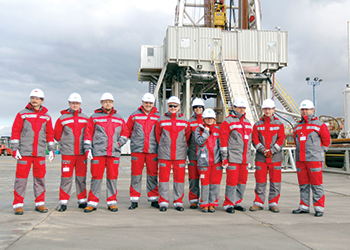
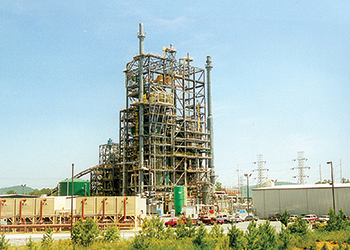
Gasification is a process in which carbonaceous materials in the presence of steam and oxygen are converted into syngas in a high temperature environment. It is partial oxidation of the feedstock in a controlled manner
Gasification offers a promising option to convert low value carbonaceous feedstocks and waste into valuable products. Traditional feedstocks for liquid and gaseous fuels as well as petrochemicals are crude oil and natural gas but are concentrated in select few regions. Gasification offers flexibility which allows use of coal, petcoke and other refinery residues, and biomass to produce a wide range of end products including but not limited to power, liquid fuels, fertilisers, SNG (Substitute Natural Gas) and petrochemicals. This paper deliberates on various aspects of gasification as a viable alternate to the conventional process schemes to produce power/ fuels/petrochemicals etc. utilising low value feedstocks and also weighs in India’s perspective on the same.
Gasification is a process in which carbonaceous materials in the presence of steam and oxygen are converted into syngas in a high temperature environment. It is partial oxidation of the feedstock in a controlled manner such that the produced syngas, which has optimum calorific value and carbon conversion from feed, could easily be cleaned up for particulates as well as undesired sulphur and nitrogen compounds. The gasification process can be summed up as combination of drying of feedstock, devolatalisation (pyrolysis) of the dry feedstock, gasification and partial oxidation reactions.
It is clear that these reactions and hence syngas composition is controlled by steam/carbon ratio, oxygen/carbon ratio in gasifier and operating temperature and pressure along with residence time in gasifier. Apart from these major reactions, nitrogen is converted primarily to N2/NH3/HCN while sulphur is primarily converted to H2S/COS/CS2. These impurities except N2 can be removed from syngas in a downstream acid gas removal unit. Raw syngas coming from gasifier is cooled and solid particulates are removed from the stream before it is sent to downstream units for further processing. There is wide range of operating parameters (800C - 1500C and 0.3 to 85 barg) for available gasifiers depending upon the feed stock and required syngas quality. Gasifiers are classified based on the flow regime inside gasifier. Table 1 highlights characteristics of each of the gasifier types. Table 2 gives salient features of commercially available gasifiers.
FEEDSTOCK FOR GASIFICATION
As stated earlier, gasification is flexible in terms of feedstock it can process. Gasifiers accept virtually any low value carbonaceous material, including: coal, petcoke and other refinery residues, and biomass. This flexibility enables gasification to extract benefits to the maximum extent out of available feedstock. Feedstocks are characterised by Proximate Analysis, Ultimate Analysis and ash characteristics which assist in determining optimum gasifier operating conditions and gasifier type to process the feedstock.
Coal gasification processes have been used commercially for more than a couple of centuries now.1 Though it was previously limited to producing gas for local lighting and heating purpose, coal gasification received great impetus during World War II when large scale commercial coal gasifiers were developed to address the liquid hydrocarbon fuel deficit of Germany which was rich in coal reserves. India’s exposure to coal gasification also dates back to 1940’s. Majority of Indian coal is characterized with high ash content, as high as 60 wt per cent, presence of chlorides and fluorides and high ash fusion temperature. Fluidised bed gasifiers and fixed bed gasifiers are better suited to process Indian coal.
Petcoke is a relatively new entrant in the gasification arena. Petcoke is produced in petroleum refineries coker units and has high calorific value. But despite high heat of combustion, it is not an ideal combustion fuel due to it’s high sulphur content, low volatiles content and low reactivity. It also has the presence of metals such as vanedium, nickel and iron and is very low in ash content compared to coal. Low reactivity demands high operating temperatures for petcoke gasification and entrained flow (slagging) gasifiers are the preferred choice for the same.
Refinery residues and asphaltenes have high viscosity and possess similar properties of high sulphur content and presence of metals as petcoke. Concept of 'Zero Residue Refinery' can be achieved by integrating gasification with refinery units with increased net energy efficiency, enhanced performance and profitability. Such integration is often referred as trigeneration where gasification plant produce hydrogen, power and steam to fulfill refinery requirements and for export as well.
Biomass gasification offers the dual benefits of waste management solution as well as producing valuable end products. Municipal waste and woody biomass (wood chips, rice husk, cotton stalks and other agro-residues) both can be used as feedstock for gasification. There is no or negligible cost for biomass feedstock, rather tipping fee could be associated for managing ‘the waste’ as it eliminates the need for waste disposal such as land filling and incineration and reduces environment pollution. Collection and transportaion cost for biomass is considerable, hence feedstock needs to be sourced from the close vicinity only. There are also some challenges associated with biomass gasification like considerable variation in feedstock characteristics, stable supply of the feedstock in the close vicinity round the year which limits the biomass gasification plants in terms of capacity.
