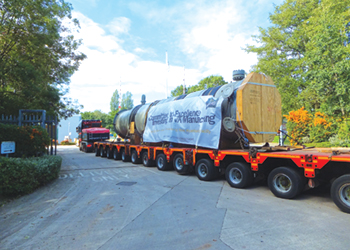
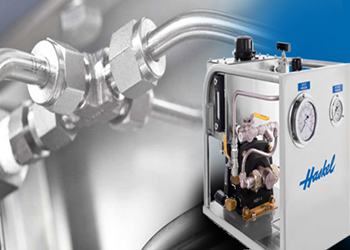
Haskel has developed a new technology that creates precompressive stress along the pressure vessel wall, eliminating the risk of leaks or ruptures due to HEE. Haskel’s technology shows great promise for the H -transport and pump industry
To mitigate the risk of hydrogen (H) embrittlement in high-cycle compressors and high-pressure storage, Haskel engineers developed a new technology that creates pre-compressive stress along the pressure vessel wall, eliminating the risk of leaks or ruptures due to H embrittlement.
A technical paper discussing the development of this technology was presented at ASME’s 2018 International Mechanical Engineering Congress & Exposition (IMECE). The details of the paper are as follows:
High-cycle compressors and other forms of high-pressure storage and transport of H are becoming increasingly common. A major concern for the advancement of this technology is the H embrittlement effect (HEE).
HEE weakens the integrity of the vessel walls and shortens the fatigue life. Haskel has developed a new technology that creates precompressive stress along the pressure vessel wall, eliminating the risk of leaks or ruptures due to HEE. Haskel’s technology shows great promise for the H -transport and pump industry and has led to a revision of the 2017 ASME Pressure Vessel code.
The increased use of H fuel cells as an energy source for cars and power plants has brought innovation and market expansion, but it has also caused an increase in concerns about the safety of H compression, transport, and storage. The past several years has seen regulatory agencies impose stricter rules for construction of pressure vessels and compressors in H service to mitigate the safety risks. A particular concern is the H embrittlement effect (HEE).
WHAT IS H EMBRITTLEMENT?
H embrittlement is the process in which H introduced into a metallic component causes its structure to crack. At the metallic surface, H molecules dissociate into atomic H .H atoms are unstable and will re-associate immediately to molecular form if they enter a void in the metallic structures. Such voids exist as material defects caused by pre-manufacturing processes. The re-associated molecular H in the cracks is more stable and occupies a larger volume. As a result, the molecule pushes against the crack walls to further open it, making more room for subsequent H re-associations. This process increases the crack growth rate, which shortens the fatigue life of the pressure vessel.
Haskel has developed a method for mitigating HEE that involves tting a liner within the jacket of the high-pressure vessel. The liner has an outer diameter that is slightly larger than the jacket’s inner diameter. The process involves three steps:
Align elements: Place the interior liner at the opening of the vessel jacket with the centre-axes aligned. Heat-Stretch-Insert: Heat the vessel jacket, which expands its inner diameter. This allows the cold liner to t within the jacket. Cool: When the assembly returns to an equilibrium temperature, the jacket’s inner diameter decreases. The resultant stress at the boundary of the liner and the jacket creates compression on the liner. The compressive stress generated by the jacket upon the inner liner prevents any cracks within the vessel walls from opening and expanding further. This procedure mitigates the risk of HEE by eliminating all voids in the pressure vessel wall.
Key results
Extensive simulation of the shrink-t liner concept yielded four principal results:
1. Keeping all the existing cracks closed prevented any chance of HEE.
2. The process successfully compensated for fatigue caused by defects created during the material-manufacturing process (e.g. annealing, heat treatment, cold drawing, etc.)
3. Fracture mechanics analysis demonstrated an effectively long fatigue life.
4. The shrink-t process enables innovation by relaxing specications and manufacturing costs for H service vessels and compressors.
Conclusion
The method of construction has proved valuable. Relaxing materials specications for H service vessels and gas boosters is enabling innovation in the H fuel cell industry. The 2017 ASME Pressure Vessel code was revised to allow the use of shrink-t liners in the design of H vessels.
This technology is currently a pending patent by Haskel International.
With over 70 years of unrivalled expertise in high-pressure, liquid and gas transfer and pressurisation technology, Haskel is the solution provider for applications in aviation, defence and aerospace, oil and gas.