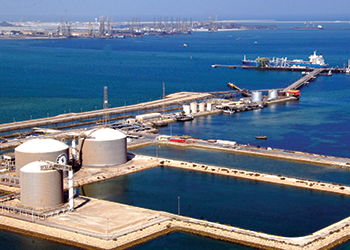
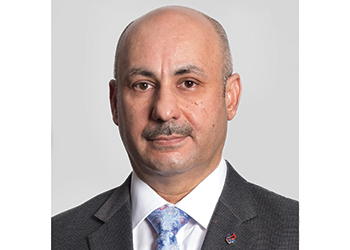
Tatweer’s Bahrainisation in 2016 is 4 per cent higher than 2015. Its headcount is now almost 677 employees, of which 79 per cent are Bahraini nationals, says Hisham Zubari, Deputy CEO of Tatweer Petroleum in an exclusive interview
Tatweer Petroleum has, over the past six years of operations, invested over $4 billion to redevelop the mature Bahrain Oil Field and to transform the field into a tertiary mode through the implementation of advanced enhanced oil recovery techniques and employing new technologies, says Hisham Zubari, Deputy CEO of Tatweer Petroleum.
This operation, which supports Tatweer’s vision to energise the kingdom’s economic growth and social prosperity, has significantly benefited local contractors by creating over 200 direct jobs in Tatweer and several hundred support services through external contractors, Zubari tells OGN In an exclusive interview.
Tatweer’s Bahrainisation in 2016 is 4 per cent higher than 2015. Its headcount is now almost 677 employees, of which 79 per cent are Bahraini nationals. The key matter here is to be able to identify suitable young Bahrainis who are willing to work in a challenging environment in specialised fields such as thermal recovery and digital oil field technology, which are relatively new to the Bahrain Field.
'Our success in reaching such a high Bahrainisation rate while maintaining the performance-driven culture we are proud of represents yet another contribution by Tatweer to the economic growth opportunities for the Kingdom of Bahrain,' he says.
Furthermore, a total of 10 Bahrainis were recently promoted to leadership positions or to higher level leadership positions in 2016. Additional leadership training will continue in 2017 to develop and better prepare Bahraini employees for more responsible future roles. It is worth mentioning that the Bahrainisation rate in leadership positions is currently 67 per cent, he says.
Excerpts from the interview:
How many hours of training do you plan to impart to the local workforce in 2017?
Tatweer launched the Individual Development Plan (IDP) programme for all and each of our employees as part of the company’s commitment to train and develop all eligible Bahraini employees in their respective fields of responsibility. With the IDP programme, Tatweer has been able to put in place personalised development plans for all Bahraini employees. The plan has already been implemented in 2016 and will continue in 2017, and the progress of each Bahraini employee will be tracked throughout the year to assure progress is made toward agreed competency targets.
Furthermore, we have kicked off two initiatives to expedite and enhance the training of young Bahrainis in specialised fields. The first is a competency assessment programme for Subsurface, whereby Subsurface Advisors at Tatweer developed a competency framework to assess Bahraini Geologists and Reservoir Engineers. Through this model, the Advisors were able to identify the skill and competency gaps more efficiently as well as provide customised functional training and professional development, to address the identified competence gaps. The second is a technical competency assessment programme for steam operators, which has been developed to accelerate the development of Bahraini Operators. The National Vocational Qualification (NVQ) framework has been adapted to assess the Operator’s knowledge and skills in the job.
How many local contractors have benefited from Tatweer?
Currently Tatweer runs its business through over 1,000 contracts. 63 per cent of all contracts and purchases were awarded to Bahraini companies in 2016, which is approximately 20 per cent of this committed spend. Excluding services that can only be provided by companies outside Bahrain, the value of normalised award to Bahraini companies is 83 per cent.
What are Tatweer’s HSE goals and how they are going to be met?
We are proud to state that in 2016, Tatweer employees managed to achieve a zero (0) Incident and Illness Rate (IIR) for the first time since the company’s inception. This is a great achievement given the nature of our business and we are determined to maintain this rate in the future.
Tatweer aims to provide a safe and injury free work place for its employees and contractors, and strives to continuously enhance its HSE programmes and initiatives to prevent and mitigate incidents involving people and the environment.
