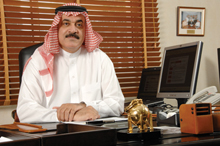
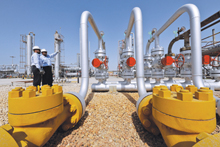
BAPCO launched its current five-year strategic plan in 2010. The main focus of the plan is on refinery expansion, enhanced trading in the international markets, and improved human resource policies and processes and intensification of oil and gas exploration activities in the country.
So far, under the current strategic plan, Bapco has been able to effectively achieve a crude supply agreement to secure feedstock for many years ahead. The biggest achievement of the current strategic plan was the successful implementation of performance management.
Bapco’s management systematically reviews all strategic activities to enable the plan to evolve and grow and also coordinates and aligns resources and actions with its mission, vision and strategy.
MAJOR STRATEGIC PROJECTS
Bahrain Aromatics Complex: A concept of building an Aromatics Complex in Bahrain, next to Bapco was developed.
After the completion of the Bapco modernisation programme (BMP), Bapco will produce a total of about 96,000 bpd of whole range naphtha. About 56,000 bpd of this will be heavy naphtha which is suitable for aromatics production. In the current BMP configuration there is no home for this naphtha other than partial use for gasoline production.
Bapco reviewed the potential uses for this naphtha. Steam cracking based naphtha feedstock cannot compete with the ethane and other gas crackers in the region. However, the aromatics route for heavy naphtha looks very promising.
The Bahrain Aromatics Complex concept is based on building an aromatics complex in Bahrain that will use the heavy naphtha feedstock which will be available from Bapco after the BMP completion.
It is planned to have only two products, p-Xylene and Benzene. P-Xylene will be maximized because it is the most valuable product and Benzene has to be produced for technical reasons. Further integration into downstream products such as PTA, PET is possible in the subsequent phases. The intention is to progress this project further.
BUSINESS DEVELOPMENT
The major objectives of the Business Development Department are to diversify Bapco’s interests into downstream hydrocarbon and chemical related businesses, increase our exposure with international companies and increase career opportunities for Bahrainis in both local and international markets.
In 2013, the Bapco Board of Directors requested Independent Consultant Reports to be implemented for three companies which have been under study for the past 12-18 months.
Having received the consultant reports, the Board has referred one of these opportunities to Nogaholding for their comments and to confirm if there is interest to invest. The reports on the other two companies are still under evaluation.
A total of 24 target companies were identified and studied in 2013 which are now at different stages in the evaluation process. Three new target companies are being prepared for presentation to the board for their consideration in 2014.
The Business Development Department anticipates that at least one business opportunity could be realised in 2014.
In addition, the Business Development Department has participated in several “in house” projects including LPG, asphalt and marketing studies.
![]() |
Bapco ... keeping its carbon footprint low |
Meanwhile, Bapco prioritised several IT initiatives during the year to help streamline operations, improve productivity and rationalise costs.
Implementation of the first phase of the Bapco Private Cloud – launched in 2012 with the aim of consoli-dating and standardising company servers and sharing IT resources to reduce ownership costs – made significant progress as more than 60 eligible physical servers were transferred to a virtual environment.
A $5.5 million project to launch a new Engineering Information Management System (EIMS) to replace the existing Engineering Document Management System (EDMS) and non-intelligent CAD sys-tems came one step closer to completion. A feasibility study and RFP [request for proposals] for the de-tailed design and implementation of the EIMS – a common database where engineering information is shared and utilised by different engineering disciplines – is scheduled for completion by the first quarter of 2014, with full implementation due in the second quarter of 2015.
To boost operational excellence, and improve user access and data entry and analysis, electronic audit survey forms were implemented for permit to work, lock out tag out, management of change, stop work authority, safety audit, managers tour form and operational readiness check functions.
Technology also played a role in tightening organisational information and data security during the year, a purpose-built CSMART (computer security management and response team) operation centre being established to co-ordinate security responsibilities across the company.
