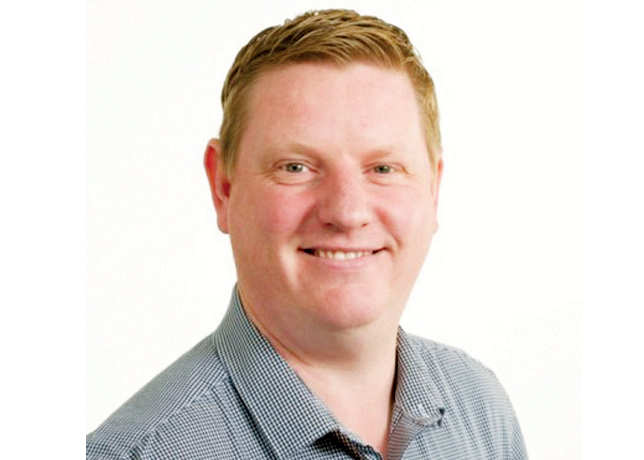
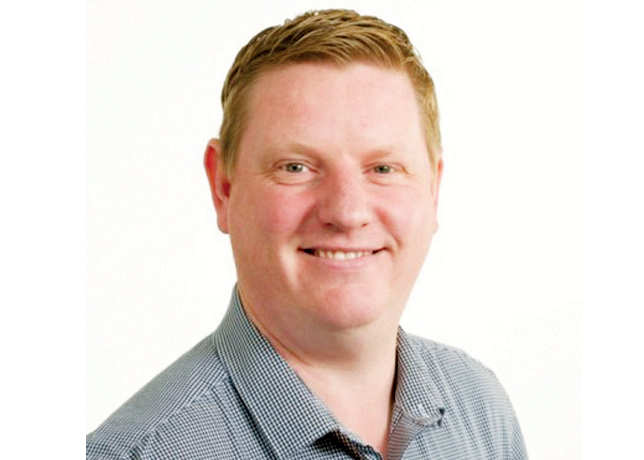
Oil and gas companies can cut costs and boost efficiency by involving filtration experts early to optimise systems, reduce maintenance, and improve performance, Chris Nixon of Cleanova tells OGN
IL and gas companies are spending millions of dollars unnecessarily due to missed opportunities to optimise performance, minimise maintenance, and reduce total cost of ownership (TCO).
"Poorly specified and maintained filtration systems are all too common in our experience, and they inevitably cause higher costs down the line," says Chris Nixon, Engineering and Products Director at Cleanova.
"We urge those responsible for plant design, operation and maintenance to involve filtration experts earlier, so they can save money and reap the benefits that an appropriately designed and sized filtration system can bring."
Cleanova points to over-reliance on generic datasheet specifications as a key reason why filtration systems are poorly designed and maintained.
The practice commonly results in oversized filtration systems, resulting in higher capital costs, or sub-optimal filter choices that mean the system is designed to fail.
They caution that standard filtration specifications should only be used as a starting point.
![]() |
Cleanova’s innovative Gas Filtration Test Skid performs on-site analysis of contaminant levels without interrupting production |
Nixon says: "Filtration systems should be developed based on the customer’s priorities and using application-specific data to optimise filtration sizing and media selection. Ideally, post-commissioning tests should also be conducted to double-check that system operating parameters match predictions. Variations in flow and contaminant levels directly affect filtration efficacy, leading to more frequent filter replacement or even system failure."
WHY FILTRATION MATTERS
Filtration is not only a vital part of traditional oil and gas production, it is also critical to the success of emerging sustainable technologies such as carbon capture, storage and utilisation (CCUS).
Deployed at key points to remove solid and liquid contaminants, properly specified filtration systems contribute directly to the quality of the end product.
Filtration also prevents damage to vital equipment involved in the respective processing stages, which would be very expensive to replace.
If a filtration system is not properly specified or is poorly maintained, additional costs can quickly accrue. Warning signs include:
• An increase in the frequency of filter element change-out.
• Higher than anticipated maintenance frequency.
• Extended periods of downtime.
Operational costs often rise too, because a blocked filter can lead to increases in energy consumption as the processing system attempts to maintain flow rates.
Expensive additives may also be required to achieve the desired product quality.
If left unchecked, poor filtration performance can ultimately lead to loss of reputation, loss of business and lower profitability.
SLASHING COSTS
To illustrate the value of involving filtration experts earlier, Cleanova cites a Middle East customer who had used generic flow calculations when specifying a new filtration system as part of a plant upgrade to improve product purity.
Based on the generic criteria, tenders for the filtration package could only propose an over-sized solution that literally would not fit the physical space available in the plant.
To solve this problem, Cleanova took a different approach. They worked with the customer to understand their specific purity requirements and then assessed the entire production process to determine the type and size of contaminant that the new filtration system would be required to remove.
![]() |
Cleanova Dollinger filters installed at a wellhead injection site in the Middle East |
Using the client-specific criteria, Cleanova were able to design a new, compact filtration skid that would meet the physical space constraints and exceed the efficiency requirements of the application.
"Our custom filtration solution was more compact and used fewer elements, which reduced CAPEX by 40 percent and halved the OPEX compared to a generic system," says Chris Nixon.
"As a bonus, the lower cost enabled faster budget sign-off and meant the customer was quicker to market with its higher purity product."
PROCESS CHANGES
Alongside poor initial specification, a change in process is often the root cause of filter failure.
Both root causes may result in higher levels of contamination than anticipated in the product flow, which leads to filters becoming clogged. While compressors and engines will keep on going, the filter becomes the point of failure because it is overloaded.
"Nine times out of ten, the reason for failure is not the filter’s fault," says Chris Nixon.
One industrial customer who called in Cleanova had been overspending on maintenance for years due to inadequate filtration.
The concentration of solid and liquid contaminants in the recycled gas stream from a DRP reactor was causing higher change out frequencies than expected and adversely affecting production.
Cleanova mobilised its innovative Gas Filtration Test Skid at the customer’s site to perform an analysis of the process gas over several days – without interrupting production.
This unique capability is part of a suite of services that form a total aftermarket approach called Cleanova.CARE. Encompassing on-site testing, aftermarket spares, rental rigs and expert support with capital upgrades, Cleanova.CARE has been developed to facilitate collaboration between Cleanova and its customers to achieve the best possible filtration outcome.
The samples were analysed by Cleanova and independent laboratories to determine the actual process gas conditions.
The analysis determined that the current filters provided an initial removal efficiency of 93-95 per cent at 50 µm: but there were significant volumes of particulates in the range of 2–40 µm present in the flow.
These finer particles, combined with the presence of high residual liquid concentrations, were forming a slurry on surfaces downstream.
These deposits were affecting the filter element structure, process pipework, valves, and the internal compressor surface/blades.
Permeability tests also highlighted that the flow permeability of the 50 µm filter was reduced by more than 2025 per cent due to liquid saturation of the media.
The wetting of the filter media occurs very quickly, so the differential pressure starting point is higher than that for a dry gas application.
Based on these results, Cleanova recommended a reconfiguration of the existing filter to 98 per cent at 100 µm, reducing element differential pressure and improving operational life.
A finer filtration system downstream was also recommended to achieve the customer’s optimum requirement of 5-10 µm whilst still improving the operational lifetime overall.
IMPROVE COMPETITIVENESS
It is clear from these real-life examples that filtration experts like Cleanova can deliver tangible benefits at every stage of the filtration lifecycle.
Their early involvement in system design and specification, and their trouble-shooting expertise when maintenance issues do arise, can help to shorten lead times, improve operational efficiency and drive down costs – all of which improve competitiveness for oil and gas operators.