Considerable efforts and resources are always focused on improving HSE practices in the Bahrain Oil Field. The HSE Management Walk-Through programme, which was launched in 2015 and involved managers and Executive Management team members in planned visits to key facilities, was continued in 2016 and involved a total of 15 visits to various facilities.
As part of ensuring HSE competency for Tatweer personnel and contractors, 84 class room training of 608 sessions were organised, including:
![]() |
An employee at work in one of Tatweer’s projects |
• Permit to work and Job Safety Analysis;
• Lock out / Tag out;
• Hazard Recognition and communication;
• H2S Awareness and SCBA Donning;
• Authorised gas testing; and
• Basic firefighting and First Aid training.
The Personnel Protective Equipment (PPE) procedure was revised and strictly enforced in the Field. New procedures have been introduced and the procurement of PPE has been automated to make sure supply is managed more effectively. HSE leadership assessment and training was conducted for both Tatweer management and staff to further enhance the safety culture in the company. This initiative will continue throughout 2017.
Tatweer Petroleum sponsored HSE campaigns in 2016 related to dropped object prevention, heat stress prevention, and Hunt the Hazard to improve employees’ and contractors’ hazard awareness in our operations. These and other programme improvements and topics were added to the Contractor HSE Forums to improve communication between Tatweer and its contractors. Other HSE Health related campaigns were also promoted including a Blood Donation drive, Breast Cancer Awareness, and the Stop Smoking campaign.
How many work hours have been achieved at the site? How many man-hours have been clocked without lost time accident (LTA) for contractors?
Tatweer and its contractors worked more than 7.2 million man-hours in 2016 and a combined 2.2 million man hours without LTI were achieved.
For the first time since Tatweer’s inception, Tatweer employees were able to achieve a full year without any lost time injuries (LTI), and accomplished an Injury and Illness Rate (IIR) of 0.
What are the risk reduction measures being implemented?
Tatweer Petroleum’s Risk Management System (TRM) was built based on an integrated approach that incorporated the identification and assessment of risks.
In 2015, Tatweer engaged its employees across the company in a process to identify a number of risk statements which were assessed by the concerned professionals in the company. This exercise was further enhanced in 2016, whereby each risk was assigned to a risk owner responsible for overseeing the implementation of the mitigation plans.
The TRM Committee, headed by the CEO, reviews and approves the company’s risk register, examines emerging risks and their quantification, and provides direction on the prioritisation of risk mitigation and business continuity plans.
In 2016, the TRM Coordination team facilitated 28 workshops to address each risk separately and to come up with mitigation plans. The team also facilitated a 'what- if' workshop to identify potential catastrophic scenarios based on a combination of events that were used to update the risk register.
![]() |
Geographic Information System (GIS) technology has been in |
The HSE Department also conducts HSE self-assessments to verify the effectiveness of HSE implementation in its operations. The results confirmed good progress in implementing recommendations from previous reviews and audits and the focus continued to be on identifying and managing the high-risk areas through enforcement of a Process Risk Management (PRM) Programme.
Could you explain how JSA (Job Safety Analysis) works in Tatweer?
The safety of our employees is absolutely the highest priority for Tatweer. JSA is a careful evaluation of the potential hazards associated with a task in order to determine the efforts required to make the work safe. It is used to identify the potential hazards, ensures that all safeguards are available, and provides an opportunity to remove hazards prior to employees and/or contractors starting a task. A strict workflow is established and then followed to complete the analysis.
Could you furnish details of the Near-Miss reporting programme? How did its last phase go?
With a strong commitment to safety, Tatweer employees contributed to a successful Near-Miss reporting programme. A rate of seven reports per person, totalling 3,285 reports in 2016, was 17 per cent higher than the set target of six reports per person.
What were the awards/recognitions received by Tatweer in 2016?
In 2016, Tatweer won the MEED Quality Award for National Upstream Oil & Gas Project of the Year. The award was presented to Tatweer Petroleum for their Light Oil Steam Flood project, which maintained a high standard of work, adherence to budget and client satisfaction in a healthy and safe working environment.
Furthermore, we were shortlisted for the Adipec awards’ 'Best Oil and Gas Innovation or Technology (upstream)' category for the same project.
