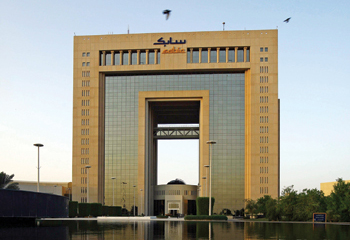
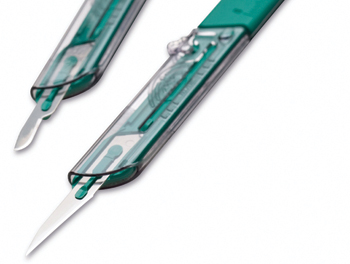
FOCUSED on helping the healthcare industry reduce costs, Sabic’s Innovative Plastics business has added to its diverse and relevant solutions portfolio with the introduction of two new grades of high-modulus carbon fibre reinforced thermoplastics.
A growing opportunity for medical device manufacturers includes a shift from using traditional metal or other fibre-filled materials in their applications to plastic. Sabic is working with its customers to support this shift with two solutions that offer medical device manufacturers the potential to optimise system cost as well as improve processability.
Identifying technologies that can help optimise medical device system costs while also maintaining -or even improving – the mechanical properties of the material in an application is a key requirement within the healthcare industry today, says Cathleen Hess, director of Healthcare Marketing for Sabic’s Innovative Plastics business. The two new materials that Sabic has added are examples of our commitment to develop innovative solutions that can enable part consolidation, helping our customers to reduce both effort and cost.
Through the innovative use of high modulus carbon fibre technology that is creatively compounded with high performance resins, Sabic has developed two new compounds which have shown significant improvement in stiffness versus similar compounds with standard carbon fibre technology, making them excellent candidates for replacing metal and other fibre-filled thermoplastics. Metal replacement is becoming more important as medical devices must withstand ever increasing in-service demands due to more complex designs, performance requirements and regulations.
LNP Thermocomp EC006AQH compound, a 30 per cent carbon fibre reinforced PEI resin, is an excellent material candidate for demanding applications that require high strength and stiffness, chemical compatibility and mechanical stability in repeated, harsh sterilisation environments.
The second material innovation is Sabic’s LNP Lubricomp DCI06APH compound, also a 30 per cent carbon fibre reinforced polycarbonate resin, which combines the benefits of high modulus carbon fibre with a high-flow, ductile polycarbonate. A great candidate for applications that require high strength and stiffness, internal lubrication and good processibility, the compound can also help enable a balance between design flexibility and ease of manufacturing.
Designed to be comparable to the strength of metal, LNP Thermocomp EC006AQH compound enables medical device manufacturers to expand their use of injection-moldable engineering thermoplastics for several reasons. These include the potential for reducing system costs, achieving greater design flexibility and enhancing device compatibility with image guided surgeries. Additionally, replacing metal can also enable part consolidation, which can reduce both the effort and cost of manufacturing devices. Potential applications for this compound include either disposable or re-usable surgical instruments, patient transport devices, fixation devices and medical device housings.
Also offering an alternative to traditional material solutions, LNP Lubricomp DCI06APH compound is a high-flow material suitable for high-strength components where the use of metals or other fibre filled thermoplastics with poor flow can create design and manufacturing challenges. The compound enables complex part designs and potential part consolidation, enabling healthcare molders to reduce waste and improve cycle times.