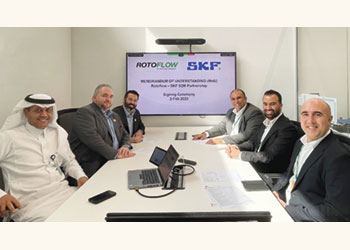
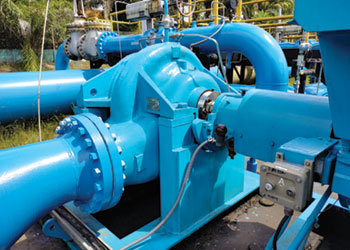
Pumps need to be protected and maintained properly in order to maximise their effectiveness in terms of power usage as well as to minimise the revenue lost when a pump fails and causes a system backup, writes Kent Davenport, Oil and Gas Industry Manager at VEGA Americas
The oil and gas industry relies heavily on pumps for operation. This is particularly true when it comes to the transportation of oil and water throughout the system to manage the desired product provided downstream as well as the undesirable product produced by oil and gas wells.
Pumps need to be protected and maintained properly in order to maximise their effectiveness in terms of power usage as well as to minimise the revenue lost when a pump fails and causes a system backup.
The most typical pump used in artificial lift starts at the well head of a conventional oil well and is called a pump jack.
In order to catch liquids in the well bore and move them into a check valve-type system, this pump style raises and lowers a rod connected to a beam and cam system several feet. Fluid from this system is drawn up via a hole and released for nearby treatment and storage.
Submersible pumps, which are lowered deeply into the well bore, are another popular type of pump used in artificial lift.
Another form of pump is a high-pressure (mobile) pump, which is utilised during the well bore's fracturing, stimulating, and cementing stages to increase product capture rates and speed up the process.
The liquids are placed in various tanks on the premises after being transferred via separation. These tanks are divided into those for storing oil and those for waste, the majority of which is generated water, often known as saltwater.
Depending on the system design, oil may either be taken up by tank trucks or transported further downstream to a larger central gathering system for additional processing. After that, it is transferred to bulk storage on the way to the pipeline and ultimately the refineries.
The produced water goes through a similar process. Water can either be carried away or pumped through a pipe to a saltwater disposal facility (SWD), where high-pressure pumps are used to inject the water into a disposal well that extends below the surface.
Once the liquids have reached the first stage of collection, two types of pumps are typically employed in these applications: centrifugal and positive displacement (PD) pumps.
Centrifugal pumps draw fluid into the inlet side and out of the outlet side using the centrifugal force of an impeller that is powered by a motor. Due to their ability to move quickly at low pressures, they are more frequently used in oil transfer applications.
Centrifugal pumps can occasionally lose prime because of low levels or empty tanks, which is a drawback.
The pump's impeller, bearings, and other components may deteriorate as a result of this condition's potential to cause cavitation and heat accumulation.
Damage over time results in at best subpar performance and ultimately catastrophic failure.
Positive displacement refers to the pumping of a constant volume of liquid per cycle or stroke.
On the SWD disposal side, these pumps are more frequently encountered.
Due to the fact that there is no fluid slippage in the pump gears or plungers, they can produce higher pressures with less power than centrifugal pumps might need to.
In comparison to centrifugal pumps, this decreased power consumption results in financial savings. Another benefit of PD pumps is that higher pressure is more crucial in these applications than higher flow rates.
PD pumps and centrifugal pumps both have the drawback of being susceptible to damage if the unit pumps dry.
This is due to the tight tolerances inherently present in their design as well as the potential for heat and friction to be produced when they run dry.
Fortunately, there are more modern pump designs and variations on existing technology that can account for unfavorable circumstances.
Some pumps even have built-in monitoring that can be used to turn them off before a catastrophic breakdown occurs.
Even with all of the advancements in pump technology, there are still a ton of outdated systems in use, and many of the pumps that are now being offered do not make use of these advancements.
Many producers and contracted disposal sites employ affordable external methods of pump protection for their expensive systems as earlier pump technology is still widely used in the field.
One approach to determine if a tank is being emptied to the degree that a dry pump condition can develop is through tank level monitoring.
These days guided wave radars (GWR) or pulse radars are replacing mechanical-style float devices as the primary means of continuous level measurement.
This can be done using the Modbus and HART protocols, as well as a scaled signal like a 4-20 milliampere (mA) output to a local programmable logic controller (PLC).
The PLC can be set to also function as a pump shutdown at a predetermined level in the tank by using the same scaled system from the transmitter as loaded in the PLC. As a backup alarm, a second lower-level setting can also be employed.
Pressure-based transmitters can also be used to monitor tank levels. One pressure transmitter is fitted in vented tanks at a location where it will activate above the height of the outlet pipe.
Similar to radar transmitters, it scales the output to the PLC based on the head pressure of the fluid in the tank.
Due to differences in density, head pressure on a water tank will be greater than an oil tank at a given height; this data is crucial to understand when setting up the scaled output.
The transmitter or the PLC can be used to do this. Additionally, since using the wrong pressure range transmitter and not knowing how much mixed fluids will be in the tank will reduce accuracy, these factors must be taken into account.
There are additional ways to safeguard a pump in the oil and gas sector than those already listed.
However, because of their mechanical nature and the environments they are exposed to, products that can seize up and fail are no longer as desirable to use.
Many manufacturers have moved away from mechanical systems due to their dependability problems as the cost of additional solid-state devices has decreased over time, primarily due to the volumes being supplied today.
In any instance, it's critical that the user assess what makes the most sense for their system and select the approach that best suits their requirements.