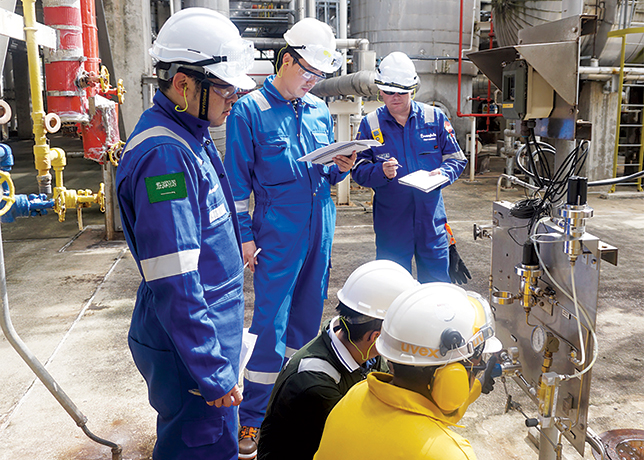
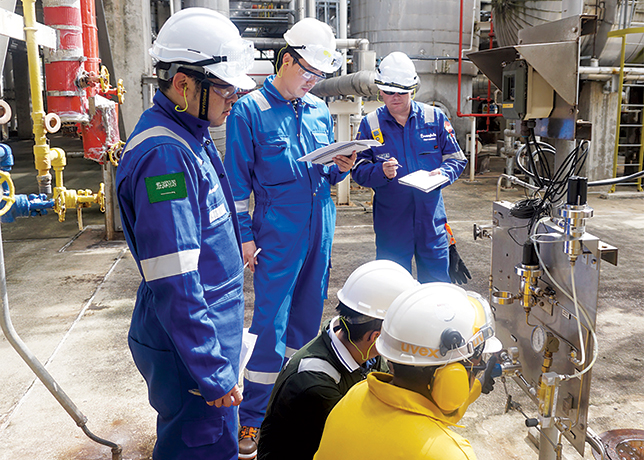
Swagelok® field engineers enhance fluid system performance, improve uptime, reduce costs, and mitigate risks with onsite evaluations, expert solutions, and comprehensive improvement roadmaps
Every day, experienced Swagelok® Field Engineers apply their technical and application expertise to help customers solve pressing challenges related to fluid system design, installation, operation, and maintenance.
The Swagelok-certified, local engineering team at Swagelok Saudi Arabia perform onsite services to help clients diagnose and resolve fluid system issues to improve operational performance, reduce cost and labour time, and help mitigate safety, quality, and environmental risks.
HELP INCREASE UPTIME & RELIABILITY
Swagelok fluid system experts help clients maintain the health of their fluid systems, avoiding equipment downtime, lost production revenue, and unnecessary troubleshooting and repairs.
Swagelok can find and measure the scale of fluid system problems, prioritise improvement recommendations, and supervise installation.
Swagelok field engineers have deep experience with various plant systems and equipment packages from OEMs so they can evaluate and enhance:
• Analyser sample conditioning systems.
• Laboratory and process instrumentation systems.
• Grab sampling systems.
• Mechanical seal support systems for rotating equipment.
• Gas distribution systems.
• Steam systems.
![]() |
A Swagelok field engineer doing Grab Sampling Evaluation |
TYPICAL SWAGELOK® ONSITE SERVICES
• Fluid system evaluation and advisory: Swagelok field engineers conduct a site evaluation of the client’s facility, detect and calculate costs of leaks, advise on design and installation practices, and recommend prioritised system enhancements in a comprehensive report. Their report will provide solutions that address vibration concerns, corrosion potential, incorrect component choice or installation, inadequate supports, and more.
• Analyser sampling system evaluation and advisory: Achieve improved sampling system excellence when it comes to time delay, representativeness, and compatibility. Reduce time delay, ensure representativeness of the sample, and deliver a compatible sample to the analyser for analysis with Swagelok expert, in-depth analysis of every sampling system component and subsystem, from tap to analyser.
• Grab sampling support: Without proper grab sampling system design and maintenance, critical actions like capturing, handling, or analysing samples that are timely, and representative of the client’s process can be difficult to achieve. Working with Swagelok experts produces more accurate, compliant, safe samples while reducing costs.
• Gas distribution evaluation and advisory services: Overlooked leaks of costly gases can also reduce client profits and create safety hazards for team members. Swagelok gas distribution evaluation and advisory services involve fluid system advisors providing critical analysis to help clients avoid these issues, informing proper regulator selection, identifying system upgrade opportunities, and guiding the design and assembly of gas delivery solutions.
• Steam system audit services: A Swagelok steam system specialist will help clients conduct a detailed assessment of their plant’s steam systems and components, document and tag areas needing attention, and share best practices for repairing and maintaining the facility’s systems.
• Hose advisory: Eliminate a variety of hose-related issues that cause safety concerns, unplanned downtime, low product yield, or costly part replacements by engaging with local Swagelok hose advisors who conduct site evaluations and provide prioritised improvement recommendations.
![]() |
Swagelok field engineer showing an engineering report |
WHAT TO EXPECT DURING THE ONSITE VISIT
1. The client identifies the system or systems that need to be evaluated.
2. A Swagelok certified team conducts a field assessment of those systems.
3. The team identifies opportunities for process improvements.
4. Upon completion of Swagelok onsite service, the client will receive a comprehensive 'Improvement Roadmap' engineering report that identifies key issues and recommended quantifiable solutions, including:
• Costs of existing, unrepaired leaks.
• Areas for improvement categorised by severity.
• Photos to clearly identify locations of problems.
• Steps that can be taken to remedy them.
5. The Swagelok local team will collaborate and provide support throughout the implementation process. Through its onsite services, Swagelok offers:
• Design services.
• Fabrication and assembly services.
• Training on product installation and best practices.
• Product selection consulting.
• Bill of materials (BOM) and piping and instrumentation diagram (P&ID) generation.
• Leak identification and repair prioritisation.
• Preventive maintenance recommendations.
CASE STUDY: SWAGELOK FIELD ENGINEERS RESOLVE UNKNOWN PROBLEM
Are you certain that your systems are operating optimally? What if you had an analyser that you believed was performing properly, but then discovered that the analyser was actually giving you false data?
A customer was experiencing longer-than-anticipated response times on its analyser and called in the Swagelok field engineers for support.
The team performed a system evaluation and discovered that the fluid was changing phases multiple times as it traveled from tap to analyser.
Phase changes in the sampling line can deliver a sample to the analyser that is not representative of the process.
Consequentially, the customer was making process changes based on inaccurate analytical data. Through recommendations provided by Swagelok® team:
• All phase changes were eliminated.
• Response time was vastly improved.
• Analytical results were now representative of the fluid in the process, providing the customer with superior process control.