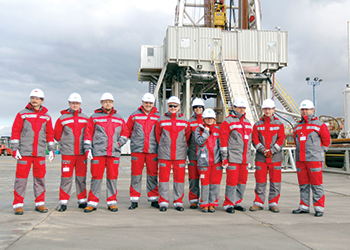
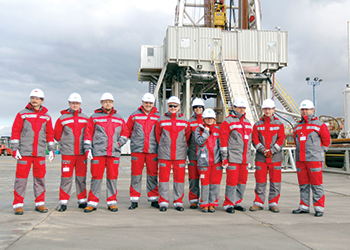
The crowdsourcing model chosen by PKN Orlen has become popular around the world. Advanced competition tools and communication channels developed with NineSigma have allowed PKN Orlen to reach innovators around the world
PKN Orlen has selected six solutions best designed to improve a refinery’s energy efficiency. The group of finalists includes companies from France, Germany, India, Poland, the UK and the US.
Despite the complexity of the challenge, PKN Orlen’s initiative attracted significant interest from innovators around the world. The submissions feature a variety of solutions enabling the use of waste heat from distillation columns (Fig. 1) for the production of electricity, chilled water and steam, among other products.
The selected solutions comprise a wide range of technologies that are already available or still in the research and development (R&D) phase. From among more than 20 submissions, PKN Orlen’s experts selected six. The submitters were scheduled to compete in March for three cash prizes, as well as the possibility of pilot project implementation and further cooperation with PKN Orlen. The winners were expected to be announced in late March or early April 2016.
The crowdsourcing model chosen by PKN Orlen has become popular around the world. Advanced competition tools and communication channels developed with NineSigma have allowed PKN Orlen to reach innovators around the world.
PKN Orlen has been actively involved in innovation-driven projects with the aim of further enhancing the group’s value. For years, PKN Orlen has initiated R&D projects in association with Polish universities and research institutes.
The aim of the contest is to find the optimum technology solution to enable efficient recovery and utilisation of low-temperature heat from distillation columns. Its implementation will not only generate savings, but it will also bring environmental benefits in the form of reduced unit energy consumption and lower emissions to the atmosphere.
A new biorefinery process developed by scientists at the US Department of Energy’s (DOE’s) National Renewable Energy Laboratory (NREL) has proven more effective at producing ethanol from algae than previous research.
The process, combined algal processing (CAP), is detailed in a new paper, "Combined algal processing: A novel integrated biorefinery process to product algal biofuels and bioproducts."
The research follows work done previously at the NREL and published in 2014. In that research work, scientists examined two promising algal strains, chlorella and scenedesmus, to determine applicability as biofuel and bioproduct producers. They concluded that scenedesmus performed impressively better, with demonstrated total fuel yields of 97 gal of gasoline equivalent (GGE) per tonne of biomass.
The cost of algal biofuel production is still a major challenge, and the DOE has set the significant goals of reducing the cost of algae production and the conversion of algal intermediates to fuels. In traditional processes, the algae produce lipids that are converted into fuels. However, simply increasing the amount of lipids in algae is not expected to bring down costs significantly. The NREL determined that further progress could be made by more completely using all algal cellular components, instead of only relying on lipids. By applying certain processing techniques, microalgal biomass can produce carbohydrates and proteins in addition to lipids, and all of these can be converted into coproducts.
In their initial work, NREL researchers determined that, through the use of a solid-liquid separation process, carbohydrates can be converted to fermentable sugars, which can then be used to produce ethanol. However, as much as 37 per cent of the sugars were lost during that process. Those trapped sugars "cannot be used for fermentation without a costly washing step, resulting in a loss of overall fuel yield," according to the report.
In their most recent work, NREL researchers hypothesised that the amount of ethanol could be significantly increased by simplifying the processing. By skipping the solid-liquid separation process and exposing all algae components directly to fermentation conditions, both ethanol (from the carbohydrate fraction) and lipids can be recovered simultaneously. Using Scenedesmus and the CAP, and after upgrading the lipids to renewable fuels, scientists are now able to produce a total fuel yield estimated at 126 GGE/t. This yield equates to 88 per cent of the theoretical maximum yield and 32 per cent more than the yield from lipids alone.
The NREL researchers were also able to recover 82 per cent-87 per cent of the lipids from the CAP, even after ethanol fermentation and distillation, indicating that the initial fermentation of sugars in the pretreated biomass slurry does not significantly impede lipid recovery.
These results led to the conclusion that the novel CAP process is capable of reducing the cost of algal biofuel production by nearly $10/GGE compared to a lipids-only process, taking the modeled cost down to $9.91/GGE. While this cost is not low enough to compete with petroleum, the approach can be combined with reduced costs for biomass production to provide a path forward to achieve that goal.
This work was funded by the DOE’s Office of Energy Efficiency and Renewable Energy’s Bioenergy Technologies Office. The NREL is the DOE’s primary national laboratory for renewable energy and energy efficiency research and development. The NREL is operated for the Energy Department by the Alliance for Sustainable Energy LLC.
EnerTrac(SE), a tank delivery automation platform for the fuel delivery industry, is a Senet IoT (Internet of Things) offering honored for excellence in innovation with the 2015 IoT Evolution Excellence Award.
