
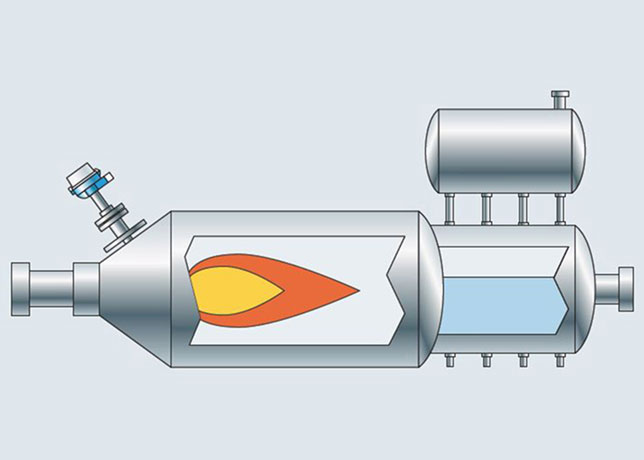
Innovative solutions from Endress+Hauser enable accurate temperature measurement in the Claus process, ensuring reliable sulfur recovery, operational efficiency and environmental responsibility in refineries, writes Michele Pietroni, Industry Manager - Oil & Gas and Chemical, Endress + Hauser
The Claus process is the industry standard for recovering elemental sulfur from hydrogen sulfide gas, crucial for refineries processing sour crude oil.
Conducted in a Claus furnace or Sulfur Recovery Unit (SRU), this process efficiently removes pollutants and prevents the emission of harmful gases.
The Claus process involves two steps:
• Burning a portion of H2S to form SO2 in the reaction furnace.
• The reaction of H2S and SO2 in a 2:1 ratio forms elemental sulfur.
These reactions are turbulent and aggressive, with the acid gas stream being partially oxidised with a low amount of O2, releasing significant exothermic energy.
Temperature control is challenging as the feedstock temperature often exceeds 1600 deg C (2912 deg F), making thermocouple temperature measurement technology essential for monitoring this process.
![]() |
Before and after (right) |
The inner temperature of the reactors during the sulfur reaction must be continuously and accurately monitored to prevent plant shutdowns and optimise the energy consumption:
• It must be high enough to sustain the reactions.
• It must not be too hot to avoid damaging the refractory lining, which protects the structure against quenches and destruction caused by severe thermal conditions and aggressive process media.
• It must be steady and homogeneous to maintain the plant’s efficiency.
THE CHALLENGE
This application is highly corrosive and combines numerous high temperature phenomena, making it exceptionally challenging and requiring a highly experienced and knowledgeable supplier for design and installation.
The long-term accurate temperature measurement combined with high mechanical and thermal strength of the instrument is crucial to ensure plant integrity and optimised process.
![]() |
Installation |
Three thermometers are normally installed in each reactor, and all the units must be able to operate in particularly aggressive environments with vibrations and with significant thermal displacement of the refractory wall, which generates high forces on the instrument.
• Thermal expansions and rapid temperature changes contribute to:
o Thermowell breakage.
o Thermocouple wire breakage.
• Sulfur dioxide and hydrogen sulfide cause contamination of TC wires due to the increased porosity of ceramics of the thermowell at high temperatures.
• High risk of thermowell breakage from falling refractory bricks.
• Thermocouple drift and damage increased by:
o Corrosive vapours and gases penetrating the ceramic thermowell.
o High hydrogen sulfide content, which attacks the platinum wires inside the thermowell, causing faster drift and embrittlement.
INNOVATIVE TEMPERATURE MEASUREMENT SOLUTION
A modified version of the iTHERM FlameLine TAF12D high-temperature thermometer including a ceramic thermowell, TC type B,R,S and further technical modifications is used:
• Thermowell material selection to withstand the harsh environment (1st layer): C799 high purity alumina ceramic with high hardness, mechanical strength, wear and chemical resistance.
• Internal protecting sheathes in special metal alloy and ceramic (2nd and 3rd layer) to protect platinum TC sensor wires from polluting substances and to stop and contain toxic flu ds leakages.
• Protection of the thermowell against the mechanical forces from thermal displacements of the bricks is achieved by a protective Nickel-Chromo super alloy sleeve. Precise clearances between the sleeve and installation passage protect the ceramic tip from mechanical loads, minimising mechanical failure risks.
• Atex 2014/34/EC compliance can be reached by certified components according to the requirements ruling the Ex d type of protection for Gas and Dust hazardous atmospheres.
• Limitation and prevention of permeating contaminants by up to three ceramic barriers with different performances installed into the thermowell tip. The materials range from alumina to silicon carbide to zirconia, with different grades depending on the percentages of the compounds Al2O3, SiC, MgO.
• Avoidance of TC contamination: using a hydrogen flame to weld the TC hot junction ensures high temperatures for melting platinum wire and prevents contamination, as hydrogen is very clean when burnt.
To protect the most important component of the measurement, the thermocouple itself, two solutions have been proven in practice. The choice depends on whether there is an N2 line near the installation area.
• Instrument with purging system with inert gas N2/argon gas is supplied continuously or periodically from a line at site with an average flow rate of 2 to 6 l/min to not affect the reading of the TC. The gas will purge and clean any contaminants present inside the ceramic thermowell. This solution may even include a cutoff valve. If the tip is broken and the purge system is useless, the valve can be activated to cut the insert and separate the external environment from the process itself.
• Pressurised instrument N2 / argon gas is injected at installation with a holding pressure of 1-2 bar higher than the process pressure. The customer must periodically check the pressure level and recharge if necessary. The higher pressure suppresses the migration of contaminants inside the ceramic thermowell.
END-TO-END CUSTOMER SUPPORT
We support customers from the design and conception phase to the correct installation, with or without pre-heating, to reduce the risk of thermal shock and prevent the thermowell from failure or breakage.
We also assist with calculations to determine the perfect installation depth of the thermometer, defining how far inside the reactor it should be to achieve the desired accuracy, but with the least risk of thermowell damage.
The Endress+Hauser modularity concept ensures that different spare parts are available and can be ordered as standard components.
Specifically, the insert is replaceable and can be removed from the instrument under working conditions after an accurate check of any eventual leakages. It can be replaced for calibration purposes or because of ageing due to thermal stress.
For data visualisation, the thermometers located at different points of the reactor can be connected to the RIA15 process indicator or the Memograph M RSG45 to read the data conveniently from anywhere at any time.
RESULT & BENEFITS
The Endress+Hauser solution achieves the highest accuracy and significantly improves the durability of the thermowell and the thermocouple.
This improvement is due to the elimination of factors that lead to contamination of the thermocouple wires and the significant reduction of the negative effects of thermal expansion and mechanical forces on the thermowell.
The adjustable immersion length leads to accurate temperature mapping, contributing to reliability.
CONCLUSION
Temperature measurement in the Claus process is one of the most challenging tasks in sulfur recovery due to high temperatures, corrosive gases, and mechanical stress.
With innovative solutions like the iTHERM FlameLine TAF12D thermometer, Endress+Hauser provides refineries with reliable, long-lasting, and accurate temperature monitoring, ensuring operational efficiency, regulatory compliance, and environmental responsibility.