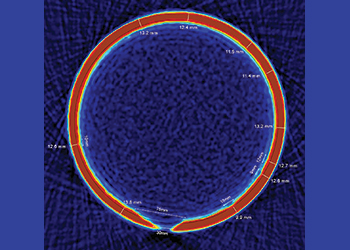
.jpg)
Pipelines can suffer many types of damage and these require urgent rectifications. Here Adnan Al-Awwami discusses common in-service weld repairs of carbon steel pipelines in sour service
Pipelines are the most economical and fastest way to transport liquids or gases to different locations within the same country or even from one country to another. Hence, without a pipeline, it is extremely difficult — if not impossible — to transport oil, gas, natural gas, water to desired destinations. Pipelines are simply similar to arteries that deliver oxygenated blood to different organs in the human body.
However, pipelines may experience some damage because of aging, operational upsets, change of content service, bad batch of the construction material, original fabrication problems, or any external factors. The examples of pipeline damage include external and internal corrosion, dents, cracks, wrinkles, girth or seam weld defects, etc. Such damage require rectifications and the pipelines industry has developed various methods of in-service weld repair where pipelines shutdown is not required.
Two fundamental welding problems can jeopardise most of the pipelines in-service weld repair —the burnthrough and the development of high hardness areas. This article will address the weld repairs of in-service carbon steel pipelines in sour service. Followings are the common in-service weld repairs:
Full encirclement sleeve welding
• Cut and replace:
To execute the welding successfully, the welding procedure must take into account the mechanical properties, chemical compositions, microstructure and heat treatment condition of the pipeline original material. For example, welding preheat may need to be higher than the ones in the current design code or engineering specifications because the original material weldability is inferior to that of the new section. The lower preheat may cause hard heat affected zones on the old material sides that would develop due to fabrication or in-service hydrogen cracking. The welds can be completed using cellulosic electrode (such as, E-XX10) for the root pass and low hydrogen electrode (such as, E-XX18) for the fill and cap passes.
• Weld buildup: Weld buildup repair is applicable to onshore pipelines to restore wall thickness loss due to internal or external corrosion. In some cases, it might be the only viable option to repair the corroded areas especially if located on the pipeline fittings (such as, tees, elbows, reducers, etc) or process equipment (such as, valves, filters, cyclones, etc). Weld buildup is a low-cost and fast repair process that does not require big crew to do the work. However, it requires thorough engineering evaluation and careful execution; any mistake would lead to explosion and fatalities. In addition, if the pipeline corrosion damage is numerous and scattered in small area of the pipe section then it would not be practical to use this kind of repair.
It is important to develop a special welding procedure simulating the actual in-service repair; that procedure may apply temper bead technique using E-XX18 class of electrode while controlling the heat input. The maximum safe welding heat input can be determined using engineering calculations or software issued by renowned and official entities such as the Pipelines Research Council International or European Pipeline Research Group. It is advisable when qualifying the welder to weld several mock-up samples to perfect the welding practice.
Weld build up
• Hot tapping:
Welding a branch pipe to the carrier pipe — with or without a reinforcing pad — is a very critical welding operation. The welding procedure should use only low hydrogen electrode (E-XX18). The success of hot tap welding mostly relies on the welder capability to apply the welding procedure with perfection. This requires that the welder welds more than one welding test coupon to ensure that his performance is consistent.
• Full encirclement sleeve: This type of pipelines repair is very common and has been in use for so many years with great success. Sleeveing the pipeline is a little bit expensive and time consuming because it requires big crew and heavy equipment. There are three general types of sleeves: reinforcing sleeve; pressure containing sleeve; and special configuration sleeve (for example, sleeves to contain leaking weld or coupling).
We are only concerned about the pressure-containing and special configuration sleeves because these are influenced by the design pressure and operation conditions. The drawback in using these sleeves is that their ends must be fillet welded, and if the pipeline experiences cyclic pressure then the welds would eventually experience fatigue failure. Hence, it is recommended that the fillet weld be dressed to have concave profile to minimise the risk.
• Patching and half-sole: Patch and half-sole pipeline repair is generally a temporary, simple and fast procedure. A patch is bended circular, square or rectangular plate (fits the contour of the pipe) with curved corners. A half-sole is a half encirclement sleeve that covers half of the pipe perimeter. However, they are both applicable to cover some external damage where the remaining wall thickness is still good to hold the maximum design pressure. Some of the pipelines damage that may employ this type of repair are shallow pits less than 0.8 t deep, shallow cracks less than 0.4 t deep, or minor attacks on the pipe seams.
Patch or half-sole are installed by fitting them snugly over the affected area and then the ends are fillet welded using low hydrogen electrode (E-XX18). It is expected that the fillet welds, which are not strength welds, would experience leaks because the pit or the crack would eventually propagate through thickness. Hence, they both should be removed and a new pipe section is installed or a permanent repair is applied when the pipeline owner or operator deem necessary.
Pipeline in-service repair is a magical solution to avoid shutdown and production loss. However, weld repair requires evaluation, precision and competency to avoid catastrophic consequences such as puncturing the pipe (burnthrough) that would result in hydrocarbon leak and fire or fast cooling of the weld (quenching) that would lead to hydrogen cracking.
• Adnan Al-Awwami is an ex Saudi Aramco and Sadara projects welding engineering consultant. He holds a BS degree in Mechanical Engineering from University of Portland and has more than 30 years of experience in the oil and gas and petrochemicals industries.
In January 2015, he established Industrial Solutions Engineering Consultations (ISEC) that specialises in Welding and Materials engineering consultations. Al-Awwami was appointed by the American Welding Society (AWS) as its international consultant in the GCC, and later covering the Middle East.