to stop a leak are only moderately effective, observes Patrick.
And stopping the leak is only the first step in managing operations. The next step is to restore the leaking line to safety to limit the disruption, eliminate the safety risk, and re-establish production. With many of the bolt-on devices available, it is possible to arrest a leak, but it is impossible to restore the line and continue operations without undertaking a major repair. Today’s owners want something better than a stopgap fix, he notes.
MITIGATING LOSS
Sometimes, the best solution comes not from a new technology but a new perspective. By combining a proven solution with specialised composite materials, it is possible to stop a leak and effect a long-lasting and dependable repair.
The Clock Spring Leak Stopper is a proven solution for arresting leaks for a broad range of chemicals and offers a way to create a long-term repair, he says.
STOPPING LEAKS FAST
The Leak Stopper is designed with a plug to quickly cover a hole in the pipeline and an optimized strap to secure plug placement. A trained technician can perform an installation in a matter of minutes using a specialized band to secure a gauged clamping device on the leaking line.
The installer places the band on the pipe, moves the stopper to cover the leak, and uses a rachet to tighten the band until no more pressure can be applied and the leak has stopped. Using the back of the tightening tool to trim the excess slack from the band, the technician can stop the leak with a repair that produces a finished profile that is only 25.4 mm (1 inch) thick. The streamlined approach simplifies the repair and creates a finished surface that can be overwrapped with a composite to safely extend the life of the repair, Patrick explains.
Everything necessary to make the repair is provided in a repair kit, including instructions for installing a composite overwrap.
TESTING AND VALIDATION
The tool was tested under multiple scenarios, proving its efficacy in arresting leaks on a 4-inch (101.6-mm) pipe with a 0.25-inch (6.35-mm) diameter hole and a 6-inch (152.4-mm) pipe with a 0.44-inch (11.2-mm) hole at an initial test started of 100 psi (6.89 bar), which was increased gradually in subsequent tests to 200 psi (13.8 bar). When the leaks were sealed, the stopper configuration was pressure tested to failure.
The next stage of the testing programme was to overwrap the stopper with different composite materials, including fiberglass/epoxy and carbon/epoxy. Both functioned to well beyond the 100 psi (6.89 bar) requirement. The fibreglass/epoxy was effective to 250 psi (17.2 bar). The carbon/epoxy composite was effective to 487 psi (33.57 bar). Additional testing validated the stopper’s chemical compatibility with common process materials.
The Leak Stopper has been installed in the field successfully in multiple leak scenarios, proving its ability to stop a range of leaks. Response kits, providing both the stopper and materials for a composite overlay are now being provided to industry.