GASIFICATION PRODUCT OPTIONS
Downstream processing of gasification derived syngas makes it a versatile good fit in the scheme of things to produce a variety of end products from syngas (CO+H2) which can be conditioned/processed as required and used as feedstock for downstream units. Gasification gives a wide range of options of end products like Fischer-Tropsch (FT) fuels, SNG, methanol and derivatives, fertilisers, hydrogen, fuel gas, power, steam, syngas for DRI (Direct Reduction of Iron) etc. Figure 2 shows the various product options from gasification.
It can be noted that Feed Preparation, Gasification Island, Air Separation Unit, Shift & Syngas Cleaning, Low Temperature Gas Cooling (LTGC) and Syngas Cleaning are the common units in most of the process configurations to produce clean syngas which is further processed in downstream units to give end products. Oxygen is supplied from Air Separation Unit (ASU) to Gasification Island where raw syngas is generated from the feedstock, then raw syngas is split between Shift and LTGC to adjust H2/CO ratio as required for downstream units. Acid gases are removed from the syngas coming from Shift and LTGC units before it is delivered to the downstream units for further processing. Apart from the common process units, the highlighted unit blocks in these figures are the dedicated process units required to produce respective end products.
As it is mentioned in the earlier paragraphs, gasification uses ‘low value’ feedstocks to produce end products with added value. As it can be seen from these tables that fertiliser and chemicals have relatively higher value addition compared to SNG and other liquid fuels. This comparison along with demand/supply scenario of the market helps in narrowing down the product choices before proceeding with a feasibility study.
Gasification technology is not new to India, Fertilisers and Chemicals Travancore (FACT), Kochi operated a wood gasification plant to produce ammonia in 1940’s. Multiple ammonia/urea units based on fuel oil/Low Sulphur Heavy Stock (LSHS) gasification projects proceeded in late 1970’s and 1980’s. These fertiliser plants were in operation until they became unviable with the easy availability of natural gas from international market as well as domestic gas basin discoveries. So it is clear that India has shown no hesitation to embrace gasification as a technology and it was only on account of financial reasons that gasification could not extend its reach. It can be inferred from a qualitative SWOT (Strength, Weakness, Opportunity and Threat) analysis that today gasification is poised to occupy an important position in the long term strategic planning of India’s energy and petrochemical sectors. Concerns about energy security, financial market scenarios and emphasis on clean energy initiatives are the favorable factors for this inference. Also, gasification technology has evolved rapidly in last few decades and carbon conversion and efficiency limits are pushed as high as ever.
Housing more than 17 per cent of world population, India has only 0.4 per cent of the world reserves of oil and gas. Oil and gas contribute to 40 per cent of India’s primary energy demand out of which ~77 per cent is met by imports. In 2013-14, total crude oil imports of 189 MMT valued ~144 Billion USD while LNG imports accounted for 13 MMT worth 9 Billion USD.2 Energy security could be defined as availability of adequate and reliable energy resources at stable prices and is prime focus for India to have balance in geopolitical dynamics. The Indian Government is strategising to reduce oil imports to 67 per cent by 2022 and to 50 per cent by 2030.3 Oil, gas and coal form significant fraction of primary energy demand.
For gradual cut in oil/gas import bill, import substitution can be assisted through accelerated domestic gas exploration efforts and capacity addition in oil extraction avenues. But these efforts won’t be complete unless import substitution actually includes feedstock substitution. India has the fifth largest coal reserves in the world estimated to be ~302 billion tonnes.4 It would be a great boost for energy security if locally available coal can replace oil/gas feedstocks. Though coal in India has high ash content, it is relatively cheaper compared to international markets. Also, prices of domestic coal are determined by level of supply and demand and don’t show direct relation with crude oil price trend/ outlook so it is relatively unaffected from outer markets.
India is producing ~13 MMTPA petcoke and the production is expected to rise to 16 MMTPA with planned coker units. Coal/petcoke should be utilised in gasification to produce syngas which is alternate feedstock to imported oil/gas to produce liquid fuels, petrochemicals, fertilisers, power etc. On the other hand, coal has traditionally been used to produce power in Thermal Power Plants (TPP’s) but existing TPP’s are based on relatively less efficient combustion boiler technology. Integrated Gasification Combined Cycle (IGCC) plants where syngas generated from coal gasification is fed to gas turbines in a combined cycle and steam generated from syngas cooling and gas turbine exhaust heat recovery is used to run steam turbines is an ideal replacement for conventional direct coal fired boilers. Table 5 provides specific coal consumption in TPP’s for various technologies.
A Government of India Initiative, India Energy Security Scenarios 2047 states that as the energy demand in India will increase over the years, the potential of various alternative sources will be exploited and hydrogen fuel will emerge as a powerful and stable source of energy. Further projections state that assuming availability of basic resources in the country and commercial viability of the technologies, 95 per cent demand of the hydrogen fuel is fulfilled by coal gasification and 5 per cent by natural gas reforming. As such feedstock substitution, enhancing efficiencies of TPP’s or backing the newer hydrogen based fuel/ energy systems, gasification is going to play a key role in achieving India’s energy security in coming decades.
Gasification provides a relatively cleaner approach to generate power and/or end products. Gasifiers have very high carbon conversion (as high as > 98 per cent) from feedstock to syngas, also the scope for additional CO2 generation is limited to Shift unit. This ultimately reflects in high carbon conversion from gasifier feed to end products.