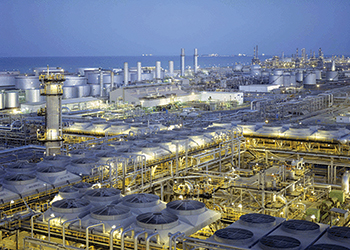
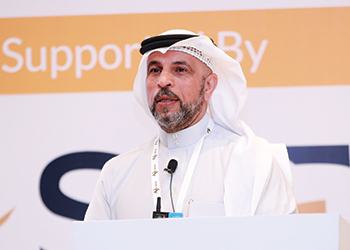
In this exclusive article for OGN, welding expert Adnan Al-Awwami identifies the primary sources that influence welding that if exploited can help achieve optimum quality and reduce welding risks
The hydrocarbon, petrochemical and nuclear industries have had many catastrophic and fatal failures over the years, and the number of new incidents is disturbingly increasing and getting more severe and costly. This is disappointing and pessimistic especially since our industry is not learning from past failures to protect its communities and assets.
Weld failures are taking a good share of the most tragic incidents worldwide. Three of the most famous weld failures include Union Oil Company Refinery in Romeoville, Illinoi, US; Chevron Refinery Fire in Richmond, California, US; and Gas Processing Plant in Antwerp, Belgium.
These three incidents have cost an estimated $1billion (with some pending claims), and killed tens of workers and injuring or medically affecting hundreds others, and taking months to fix and resume operations.
Apart from these incidents, there are countless other unreported weld failures that have caused tremendous loss of asset and human life. The failure to report weld failure incidents will significantly increase the risks and downgrade weld quality.
There are some primary sources that influence welding and which can help achieve optimum quality and reduce welding risks if exploited jointly and smartly:
INDUSTRY WELDING CODES AND STANDARDS
![]() |
Industry welding codes and standards have been found to have |
Piotr Paluszkiewcz, Regional Technical Manager Middle East and Africa of Applus+, highlighted some of the technical weaknesses of ASME Section IX - Welding, Brazing, and Fusing Qualifications in a blog titled 'Why following ASME Section IX is not (always) enough'.
Being a veteran user of ASME Section IX myself for about 30 years, I have found some shortfalls in the welding requirements. For example, ASME IX does not consider the welding technique (forehand or backhand) in corrosion resistant weld overlay qualification as an essential parameter though the technique affects the corrosion performance of the weld overlay.
An awkward issue about the welding codes is that welding requirements are directly linked to the oil prices. Whenever the oil prices go down, the welding requirements do as well. This justifies why the welding codes write a statement in the scope section claiming they take no responsibility for any undesirable outcome when using the subject code. Therefore, the welding codes do not provide any guarantee of the final weld quality even if we follow them loyally.
INDEPENDENT INVESTIGATION ORGANISATIONS
Some countries with large hydrocarbon, petrochemical or nuclear industries have independent investigation and legislative agencies responsible for investigating catastrophic failures. For example, the US Chemical Safety and Hazard Investigation Board (CSB) conducts root cause investigations of chemical accidents, and then issues rules or recommendations for implementations.
Similarly, the Hazards Forum (HF) in the UK is a group of engineering institutions that studies industrial disasters and publishes lessons learned for public awareness of how to mitigate that risk and avoid further potential failures.
Unfortunately, in our region, we do not have any entity with a similar role as CSB or HF to enhance safety and reduce risks in welding. This is why most of the local industrial companies form their own investigation committees after an industrial incident, and they deal with it in the most confidential way. Following the incident, the affected company revises its own specifications and procedures to avoid reoccurrence. However, this does not safeguard other companies in the same country from experiencing a similar failure because of no knowledge sharing.
PUBLIC INFLUENCE
Civil society organisations, and environment or human protection movements have great influence in elevating the safety requirements and by extension the welding requirements too. But we don’t have this leverage in our region. The anti-nuclear movement or one of its alliances, for example, organises demonstrations when a company is planning to build a nuclear facility that introduces risks to the people of the environment.
What this does is it forces the company owner to establish sound and thorough engineering specifications to maximise the plant’s integrity. The options may be to develop more stringent welding requirements, elevate the weld inspection programme, apply more advance non-destructive testing techniques, etc. This accordingly reduces the chances of weld failures. A point worth highlighting here is that some welding consumables manufacturing companies had to invest huge amounts in improving their products just because of pressure coming from civil society organisations.
WELDING ENGINEERING
It is often thought that a welding engineering role rises only during industrial facility construction because welding is an execution discipline. This is an entirely wrong perception.
The implementation of good welding engineering at all stages of an industrial project (initiation, planning, execution and closure) provides great opportunity to foresee the welding risks and find the solutions.
A welding engineer can engineer the welds based on the project’s base materials, design conditions, nature of the service and ease of fabrication and maintenance. For example, some types of welds, namely socket welds, have inherent fabrication problems such as incomplete penetration (IP). Unfortunately, because of the small size of all the socket connections and the awkward welding geometry, it is very difficult to detect this IP defect regardless of how advance the applicable inspection technique was.
That defect, during operations, may develop to a fatigue failure resulting in shutting down the whole plant or causing big damage. Therefore, during the project phase, the welding engineer can develop a special training programme to qualify the welders or specify some welding accessories in order to ensure the soundness of the socket welds. The welding engineer is the caretaker of the deficient conditions that influence the final weld quality.
Such high number of industrial catastrophic failures should urge us to continue relentlessly to look for welding risk areas and provide solutions. Every welding failure should give us the opportunity to sit together, think, analyse and take corrective actions to prevent similar welding failure elsewhere. Lack of sharing knowledge and overlooking the welding engineering contribution convert our industrial facilities to ticking time bombs that may set off at any moment.
• Adnan Al-Awwami is an ex Saudi Aramco and Sadara projects welding engineering consultant. He holds a BS degree in Mechanical Engineering from University of Portland and has more than 30 years of experience in the oil and gas and petrochemicals industries. In January 2015, he established Industrial Solutions Engineering Consultations (ISEC) that specialises in Welding and Materials engineering consultations. Al-Awwami was appointed by the American Welding Society (AWS) as its international consultant in the GCC, and later covering the Middle East.