Bapco also stepped up the security of its assets by successfully taking over responsibility from the vendor of an upgrade to the Oracle-based Security Access Control System.
Enhancing employee output was a focus of IT work during 2013. For example, Bapco became the Gulf’s first company to implement Microsoft Lync 2013 Enterprise Video Conferencing.
An Automated Confidential File Memorandum (CFM) Workflow was, meanwhile, developed in-house, enabling CFMs to be created and circulated electronically, one of a number of time saving initiatives launched in 2013. Another was the development of a web interface to manage a ‘Lesson Learnt’ database for employees as part of the Bapco Modernisation Programme (BMP), replacing manual data analysis previously saved in an Excel spreadsheet.
Among other IT achievements at Bapco during the year was the migration of 930 PCs from Windows XP to Windows 7 with minimal disruption to users’ productivity; the migration to e-banking payments to local and international vendors and employees; the introduction of a new fuel management system (Sadeem) at service stations across Bahrain; the implementation of an engineering project information and tracking system (SageCRM) for work requests; and the automation of international marketing functions for crude oil orders from the Abu Safah field, enabling more efficient process cycles.
Bapco continues to provide petroleum engineering expertise to Noga and nogaholding as the kingdom’s quest for additional sources of oil and gas turned to new offshore and onshore projects in 2013.
A key focus of upstream attention during the year was preparatory work for a new offshore exploration bid round relating to four blocks relinquished by Occidental Bahrain and Thailand’s PTTEP in 2012.
Geological and geophysical evaluation of the four blocks, including rock sample analysis, was conducted by two international consultancies with the objective of upgrading the prospectivity of the blocks by better understanding their characteristics.
Following an agreement signed with Tatweer Petroleum, onshore exploratory well Al Mamtalah-1, located in south west Bahrain, was drilled to a total depth of 8,610 feet to explore for and test Hanifa unconventional resources.
DEEP GAS INITIATIVE
Following detailed geological, geophysical and engineering analysis conducted in 2012 under the terms of an Exploration & Production Sharing Agreement (EPSA) for the onshore Deep Gas Initiative, attention turned to the logistics of drilling the first deep exploratory well in this complex, technically challenging and unconventional reservoir environment.
Bapco’s Deep Gas technical team, working in conjunction with its counterparts at Occidental Petroleum (Oxy) of the US, selected the optimum well location and drilling while completion design was fine tuned. This work was part of a monitoring and technical audit of the first phase of the exploration project.
Furthermore, long lead drilling materials were selected and orders placed with a view to spudding the well in 2014.
BAHRAIN FIELD DPSA
Bapco continued to represent nogaholding in the OpCom, TeCom, Contracts Committee and Studies Steering Committee taking care of the kingdom’s interest in the Development and Production Sharing Agreement (DPSA) for the onshore Bahrain field.
The company’s responsibilities in the DPSA, which seeks to increase oil and gas output and enhance recoverable reserves in the Field, extended in 2013 to putting forward further recommendations on optimising oil and gas production; providing insight on associated gas management to reduce gas flaring and offering support for a gas plant study; coordinating studies conducted by consultants aimed at understanding current DPSA processes; and stepping up cost control measures.
Furthermore during the year the company initiated a mechanism by which it regularly receives and archives data generated by Tatweer Petroleum for the Bahrain Field. Furthermore, Bapco also critically reviewed Tatweer’s 2014 Annual and Five-Year Plans, generating several future development scenarios to support the overall field development plan.
A Business Continuity Plan was also prepared in the event of Bapco assuming responsibility for Field Operations.
WASTE WATER TREATMENT PLANT
A Waste Water Treatment Plant, WWTP, was officially inaugurated in December 2013.
The WWTP Project has been implemented as part of Bapco’s Environmental Strategic Plan in line with the requirements laid down by the Supreme Council for the Environment at a total cost $120 million. The new plant will provide secondary treatment to the refinery waste water that is received from the existing primary treatment facility.
