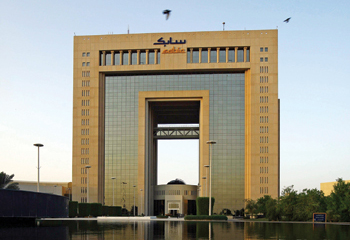
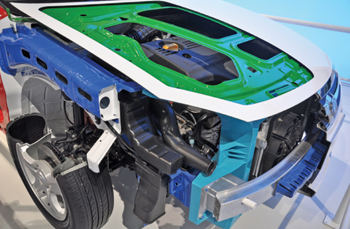
SABIC’S Innovative Plastics business has announced that it is proceeding with an investment in a production line for Stamax long glass fibre-reinforced polypropylene (LGFPP) at its manufacturing site in Shanghai, eastern China.
The new capacity, expected to come on stream during the second half of 2015, brings Sabic’s Stamax operations closer to customers in China and Asia Pacific and responds to increased demand for the lightweight LFGPP material from automakers in the region.
Leading automakers have successfully used Stamax resin as a weight and emissions reduction solution since the early 2000s, primarily for large moulded parts and semi-structural parts such as front-end modules, door modules, instrument panel carriers, tailgates and seat structures.
“With this move to bring local supply of Stamax resin to China and Asia Pacific, we are demonstrating our commitment to ensure our expanding customer base in the region has a reliable supply of this important material technology,” says Alan Leung, vice president of global and Asia Pacific commercial operations for Sabic’s Innovative Plastics Business.
Sabic currently operates two Stamax resin plants: one in Genk, Belgium, the largest greenfield polypropylene compounding plant ever built in Europe; and one in Bay St. Louis, Mississippi, which opened in November 2011.
The Stamax resin production line in Shanghai will be built using the same state-of-the-art design and technology of those in Genk and Bay St Louis. As a result, Sabic will be poised to deliver uniform product quality for its customers’ global platforms from each plant.
“With the continuing trend and importance of global vehicle platforms, it is increasingly necessary that automakers have the ability to specify and receive the same high quality material in one region as they do in another,” says Scott Fallon, general manager, Automotive, Sabic’s Innovative Plastics business. “Our Stamax resin production line in Shanghai will enable us to continue meeting this critical customer requirement.”
Increased need for lightweight-enabling materials like Stamax resin in China, in particular, comes at a time when the country is taking important strides to address the challenges of air pollution.
China’s Ministry of Environmental Protection has committed to reduce vehicle emissions, which is says to be the source of about a quarter of the country’s air pollution.
The difference made by a material like Stamax resin is evident when comparing its use in a front-end module (FEM) carrier vs. one with a polyamide-steel hybrid (PA hybrid).
According to Sabic data that has been verified by GreenOrder, a leading sustainability consulting firm, a FEM molded out of Stamax resin has a life cycle greenhouse gas (GHG) footprint of 78 kg vs 149 kg with a PA hybrid solution, a 48 per cent reduction.
That data also shows that the FEM with Stamax resin also has a lower life cycle energy footprint of 1 200 megajoule (mj) vs. 2 140 mj for one with a PA hybrid solution, a 44 per cent reduction. Scaling this data up to 200 000 FEMs with Stamax resin vs. a PA hybrid solution, a manufacturer could avoid emitting as much GHG as driving a car 100 million kilometres.
Stamax resin also enables manufacturers to advance from traditional multi-part steel components to single injection molded modules, which can help manufacturers to lower overall system costs by increasing automation and reducing additional processing and assembly.
The material is says to offer excellent stiffness across a wide temperature range and high dimensional stability.
In addition to the new Stamax resin production line, Sabic is adding on-the-ground specialists in China and Asia Pacific to strengthen its design support offering in the region.