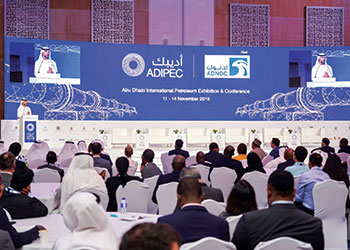
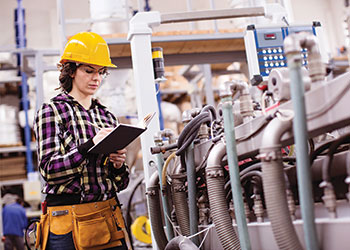
To streamline acceptance by the EPC contractor, end user or code authority, a skid should be evaluated and inspected as a complete, integrated system, rather than a collection of individual pieces of equipment, says Michael Slowinske, Engineering Manager at UL*
Driven by the need to shorten overall project timelines, process system modularisation is growing in demand for hazardous locations applications.
Building process systems into skid assemblies, a modular process skid contained within a frame, allows the process system to be easily transported and quickly installed.
Individual skids can contain complete process systems, or multiple process skids can be combined to create larger process systems or entire portable plants. Skid types include equipment, oilfield, pump and tank skids. These skids are used in applications including petroleum, chemical, electrochemical, marine, production, refining, transportation and oilfield.
According to Michael Slowinske, Engineering Manager at UL, a global safety certification company, for hazardous locations (HazLoc/Ex) skid assemblies, verifying compliance can be difficult if you only consider the individual components.
He explains: "Skid assemblies typically contain a wide variety of components with multiple applicable standards, thus making the certification process complex. Adding global market access requirements exponentially increases the level of complexity. This can create regulatory issues and unplanned delays in getting a product to global markets."
Therefore, it is critical for assembly manufacturers to consider the entire system comprehensively in order to shorten the time to market.
To streamline acceptance by the engineering, procurement and construction (EPC) contractor, end user or code authority, a skid produced by an assembly manufacturer should be evaluated and inspected as a complete, integrated system, rather than a collection of individual pieces of equipment. Finding a conformity assessment body that is knowledgeable in a wide variety of global standards and has the expertise to evaluate systems and components is key.
Applying the correct standards for the current and/or potential market(s) for product use is important to help ensure all relevant safety concerns are addressed. Some of the key requirements in different markets include:
• UL/C-UL Mark: UL 2011, Outline of Investigation for Machinery, is used to certify skid assemblies for use in hazardous (classified) locations in the US. Additionally, the hazardous location aspects may require additional protection technique standards to be applied. Wiring would need to comply with the National Electrical Code (NEC) applicable hazardous location parts.
• IECEx System: IECEx skid assemblies can be evaluated in accordance with IEC TS 60079-46. This standard was specifically written to address concerns related to certification of hazardous locations Ex skid assemblies across global markets. For wiring that interconnects individual parts of an assembly, IEC 60079-14 would be used. IEC TS 60079-46 currently requires the equipment to also be evaluated for non-electrical ignition hazards using ISO 80079-36.
• ATEX Directive: ATEX Ex skid assemblies can be covered by the European ATEX Directive (equipment and protective systems intended for use in potentially explosive atmospheres in Europe), involving the EN 60079 series of standards (as well as EN 50381 for transportable ventilated rooms) and EN/ISO 80079-36.
* UL is a leader in technical compliance services for skids, machinery and other types of assemblies typically used in hazardous locations. For individual pieces of hazardous locations-rated equipment, it assists with verification of the conditions of use and development of the documentation package or provide certification for each individual piece.