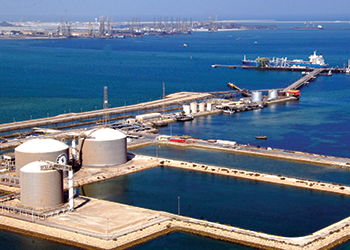
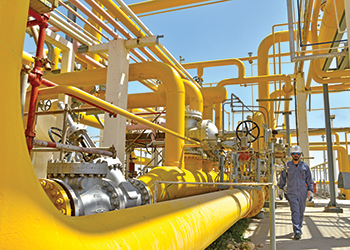
The company produces approximately 3000 bbls of propane, 3200 bbls of butane and 4500 bbls of naphtha per day for its own account as well as 2500 bbls of product from refinery off gas under a processing fee agreement with Bapco
Banagas operates LPG plant facilities to recover propane, butane and naphtha from associated gas (from oil wells) and refinery off gas. Liquefied propane and butane are transferred to refrigerated storage tanks located at the Sitra Wharf area for shiploading. Naphtha is sent to the Bahrain Petroleum Refinery (Bapco) for storage and subsequent export.
The residue gas is used as fuel for Banagas furnaces and gas turbines, and the rest is supplied to Aluminium Bahrain (Alba), Riffa Power Station and the Bapco Refinery. This residue gas, of about 250 million standard cubic feet per day (mmscfd), represents 25 per cent of Bahrain’s daily fuel gas consumption.
The original plant was commissioned in 1980 with capacity of 110 mmscfd of associated gas. At present Banagas operates two gas-processing trains with a total feed gas throughput of about 300 mmscfd.
BAHRAIN OIL FIELD
The low pressure associated gas is collected from 31 well manifolds in the Bahrain Oil Field. The gas is separated in gas oil separators (GOSPs) which are operated by Tatweer Petroleum, the Bahrain Field operator, at a controlled pressure of about 35 psig. The gas from the well manifolds is distributed to all seven compressor stations operated by Banagas. Additionally, low pressure non dehydrated Refinery Off gas is also supplied from Bapco refinery to compressor stations 6, 7 and 9 where it is compressed along with the associated gas and delivered to the central gas plant for LPG recovery.
Compressor stations: At each compressor station, gas from several GOSPs is gathered into an inlet header and compressed by two-stage centrifugal compressors driven by a gas turbine to about 420 psig. The gas is then cooled by air fans to about 110 deg F. During this process some of the gas is condensed and sent to Banagas’s Central Gas Plant (CGP) as condensate. The compressed gas however contains some water vapour and acidic gases like carbon dioxide and hydrogen sulphide.
The water vapour may condense in the pipe line due to natural cooling and the free water, together with hydrogen sulphide and carbon dioxide present in the associated gas stream, will form corrosive acid. To avoid this the compressed gas is dried in a glycol dehydration unit (GDU) located in each compressor station before being pumped through gas pipelines to the CGP.
Central gas plant: The plant was initially commissioned with a capacity of 110 mmscfd of associated gas. After a series of plant expansions, Banagas now operates two process Trains with a total gas throughput of 300 mmscfd. The two process trains are identical and use refrigerated lean oil-heavy naphtha to recover LPG from the feed gas. Each train consists of condensate, absorption, fractionation, treating and intermediate storage sections.
CONDENSATE SYSTEM
Stabiliser: Condensate from the compressor stations and from the gas separation system is distilled in a stabiliser column to remove light gas components such as methane and ethane. The stabilised condensate is fed to the depropaniser, while the light gases join the inlet gas.
Separation Section: The compressed gas, at 420 psia and a dew point of – 20 deg F, enter the separation section where liquids are removed. Any solid residue is separated and removed from the process by the filter separator.
GAS ABSORPTION SYSTEM
Dehydration: The gas leaving the separation section is dehydrated to a dew point of -45 deg F to prevent the formation of hydrates in the subzero absorption section. Triethylene glycol is used to absorb any water from the gas.
Absorber: In the absorber column the refrigerated feed gas and lean oil are intermingled at a temperature of minus 35 deg F to allow the lean oil to absorb the LPG products of propane and heavier components from the gas and become a rich oil. The residue gas leaves the absorber is used as fuel gas by Banagas as well as neighbouring industries.
