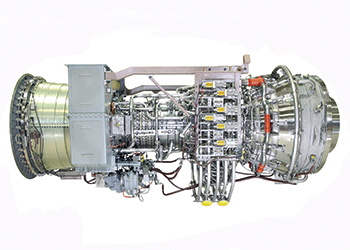
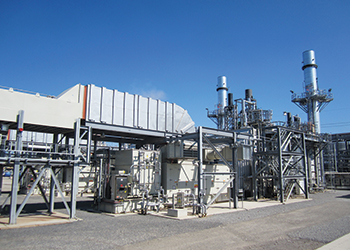
Three case studies demonstrating the benefits of gas-turbine-based power and heat solutions in a downstream environment were done to understand the use of gas turbine solutions in refinery or petrochemical installations
With increasing attention given to greenhouse gas emissions by global supply chains, improving energy efficiency and reducing environmental impact are two areas where the downstream industry must excel.
"One solution offering an excellent return on investment is the use of hydrogen-rich fuel gas. Commonly available in refining and petrochemical processes, this excess or underutilised gas presents an opportunity to minimise fossil fuel CO2 emissions and cost when power and heat are produced onsite, and grid dependency when the plant power is imported," says a spokesman for Solar Turbines, a Caterpillar company.
He says energy efficiency programmes, revamping and new processing unit installations are freeing up hydrogen-rich gases that once were flared or incinerated in boilers. Now, they can be processed using the most efficient natural-gas-fired power (and heat) technologies: gas turbine combined heat and power (CHP) and combined cycle power plants (CCPP).
The result is inexpensive and sustainable heat and power, produced far more efficiently than competitive technologies in similar power ranges. For example, 5 to 30 MW CCPPs are 10 per cent more electrically efficient than boiler-plus-turbine solutions.
Solar Turbines began development of hydrogen capabilities for turbines in the year 2000 and reached one million operating hours with hydrogen-rich fuel gas (defined as H2 content higher than 50 per cent) in 2016. The company did some case studies to understand if a CHP should be based on a steam turbine or gas turbine, and in which condition is a gas turbine combined cycle (CCGT) system a better investment than a boiler-plus-turbine power plant.
Open cycle in an off-grid refinery: This refinery, located in tropical Asia or Africa, has Gas B available and a 4.5-MW power requirement. The installation country’s grid is unstable, and in-house production of electricity will reduce unexpected shutdown costs, which is critical for the refinery. This case study compares a hydrogen-rich fired gas turbine to a diesel engine. A gas engine comparison is not included due to the H2 content of the gas, its low "methane number" and the consequences on maintenance and power derating.
At the specified conditions, the Taurus 60 gas turbine can produce 4,959 kW at the generator terminals. The corresponding refinery fuel gas volume flow is 1,445 Nm3/h (899 scfm) to meet the turbine’s full load, and refinery Gas B fuel gas must be compressed to meet the gas turbine requirement. The required fuel gas compressor electrical load is 150 kW. As a result, a Taurus 60 gas turbine meets the refinery’s 4.5 MW power needs.
In this simplified case, considering standard capital and operating expenses for the various solutions, installing a gas turbine using a refinery-gas fired Taurus 60 is more advantageous than choosing grid-imported electricity or a diesel-fueled engine, thanks to a very short payback period and strong return on investment. The cost of Gas B, which otherwise would be flared or incinerated, is nearly zero, while diesel costs amount to multiple millions of dollars per year.
Combined cycle in a Western Europe Plant: This steam turbine power plant (STPP) in Western Europe has access to tail gas, such as Gas A, which typically is fired in a conventional boiler to produce the steam to drive a steam turbine.
This case study compares a Titan 130 CCPP to a boiler-plus-steam-boiler configuration (STPP). As a tradeoff between steam cycle efficiency and capital investment, the boiler and heat recovery steam generator (HRSG) produce steam at 40 bars and electrical efficiency ranges between 28-30 per cent.
In these ambient conditions, the Titan 130 produces about 14.8 MW and the volume flow of gas is approximately 8,150 Nm3/h (5066 scfm). As in Case Study 1, Gas A is compressed from 3.5 bars to the gas turbine skid edge pressure. The fuel gas compressor power requirement is estimated at 1.2 MW. Based on the steam flow produced by the HRSG, steam turbine power production is estimated at 4.8 MW.
In total, the Titan 130 CCPP produces 18.3 MW while the STPP produces 12-13 MW using the same amount of fuel gas. For this case study, the power difference is imported at the grid rate.
This discounted cash flow (figure 2) trend shows the advantage of installing a gas turbine combined cycle for hydrogen-rich applications despite the lower investment cost of the STPP solution.
Case Study 2 assumes the continuous availability of Gas A. However, the Titan 130 CCPP can operate with 100 per cent natural gas, pure Gas A or any blend of both gases – enabling uninterrupted operation and production of power (and heat) even when Gas A flow is not continuous. When tail gas is available, it can be absorbed by the gas turbine, eliminating the need for flaring and reducing fossil-fired power generation. The current technology used by Solar Turbines results in lower CO2 emissions and fuel costs since it does not require limitation of the H2 content in Gas A or blending Gas A with natural gas.
Cogeneration with hydrogen-rich gas: The plants power requirements in this case study are 5 MW, and steam requirements are 12.5 t/h (26,896 lb/h) at the following steam conditions: 10 bara and 215 deg C respectively (145 psia and 419 deg F). Gas C is available at 1.5 bara (21.8 psia) and must be compressed to meet the gas turbine skid pressure. This study compares the performance of a gas turbine CHP plant (or tri-generation in the schematics) to a condensation steam turbine with steam extraction, with the missing power imported from the grid.
In these conditions, a Taurus 60 gas turbine produces 5571 kW at the generator terminals, and the fuel gas compressor requires approximately 250 kW to bring the gas to suitable gas turbine skid edge pressure. Eventually, the power produced is approximately 5 MW net, considering various HRSG loads.
Studies showed that at power costs higher than $0.05/kWh, NPV is better for a gas turbine CHP, making it the solution of choice at these conditions.