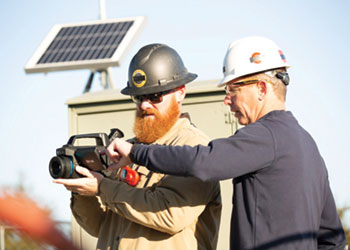
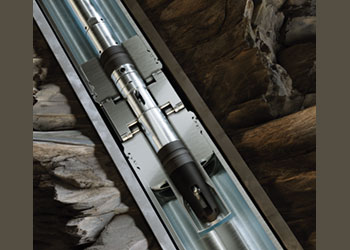
Interwell systems have been deployed across the world in difficult environments to provide fast and cost-effective solutions to major challenges in the oil and gas industry.
These solutions have saved operators both time and cost, increased productivity, and in certain instances helped reduce emissions.
Interwell technologies have succeeded and have also made possible remote operations.
These systems and solutions can be better understood with the help of actual case studies:
ISOLATING EXTENSIVE LEAKS AND REINSTATE GAS LIFT FUNCTIONALITY
• Challenge: A major operator in Qatar was looking to isolate an 85-ft leaking section in the completion string below the side pocket mandrel (SPM) along with a suspected gas exit at the SPM in a high-producing oil well.
Assigning the well to a workover would have been an expensive and lengthy process wherein the well would have to be shut down for extended periods leading to loss of production.
The client was looking for a quick and efficient solution to restore well integrity without compromising the functionality of the gas lift and reinstate production back to optimum levels.
![]() |
Figure 1 ... the APS Isolate extensive leaks in wells |
• Solution: Interwell proposed a multi-run anchored production straddle (APS) based on the ME design retrofitted with a Go-lift sub to restore the gas lift capability.
The APS (Figure 1) was then customised to cover the entire leaking section including the SPM. The lower section was initially set, followed by two sets of spacers on a GS, and finally, the upper section fitted with the Go-Lift was latched onto the bottom sections.
• Value created: The APS was mobilised to the location within two weeks, and the operation to be completed within three weeks from the date the plan was established.
This enabled the client to significantly reduce production downtime and quickly switch the well back online.
IRSV REMOTELY OPENED AFTER 674 DAYS
• Challenge: A major operator on the Norwegian Continental Shelf was planning to batch complete 10 middle completions.
![]() |
Figure 3 ... the RockSolid creates a gas tight barrier against |
The challenge was to find a robust system that allowed for temporary suspension leaving an ISO 14310 V0 qualified barrier in the well.
After the suspension period, the upper completion—which refers to all components from the bottom of the production tubing upwards—was to be installed before the rig moved away and a light well intervention vessel installed an x-mas tree—a piece of equipment that provides flow control on an oil or gas well. The goal was to perform all these activities with minimised mechanical intervention.
• Solution: Interwell proposed using an Inter Remote Shatter Valve (IRSV), which is a multicycle, remote-activated glass plug. IRSV (Figure 2) is known for its robust cycling mechanism and debris-friendly system.
The plug was installed as part of the completion tubing with the glass being bi-directional ISO 14310 V0 qualified. With predetermined cycling setup, the plug cycles open leaving a full-bore ID through the valve.
• Value created: Through using the IRSV, the operator was able to batch complete all wells with a reliable barrier in place from temporary suspension to the XMT was installed.
The IRSVs were successfully cycled open on all 10 wells and no intervention was required. The longest suspension period, from installation to remotely opening, was 674 days.
ROCKSOLID™ BARRIER SYSTEM IS A SUCCESS
• Challenge: An operator in Canada had experienced multiple challenges on one of its wells with severe SCVF (surface casing vent flow) issues, of approximately 13.5 cu m per day.
Several attempts with different existing technologies had been made without success in order to stop the sustained casing pressure/surface casing vent flow.
Shutting off the flow of hydrocarbons is a requirement by regulators before being allowed to abandon a wellbore. Conventional methods to shut off the flow of gas are unreliable, have poor longevity, and are time consuming operations.
• Solution: The Interwell plug and abandon (P&A) RockSolid™ tool (Figure 3) utilises an in-house engineered THERMIT® mixture to remove casing and annular cement while, in the same run, creating a gas tight barrier through the entire cross-section of the well, against hydrocarbons flowing from below.
THERMIT is an exothermic material which releases large amounts of energy when ignited from the surface through the e-line cable.
The tool was successfully run in hole to a pre-defined setting depth adjacent to competent caprock, before initiating the reaction in order to melt the surrounding well elements.
An extensive verification process was initiated post operation to verify that we had established a rock-to-rock barrier.
The annulus was continuously monitored for gas flow for several months and the results were immediate.
The flow rate continued to decline over the next weeks before falling below a measurable threshold—less than 50 litres of gas per day.
Subsequent pressure build-up indicated no pressure on the annulus side, and the gas flow was finally confirmed shut off by passing a bubble test. No bubbles from annulus vent over 15 minutes.
• Value created: The RockSolid barrier sealed the inside of the casing and created a gas tight barrier where the caprock was restored to its original integrity, permanently, across the well’s cross section, sealing both vertically and horizontally.
REACHING OPTIMAL INJECTION DEPTH
![]() |
Figure 2 ... the IRSV is known for its robust cycling mechanism and |
• Challenge: An existing well in the UK sector of the North Sea was not originally completed with gas lift mandrels, and the well was needed to be shut-in for an extensive period to build up pressure. With the well put on production, it soon loaded with water and production ceased.
• Solution: Interwell demonstrated how the well production rate could be improved by utilising two GoLiftTM (Figure 4)straddle subs within the 5-1/2-inch production tubing.
In order to reach the optimal injection depth, one unloading and one operating valve was installed.
• Result: The GoLift systems enabled lift gas to be injected at nearly 7,500 ft which allowed the operator to achieve steady production of 1,000-1,500 barrels per day of oil.
It was estimated that the costs for the entire intervention operation, including all equipment, personnel and the intervention vessel were recovered after 68 days of production.
By Abdulaziz Khattak