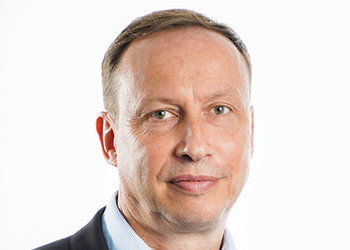
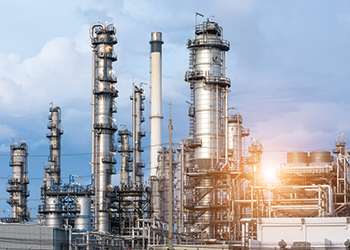
Sulzer GTC’s GT-BTX separation technology enhances processing of aromatic streams leading to improved recovery levels and increased purity, says the company
Refineries and petrochemical complexes can maximise their margins and competitiveness by leveraging aromatics byproducts, such as benzene, toluene and xylene (BTX).
When setting up recovery and production lines for these aromatics, businesses can benefit from Sulzer GTC’s GT-BTX technology. By selecting this solution for new or existing facilities, companies in the oil and gas sector can intensify their operations, improve their recovery levels from aromatic streams and increase the purity achieved.
The market for consumables used in industrial chemical processes is steadily growing and larger volumes of aromatics are required to support this expansion. As the building blocks to all aromatic derivatives, the global demand for BTX is also increasing. To serve this market with reliable supplies, forward-looking refineries and petrochemical complexes are investing in new or revamped BTX units.
![]() |
When doing so, businesses need to implement separation equipment that can recover BTX with high purity levels, so that the substances will be accepted by polymer, solvent or additive manufacturers.
High BTX recoveries can be very energy intensive, especially if conducted via liquid-liquid extraction or azeotropic distillation. This can, in turn, compromise any effort to increase profitability or assure a quick return on investment (ROI). However, there are separation techniques that can support businesses make BTX recovery economically sustainable.
In high-purity BTX recovery applications, extractive distillation has proven more effective. This is a vapour-liquid extraction that relies on the addition of a third component – a solvent – to the hydrocarbon feedstock to change the corrected partial vapour pressure, known as relative volatility, of one or more constituents. In this way, the extra chemical promotes the separation between different substances.
Extractive distillation is to be favoured over other alternatives for a number of reasons. The overall mass transfer is generally considerably higher than in azeotropic distillation units with comparable size and footprint.
When compared to liquid-liquid extraction, extractive distillation minimises the risk of fouling within columns and their internals. It also requires considerably lower solvent volumes and less equipment. In effect, only two distillation columns are required, rather than one extraction column with a downstream distillation unit.
![]() |
Overall, by adopting extractive distillation systems, businesses can reduce capital costs by 30-40 per cent and benefit from 20-30 per cent lower energy consumption.
An example employing this extraction method is Sulzer GTC’s GT-BTX licensed technology. The setup utilises two columns and advanced solvents to recover BTX from refinery, petrochemical or coke oven aromatics streams, such as catalytic reformate, pyrolysis gasoline or coke oven light oil (COLO).
During the GT-BTX process, the hydrocarbon feedstock is first preheated with hot circulating solvent. The mixture then goes through an extractive distillation column, where it is separated into raffinate (non-aromatic hydrocarbon) and aromatics-rich solvents. Finally, the aromatic compounds are stripped in a solvent recovery column and routed to the purification section, in order to fractionate them and produce chemical-grade BTX.
As a result, Sulzer GTC’s GT-BTX technology can help refineries benefit from cutting-edge aromatics separation performance while reducing both capital expenditure (capex) and operating expenses (opex). By using this technology, it is possible to produce larger volumes of higher purity aromatics in a more efficient way. This means that businesses can increase productivity as well as recover non-aromatics that can be used in subsequent processes, optimizing resource utilisation.
UNRIVALLED SOLVENTS OF SEPARATION CHALLENGES
While extractive distillation offers clear advantages, there is a great variability in the processes available, resulting from column design and solvent selection. Therefore, refineries and petrochemical complexes should select mass transfer specialists that can deliver optimal results in both fields.
Sulzer GTC Technology can provide support to its customers in the oil and gas industry by delivering high-quality columns and internals as well as selecting the most suitable solvents. The synergies between this group and Sulzer Chemtech’s teams lead to enhanced mass transfer capabilities in licensing process-based plant engineering and technologies.
In this context, the elevated level of expertise has led to the development of state-of-the-art combinations of solvents, known as Techtiv solvent, that substantially enhance extraction performance in GT-BTX units. In addition, they support the optimisation of the facility itself, in terms of stability and mass transfer efficiency.
Furthermore, these co-solvents allow refineries to avoid special feed preparations and handle a wide range of BTX feedstock while delivering substances with purity levels of 99.99 per cent wt. per cent or more at high recoveries rates (99.9 per cent or higher).
SINGLE POINT OF CONTACT FOR TOWER SERVICES
Finally, refineries should choose full-service providers for aromatics recovery projects. By selecting a mass transfer specialist that can provide turnkey projects, installation and start-up activities can be streamlined and the number of subcontractors can be reduced.
By offering complete project support, Sulzer GTC is able to help businesses benefit from GT-BTX units as quickly and efficiently as possible.
Furthermore, the company’s Tower Field Services division can carry out planned and emergency repairs, design and implement upgrades on equipment from multiple vendors. In this way, it ultimately delivers continuous support in a timely manner, minimising equipment downtime and optimizing its performance.
CASE STUDY: GT-BTX FOR REVAMPS
GT-BTX technology is supporting the revamp of a benzene production unit at a leading integrated petrochemical complex specializing in olefins in Eastern Europe.
By leveraging advanced aromatics recovery solutions, the project will turn the facility into one of the most modern of its kind and allow it to act as a hub for processing pyrolysis gasoline (pygas) from multiple locations.
Thanks to this revamp, the plant will be able to produce higher purity benzene and more efficiently, increase product quality while reducing production costs.
In addition, the facility will be able to recover non-aromatics for subsequent processing, thereby increasing overall in-house capabilities. Furthermore, the higher processing capacity will allow the petrochemical complex to gather full range pygas from various facilities for downstream activities.