The absorption of LPG is accelerated by high pressure and low temperature. Refrigeration of the feed gas and product streams is provided via a closed loop circulation of refrigerant propane using two gas turbine driven centrifugal compressors at each train.
FRACTIONATION SECTION
Deethaniser: The purpose of the deethaniser is to remove ethane and lighter components from the rich oil in order to maintain a maximum of 2 per cent ethane in propane. The overhead vapour is recycled to the absorber section to recover any escaped propane and heavier components. The deethaniser bottoms are fed to the rich oil still column.
Rich oil still column/hot oil system: In the rich oil still, lean oil is separated by distillation from the absorbed LPG products. These LPG products go overhead and are condensed by the rich oil still reflux condenser and then routed to the Fractionation columns. The liquid from the bottom of the rich oil still is circulated through the hot oil system as a source of heat for all the plant reboilers and part of it is used as absorbent lean oil. The hot oil temperature is maintained by a gas fired heater.
Depropaniser and debutaniser systems: The purpose of these systems is to separate the stabilized condensate and the absorbed LPG products into three marketable products: propane, butane and naphtha.
Depropaniser: The condensed LPG Product and the stabilised condensate are fed to the depropaniser column. A distillation process takes place where the light components of propane are separated and condensed in a reflux condenser prior to sending to the treating section.
Debutaniser: The lighter components of butane vapour are separated and condensed in a reflux condenser prior to sending to the treating section. The bottom liquid from this column is cooled and sent to intermediate storage as naphtha product.
Treating section: Propane and butane contain contaminants such as hydrogen sulphide, carbonyl sulphide and mercaptans. For the removal of carbonyl sulphide and mercaptans both propane and butane products are treated in a fluidised bed of solid potassium hydroxide (KOH). Prior to this, propane product is treated by diethanol amine solution to remove hydrogen sulphide.
Intermediate Storage Section: Treated propane and butane products are routed to horizontal tanks (bullets). After the product is circulated and analysed to confirm the product specification it is routed to spherical tanks located in the intermediate storage at the CGP. If any product fails to meet the required specification, it is returned to the gas plant to be reprocessed. Only " On-spec-products" are pumped via a 20 km pipeline from their respective spheres to the refrigerated storage tanks located at the Bapco Wharf area at Sitra.
A very small quantity of propane product is sold in the local market, which is loaded in pressurised trucks. Naphtha product is stored in floating roof tanks. "On-spec" naphtha product is pumped directly to the Bapco Refinery for storage and subsequent export.
REFRIGERATED STORAGE AND SHIPPING
Refrigerated storage: At Sitra, liquid propane from the Gas Plant is received into the surge drum at 356 psig and 120 deg F. Some of the propane is used as refrigerant, first in the butane chillers and then in the butane sub-coolers. During this process butane is cooled to +25 deg F and the liquid propane is flashed into vapour. The balance of the propane is flashed to its boiling point of -45 deg F into the propane storage tank.
The propane vapours from the storage tank, butane chillers and sub-coolers are compressed by reciprocating compressors.
The compressed vapours are condensed and used as refrigerated propane to cool down both propane and butane products to their atmospheric boiling point of -45 deg F and +23 deg F respectively.
Each product is stored at its boiling point in separate refrigerated tanks of 200,000 barrels capacity. A 100,000 barrel dual purpose storage tank to store either propane or butane product is also available.
Product Shipping: The LPG shipping facilities consist of two loading pumps each with a rated capacity of 5,000 bbls/hour, a 16" loading line and a 10" vapour return line, each of which is fitted with fully articulated arms.
Just before a ship’s arrival the loading line is cooled down with the product to be loaded. The vapour generated is returned to its respective tank. The loading and vapour return arms are then connected to the ship and loading commences at a low rate. As conditions in the loading system allow, the loading rate is increased up to a maximum of approximately 10,000 bbls/hour.
Most of the vessels take a dual cargo of propane and butane. With only one loading line, great care is taken to avoid contamination of the ships tanks when switching from propane to butane or vice versa.
The method of detecting the arrival of the second product at the ships rail is by closely monitoring the temperature difference, or ‘break’, between propane (-45 deg F) and butane (+23 deg F).