The award honours innovative products that support the availability of information being deduced, inferred and directly gathered from sensors, systems and anything else that supports better business and personnel decisions.
EnerTracSE combines integrated back-office software and eSensor technology with Senet’s Low Power Wide Area Network (LPWAN) to capture all fuel tank levels, multiple times per day. Each customer’s tank data is sent to the dealer’s computer to provide a continuous report on the status of every tank. Dealers are able to consolidate deliveries, forecast fuel usage and schedule servicing to avoid run-outs, contributing to significantly increased profits and an improved bottom line.
LPWANs enable immediate return on investment by enabling devices to connect over long ranges (approximately 15 mi) while delivering long battery power life (approximately 10 yr) at a low solution cost. Low-cost, low-power and secure, the Senet Network is claimed to have advantages over cellular, WiFi and other emerging connectivity technologies for the IoT market.
SignalFire’s Remote Sensing System for tank level monitoring features an open architecture mesh network that provides a number of benefits over other technologies, including choice of sensors, wireless capacity and simple configuration.
Many tank level technologies limit interfaces to one or two types of sensors. However, the materials (oil, water, etc.) and the environment being monitored must dictate the best sensing technology. The right sensor for the job might be a radar, a float, a pressure sensor, an ultrasonic sensor, a piezo-resistive sensor or a guided wave radar.
SignalFire provides wireless modules that have an open architecture with industry-standard interfaces to permit the user to choose the sensor type that is best for the application. Sensors are easily integrated into the SignalFire Mesh Network. Supported interfaces include 1-5V, 4-20 mA, Modbus, Hart and digital inputs.
SignalFire’s systems can also power both the sensor and the radio system from either internal batteries or a specially-designed solar system. Battery life depends heavily on the choice of sensor, and can range from 1 yr-10 yr.
SignalFire’s Sentinel nodes, which interface with the sensors, meet Class 1 Division 1 certification for an intrinsically safe system. Battery technology also meets these requirements and can be changed in hazardous areas without a work ticket.
A SignalFire Tool Kit makes system configuration easy through a graphical interface. Raw analog values can be converted to units of measure, and polling frequencies and power settings can be configured using the tool kit. For sensors that require in-situ calibration, SignalFire offers a Wireless PACTWare for its NodeChecker utility.
A truly valuable wireless system must deliver economic value to the customer. SignalFire systems are competitively priced when compared with 50 ft to 100 ft of installed conduit. In addition, systems can be shop-preconfigured, greatly reducing field installation time.
Schneider Electric debuted its DTN Allocation Tracker at the WPMA Expo. The tracker provides a consolidated view of product allocations on one platform for customers, saving time and improving decisionmaking.
The DTN Allocation Tracker, which will be released in April 2016 in the US, aggregates critically important product allocation information from suppliers into an "all-in-one" view, giving customers the ability to maximise fuel supply efficiency. Downstream oil and gas marketers often lose time tracking down product allocations at numerous truck rack terminals. They also risk not having the allocation once trucks arrive, and may need to send their fuel trucks to another location.
The tracking process, which was formerly time consuming and labour intensive, is available with a single sign-on, on a single screen, with the DTN Allocation Tracker.
Clariant, in cooperation with Werner & Mertz, has launched a project to expand the possible applications of bioethanol made from agricultural residues, such as straw, to detergents, cleansers and cleaning agents.
Clariant’s sunliquid bioethanol has been used in Frosch Bio-Spirit Multisurface-Cleaner since the beginning of the year. Clariant supplied the cellulosic ethanol, also called bio spirit, at the end of 2015 from its precommercial plant in Straubing, Germany, where up to 1,000 tpy of cellulosic ethanol are produced using the sunliquid process.
Alcohol has been known for its grease- and dirt-dissolving properties for decades. Through the use of cellulosic alcohol in Frosch Bio-Spirit Multisurface-Cleaner, these properties are coupled with sustainable and environmentally friendly manufacturing.
Due to its virtually carbon-neutral production, cellulosic ethanol saves up to 95 per cent of CO2 emissions compared to synthetic ethanol from fossil resources. At the same time, it is produced from local residues and does not compete with food production or arable land.
Frosch Bio-Spirit Multisurface-Cleaner Orange has been produced with the sunliquid bio-alcohol since the beginning of 2016, and is available at German retailers as of February.
Ashcroft A-Series 316L stainless steel pressure switches (Fig. 5) now offer a greater selection of process and electrical connections. With the addition of male and female ½ NPT and 37° flare pressure fittings, both watertight and explosion-proof versions can be installed in a wider variety of applications.
Additional electrical conduit fittings improve connection options, while NACE-compliant piston seals round out compatibility with sour gas. With expanded pressure ranges, the A-Series switch can now control pressure up to 15,000 psi.
Baumer’s compact RTD technology-based TER8 temperature sensor is designed for applications with demanding requirements for measuring accuracy and stringent hygienic standards. It is available both for front-flush installation and in two variants with an immersion sleeve. Based on the Baumer TE2 series, TER8 adopts the mechanical and electromechanical properties of this product family. The compact TER8 sensor housing fits into tight spots that are difficult to access.