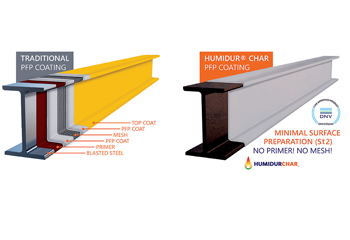
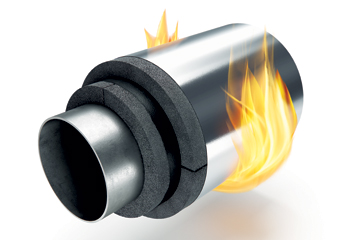
Properly specified insulation systems provide extra time for worker evacuation, the activation of first responders and can aid in the prevention of structural collapse caused by fire, Jente Quintens, Marketing Manager EMEA at Owens Corning, tells OGN
Industrial facilities that use, process or store flammable petrochemicals or hydrocarbons must have a passive fire protection strategy in place to help safeguard their critical assets such as piping, equipment, structural elements, tanks and storage vessels in case of a fire.
Wherever flammable materials are present, so is the risk for a fire and an ignition source or spark may be all that is needed to trigger it.
Specifying systems that effectively contribute to passive fire protection has the potential to save lives in the event of a hydrocarbon-based fire or explosion.
![]() |
The double-layererd FOAMGLAS is a lightweight insulation |
Such systems contribute by providing valuable extra time for worker evacuation, the activation of first responders and can aid in the prevention of structural collapse caused by fire.
Beyond providing thermal resistance, proper insulation can offer passive fire protection in industrial settings beyond operating temperatures in processes.
Properly specified and installed insulation systems deliver up to several hours of protection against fire.
These systems can guard against extreme temperatures, manage thermal flux, and extend the time for protected elements to reach dangerous temperatures where structural strength can be lost.
FIRE PERFORMANCE TESTING
Fire testing is a means of determining whether fire protection products meet minimum performance criteria as set out in dedicated norms and standards.
Different testing methods are used to determine the reaction of a product in terms of fire resistance, flammability, smoke resistance and the ability to help to prevent a pipe or piece of equipment from reaching a specified temperature too quickly when exposed to a fire.
Meeting these performance criteria allows for the safe specification of suited products in fire protective systems.
Two commonly referenced standards for passive fire protection systems are UL 1709, the standard for rapid rise fire tests of protection materials for structural steel; and ISO 22899, which determines the resistance of passive fire protection materials and systems to jet fires.
The UL-1709 is specially designed to create the unique conditions of a petrochemical plant fire and measures the hourly protection afforded steel during a rapid temperature rise that reaches 1,093 deg C (2,000 deg F) within five minutes.
Additionally, the fire environment within the furnace is to develop a total heat flux of 204 kW/sq m (65,000 Btu/h/sq ft) within that time frame.
The burning rate and fuel energy potential here are totally different from fires involving typical building construction materials.
The amount of time before failure occurs dictates the time rating of the protection granted by that insulation or insulating system.
The ISO 22899 jet fire test focuses on material response to directional or intensive and localised fire events.
During the test, insulation or the insulating system is exposed to 14 megawatt (0.3 kg/sec) horizontal flames produced by a propane fuel system projected out of the standardised jet nozzle for various time periods, depending on the rating, to simulate the intense jet fires that hydrocarbon facilities can face.
The test stops when a single thermocouple reaches 400 deg C (752 deg F) above the initial ambient temperature at the beginning of the test.
INSULATION MATERIAL PROPERTIES IN PASSIVE FIRE PROTECTION SYSTEMS
When specifying insulation systems for passive fire protection of structural steel, equipment, piping and storage tanks, engineers should consider relevant material properties, the process environment and the required level of fire protection.
Materials properties such as combustibility, absorbability, smoke development and possible loss of mass in case of a fire can help determine which products would be most suited for a set of design considerations and environmental conditions.
An insulation material that is often preferred in passive fire protection systems is non-combustible cellular glass insulation.
In addition to its non-combustible properties, cellular glass insulation is also trusted in industrial and mission-critical applications, as it is impervious to moisture.
For example, FOAMGLAS® cellular glass insulation is a lightweight insulation that comprises completely sealed glass cells.
The material is inorganic, non-permeable and will not give off smoke in case of a fire. It has a wide service temperature range from -268 deg C to 482 deg C (-450 deg F to 900 deg F) making it suitable for use in both cryogenic and steaming hot applications.
PASSIVE FIRE PROTECTION SYSTEMS
Since thermal insulation only reduces the rate of heat transfer, rather than stopping it, insulation material type, thickness, layering, cladding and tertiary materials are important in determining the overall level of prevention.
Thoroughly selecting a system or combination of insulation materials tailored to the environment and application can help lengthen the time that materials perform in case of a fire.
Based on the application systems can consist of insulation materials that are paired with additional materials, such as jacketing or coatings.
In some hybrid systems, the insulation can even be combined with an intumescent coating to provide extra protection. When exposed to high levels of heat, intumescent coatings char and expand to further slow heat reaching the underlying structure.
TESTED SYSTEMS FOR PROVEN PERFORMANCE
Protection against hydrocarbon-fueled fires can sometimes benefit from a combination of different materials to form a system best suited for that environment or application.
For this reason, a series of insulation systems incorporating FOAMGLAS cellular glass and/or PAROC® mineral wool insulation along with jacketing and other accessories was tested for fire performance using either ISO 22899 or UL 1709.
The results offer insight into the types of time ratings achieved by different passive system designs.
For example, insulation intended for use on ambient or below ambient equipment, including piping, tanks, or structural steel, could consist of one layer of FOAMGLAS® ONE™ cellular glass insulation with PITTSEAL® sealant, PITTWRAP® B100 jacketing and 0.4 mm (0.016 inches) stainless steel cladding.
When tested using UL 1709, this set-up provided up to 30 minutes of protection. The same insulation system with 0.7 mm (0.027 inches) stainless steel cladding also achieved 30 minutes of protection when tested according to the ISO ‘jet fire test’.
Combining cellular glass insulation with mineral wool insulation not only gives you great fire protection but also provides noise reduction and acoustic performance.
A design that combined FOAMGLAS cellular glass insulation with PAROC mineral wool pipe insulation, mass loaded vinyl, and stainless steel cladding reached Shell DEP Class D performance when tested in accordance with ISO 15665 for sound isolation performance.
Beyond providing acoustic performance, it also gave great passive fire protection results when tested for jet fire and rapid rise fire performance.
When tested in accordance with ISO 22899 it provided up to 120 minutes of protection. When tested for UL 1709 it provided up to 180 minutes protection.
Additionally, passive fire protection systems can combine different materials to optimise performance.
Owens Corning’s hybrid design combines cellular glass insulation with PPG Pitt-Char® NX and carbon mesh. This hybrid system can be adapted for both below and above ambient conditions, and provides up to 240 minutes of protection in a jet fire situation.