The WWTP is based on four-stage Membrane Bio-reactor Technology and will be the first global installation of this size in any refinery waste water treatment facility, operating under the extreme water salinity and temperature issues that are experienced in Bahrain. The treated water specifications meet some of the most stringent regulations in the world. With this project, Bapco and Bahrain have been put on the world map for using innovative technologies in environmental conservation.
STEAM TURBO-GENERATOR PROJECT
In February and March 2013 Bapco successfully commissioned the $108-million steam turbo-generators which replaced four old units. The units were officially opened in April 2013. The STG project was awarded the MEED Quality Awards for Projects in 2013.
The immediate benefit of the STG was replacement of four old, unreliable and unsafe units, by two new state-of-the-art safe and reliable units. The new STG’s are equipped with sufficient redundancy that allows for maintenance repairs without the need to shut down.
Operationally the new units are easier to control and have resulted in more stable operation due to online control and monitoring systems. Operational cost reductions have been noted in lower energy loss and sea water consumption. The control of 110# steam generation and the refinery steam balance have been easier and the optimisation more efficient.
REFINERY MARGINS
The Refinery Gross Margin for 2013 is $6.48/bbl which exceeded the business plan target of $5.29/bbl. This high gross margin relative to target was achieved despite the tough prevailing market conditions over the last couple of years. In addition, given the tight market conditions, the refinery has embarked on an active programme to contain and reduce operating costs.
The truly remarkable effort can be clearly seen by the ever narrowing gap between Gross and Net Margin over the last three years. This is an indication of improving operating cost and in 2013 the YTD operating cost was $449,000. The Net Margin for 2013 is $1.81/bbl which again is above the target of $0.27/bbl.
CRUDE RUN
The refinery processed an average of 263,829 barrels per day (bpd) during 2013 compared to an expected budgeted crude run of 254,407 bpd. This remarkable achievement was primarily due to early start-up of crude units following T&I’s, as well as very high on-stream factor of the crude units. An additional 3.4 million barrels was processed compared to budget.
The refinery processed an all-time high of 47.7 mbpd Bahrain crude during 2013, as well setting a new monthly crude processing record in January of 271,807 bpd.
HIGH-VALUE MIDDLE DISTILLATE
A very good Middle Distillate yield of 57.4 vol per cent was achieved in 2013 which exceeded the annual target of 55.6 vol per cent and in addition showed an improvement on the 2012 yield of 57.1 vol per cent. The Middle Distillate yield has been the highest recorded yield over the last three years. This was achieved despite unfortunate unplanned shutdowns of 1HCU and FCCU in the summer. In the 4Q, 2013, 1HCU was operated at an average feedrate of 52,078 bpd which is the highest sustained feedrate in Lube Base Oil mode.
The average Diesel Pool Sulphur for 2013 was the same as for 2012 at 0.05wt per cent.
MINIMISED LOW-VALUE HEAVY ENDS
The yield of low-value products (Heavy Ends) of 19.8 vol per cent exceeded the annual target of 19.1 vol per cent and was marginally higher than the 2012 yield of 19.3 vol per cent. This was primarily due to lower than expected asphalt sales. However in 2H 2013 asphalt sales improved and the expectation for 2014 is continued higher demand. Asphalt production peaked at 3.7vol per cent in September, this is the highest monthly yield over the last three years.
Asphalt production has continued to be profitable compared to fuel oil sales and sales of asphalt were maximized within the market. Production averaged 2.7 vol per cent (7,085 bpcd) and the estimated profit compared to selling as fuel oil over the year was $92.00/mt compared to the annual target of $50.00/mt.
LPG AND NAPHTHA RECOVERY
A total of 2,591 mmscf of refinery off gas was sent to Banagas with a total recovery of 574,214 barrels of propane, butane and naphtha. The recovery in terms of barrels is lower than 2012, primarily due to unplanned shutdowns of 1HCU and FCCU, the shutdown of Banagas Central Gas Plant I and the economic shutdown of the platformer.
