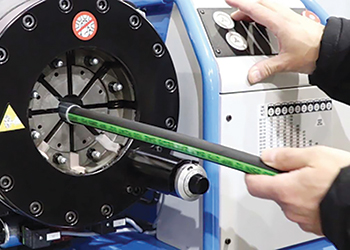
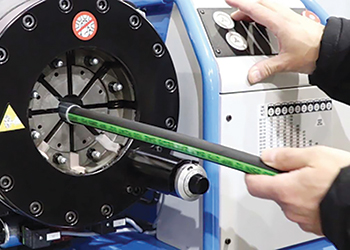
Continuing with its focus on oil contamination, leading hydraulic solutions provider MH HYDRAULICS highlights the importance of choosing the right hose to prevent early failure of the system and reduce the risk of oil getting contaminated
Hose assemblies are integral part of hydraulic systems and hence utmost care must be taken in their selection, manufacturing and installation. One of the main causes of oil contamination is hose failure as oil gets contaminated during the process of replacing damaged hoses and fittings. Therefore, making hose assemblies right the first time saves time, money and unplanned equipment downtime.
A hydraulic system’s hose assembly design needs to focus on the required working pressure, flow rate, medium, temperature and the application. Incorrect hose length will not allow the hose to expand/contract due to changes in pressure or temperature and causes excessive stress on the fittings or hose reinforcement.
Hose and fittings are made of a unique blend of different materials with complex manufacturing methods; human error, inconsistent machinery or poor product quality or raw materials can result in defects or variances.
During installation, twisting a hose rather than naturally bending it will reduce life. It is estimated a seven per cent twist when installing a hose in a permanent application can reduce hose life by 90 per cent.
Kinks, crushed sections, and cover damage, which exposes reinforcement, will eventually break down the reinforcement and lead to a hose failure.
Failure from a defective hose will typically occur in the first few hours of service, such as pinholes, blow-outs, or tube and cover separation. Improperly installed or selected clamps can result in the coupling ejecting from the end of the hose.
A hose is not ‘pipe’; it is a flexible component that will degrade over time with a shelf/service life of up to 20 years, depending on its composition, application, and environment.
Several factors are to be considered while selecting the hose fitting, including the compatibility of the fitting to the hose, one- or two-piece design and the correct assembly. A one-piece hose fitting is highly recommended to avoid selection mistakes.
In addition, correct equipment must be used for hose crimping. Finn-power from Finland has many years of experience to create a reliable crimp.
Cleaning of hose using foam pigs and use of shrink plugs while delivering would make sure there are no dust or particles inside the hose. Hoses that are subjected to external abrasion can be protected with external sleeves like that from Safeplast in Finland.
What are various types of hose configurations available? The technical article in our online edition (https://www.gulfconstructiononline.com) provides the details.
In Tech Talk next month, MH Hydraulics will explain hose storage, hose testing and reliable/clean hose packaging to achieve a safe, leakproof, long-life hydraulic system can be achieved.