We attribute our success to the full support and encouragement that we continue to receive from His Majesty King Hamad bin Isa Al Khalifa, HRH the Prime Minister Prince Khalifa bin Salman Al Khalifa, and HRH the Crown Prince and Deputy Supreme Commander Prince Salman bin Hamad Al Khalifa. Additionally, Tatweer is thankful to Shaikh Mohamed bin Khalifa Al Khalifa, Minister of Oil, and Dr Dafer Al Jalahma, Acting nogaholding CEO, who continue to offer their guidance and support.
We also strengthened our engagement with our stakeholders such as the Southern governorate Office headed by Shaikh Abdulla bin Rashid Al Khalifa, who has been a great supporter to Tatweer’s safe camping concerns, the National Guard headed by Shaikh Abdul Aziz bin Saud Al Khalifa, the Traffic Directorate headed by Shaikh Nasser bin Abdul Rahman Al Khalifa, and the Bahrain Health and Safety Society headed by Dr Mustafa AlSayed. We will continue to work very closely with our stakeholders to achieve a mutual cooperation and collaborations on all levels for the best interest of the Kingdom of Bahrain.
How does Tatweer honour its commitment to responsible environmental stewardship?
Tatweer is committed to the conservation of the kingdom’s natural resources and the protection of the environment. The company installed a 1 Megawatt solar power plant which is capable of supplying around 1-2 per cent of Tatweer’s present power consumption. Solar energy panels connect to Tatweer’s own power grid to deliver enough power for the autonomy of its headquarters building. During weekends and times of low use of the Tatweer Headquarters, excess power is fed back into the Tatweer power grid for use elsewhere in oil field operations. This reduces and conserves the gas consumption burned for fuel in the power stations as well as reduces emissions. Following the success and economic feasibility of the solar farm, we have made plans to construct a 5 Megawatt solar power plant in 2018.
Tatweer Petroleum has also installed and now operates 8 water treatment plants that treat all its produced water to remove oil and solids before re-injecting the same into oil reservoirs for pressure maintenance. Furthermore, Tatweer has modernised and improved air emissions and waste management by deploying world class programmes with world class standards.
With Health, Safety and Environment as one of its core company values, Tatweer Petroleum strives to provide a safe workplace and is committed to the protection of the environment. Campaigns, initiatives and bulletins are put in place every year to address industry trends and safety risks. Tatweer continues to safeguard the kingdom’s resources minimising the operations impact on the environment while maximising the value it is returning to the kingdom.
How did Tatweer’s Supply Chain Management team perform in 2016?
During 2016, Supply Chain Management (SCM) continued to identify and achieve reductions across key contracts. These continued efforts supported the overall savings made by the company throughout the year. The SCM Inventory Reduction KPI, which was set at 10 per cent for each relevant Tatweer department, continued to support the reduction in Inventory and identified $13.85 million worth of inventory items that could be utilised on new projects instead of purchasing new parts.
SCM also championed a cost reduction campaign that resulted in savings of over $10 million in 2016-17.
Additionally, by the end of 2016, the SCM Warehouse completed 583,703 man-hours without an LTI.
What are the key features of the Geographic Information System (GIS) technology component in Tatweer’s management?
Geographic Information System (GIS) technology has been in use at Tatweer Petroleum since 2009. GIS implementation has always been a key component of a management strategic initiative to drive safety and efficiency in the company’s operations and assets management and protection.
Today, GIS solutions can be found in use within various business processes in Tatweer. The solutions include standalone applications for spatial analysis and decision-making as well as integrated GIS enhancing utilities added to existing applications. Given the geographic dispersion of our operations and the diminishing proximity of urban areas around Tatweer’s operation, the use of GIS based solutions have played a critical role in helping to maintain not only an efficient and effective production operation but also a safe one.
During 2016, the GIS application development team continued to work closely with Tatweer’s other departments in order to explore new opportunities and enhance existing GIS applications. Manifold Tie-ins Reservation, Oil Leak Tracking and Registering Permit to Works are example of new GIS opportunities realised.
Our team created two in-house tools to help with enhancing oil production; a real-time system that shows wells that need immediate attention, and a tool, called Tarteeb, to help engineers understand behaviour of wells on artificial lifting mode.
The GIS Team also successfully upgraded its GIS data infrastructure when it successfully completed a field-wide topographic survey, designed to enhance the GIS accuracy, and revised the pipeline data classification and categorisation for the pipelines network, resulting in enhancement of the GIS user experience.