OPERATIONAL AVAILABILITY
The plant operational availability at 91.97 per cent for 2013 is lower compared to 2012 value of 93.6 per cent. This is attributed to the planned T&I’s for 2013 and the unplanned shut downs of the FCCU and HCU.
Jet/Kerosene Flash Point: As per continual improvement initiatives, a 0.5 deg C reduction in Kerosene Flash Point, at an estimated benefit of $110,000 per month (using 2009 prices) has been realised. The trial targeting a flash point of 39.0 deg C min commenced mid-February 2010. The average Jet/Kero flash point achieved over the 2013 period was 39.0 deg C. This resulted in a corresponding benefit of $1.9 million for the year considering the shift in Kerosene Flash Point.
REFINERY MASS LOSS
The refinery continued in managing mass loss and averaged 0.58wt per cent for 2013. This continued maintenance of mass loss would not have been possible without the ever vigilant dedication of all Bapco personnel.
Energy Usage: Energy Intensity Index, EII, is an industry standard that measures and ranks the energy efficiency of a refinery. The correlations used in the EII calculation were revised by Solomon during the 2008 study. For 2013 an EII of 129.8 was achieved. This is lower than 2012, and the preceding two years.
Lost Profit Opportunity: Unfortunately, the refinery incurred very high LPO in 2013 compare to 2012. Even though only 6 reliability clock resets were experienced in 2013, compared to 14 in 2012, the high LPO value can really be attributed to the high margin units that were affected by the operational upsets. The LPO, for 2013 compared to 2012 increased from $0.20/bbl to $0.35/bbl.
Below are the five major LPO’s in 2013:
• Loss of HVGO yield on 6VDU due to problems associated with the column top bed and overhead system over April, May and June, $10,510,400;
• Controlled shut down of 1HCU in July to replace the drive end seals on the RGC, $8,945,500;
• 1HCU slowdown over June/July due to unavailability of 1SRU Waste Heat Boiler, $3,505,200;
• 1HCU shutdown in August in order to resolve the high differential pressure on product stripper bed, $3,252,700; and
• Controlled shut down of 1HCU in June in order to replace RGC O-rings whose failure could lead to loss of containment, $2,606,000.
Of the top five major LPO’s it must be recognized that almost $15.1 million was lost due to safety and environmental considerations. Bapco through its commitments to OSOOL Bapco and Operational Excellence recognized the process and environmental violations and took the necessary corrective actions to ensure the well-being and integrity Bapco people and assets.
OPERATIONAL PERFORMANCE
Major T&Is: In February and March there was a planned shutdown of 5CDU and FCCU for T&I. 5CDU was shut down from February 15 to March 9 while the FCCU was shut down from February 14 to March 18.
In addition 3CDU and 1VDU was shut down from February 26 to March 8 in order to carry out maintenance on salt water line. 1VBU was shut down from March 9 to 18 in order to decoke the unit.
REFINERY RELIABILITY CLOCK (RRC)
The RRC measures the number of days the refinery remained on line without any unplanned core unit shutdown for more than 24 hours. In 2013 the target of 90 days was achieved on March 24 and on the November 28, 2013. For 2013 the Refinery managed to achieve a maximum of 142 days before the RRC was reset.
The Cumulative Number of Resets of the RRC for 2013 was 6, which is a vast improvement over the 2012 RRC Resets of 14.
• May: (1) Failure of the incomer transformer to FCC Complex substation resulting in a major voltage dip leading to the shutdown of FCCU Complex.
• June: (2) Controlled shut down of 6VDU in order to carry out essential repairs.
• (3) Controlled shut down of 1HCU to replace RGC O-rings.
• July: (4) Controlled shut down of LSDP in order to replace 1HCU RGC damaged seal.
• August: (5) Manual shut down of FCCU due to high air blower speed and governor not responding.
• (6) Controlled shut down of 1HCU in order to inspect and rectify problem in the Product Stripper.
Thus of the six RRC Resets, two of the resets were operational safety considerations and 3 were conducted in a controlled manner in order to rectify operational problems.