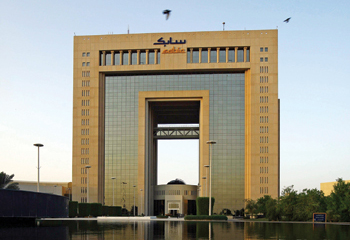
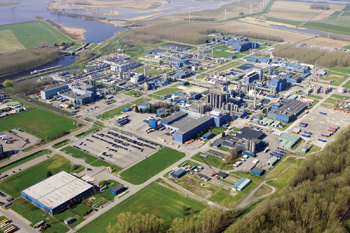
SABIC plans to manufacture and market a full range of renewable polyethylene (PE) and polypropylene (PP) by feeding “second generation” waste animal and vegetable oil feedstocks into its crackers in Europe.
The project aims to help customers, especially in the packaging sector, meet consumer demand for sustainable, renewable products.
It uses certification from the International Sustainability and Carbon Certification plus (ISCC+) scheme which certifies renewable content and standards throughout the value chain from source to end product.
Sabic expects its customers also to use the ISCC+ system to show customers the product is from a renewable feedstock.
Sabic has not needed to invest any money in new technology because, say executives, the company’s crackers in Europe are flexible enough to crack animal and vegetable oils without modification. A spokesperson says the oils and fats are hydrogenated by its ISCC+-certified feedstock supplier.
The company’s Geleen, Netherlands, cracker will be the first to produce the renewable polymers.
The ISCC+ certification works on a “mass balance system” which means that for each tonne of renewable feedstock fed into the cracker, a proportion of the output can be claimed as renewable. Sabic says independent, third party auditors have checked its reliability.
Mark Vester, business unit director for linear low and low density PE in Europe, says: “We source fuels from the market which are renewable, and this is being overseen as a chain of custody by the ISCC+ scheme which gives us the confidence that these sources are renewable. If you bought a certified renewable tonne of PP there is a direct connection between your purchase and our purchase of the certified feedstock.”
He says, Sabic is in an advantageous position because it can use the same assets where it processes standard feedstocks. “Our crackers have the ability to crack heavy renewable feedstocks and (hold) a unique position in that respect.
“We are especially happy that we have found a way to bring renewable poly-olefins to the market in this way. We are now able to offer something to the market that neither Sabic nor others could offer.”
The feedstock comes in a liquid form and its properties are similar to traditional feedstocks. “At our Geleen site (Olefins 3 and 4) we have differentiated ourselves through the use of various liquid feedstocks... We do not stop and start the cracker for the processing of these (renewable) fuels,” says Vester.
Any form of waste fat or oil which can be converted into a fuel is a suitable feedstock including vegetable oil or animal fat waste from meat processing or waste oils from other industries. The fuels being targeted are termed “second generation” because they do not compete with food.
Vester adds: “Compared to total polyolefin consumption the feedstock is limited. But we believe there is enough second generation to replace the current first generation feedstock which is on the market.”
He describes this initiative as a “drop in” solution where the properties of the products produced are identical to Sabic’s current offering. “This means they can be adopted across the value chain without any consequences for further processing or recycling.”
Sabic is now working with its customers to bring these renewables to market as finished goods such as renewable-based packaging.
“The market for renewable polyolefins is limited but we see them growing substantially faster. One of the drivers for the market will be the availability of renewable polyolefins. We are bringing renewable PP to the market which is not yet available. This availability will help to create demand: the polymers will now be available as renewables under the ISCC+ scheme.”
Vester adds that the company plans to expand renewable polyolefin manufacturing to its Gelsenkirchen, Germany, site.