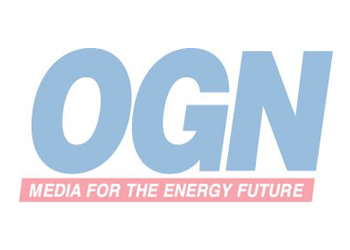
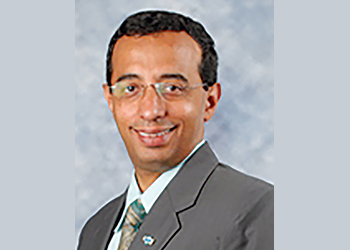
Designing valve automation strategies to the entire spectrum of terminal applications improve safety, increase reliability and add greater visibility on valve assets and their conditions, Bill Dumasia, Business Development Manager MEA, Emerson, tells OGN
Storage terminals play a critical role in the movement of hydrocarbon-related products throughout their supply chains. As large tanks are designed to handle hazardous and flammable fluids, safety is the paramount concern for operators. The role of valves is, therefore, of paramount importance.
Terminal business is around its capacity, and the global storage terminal market size is projected to reach around $37 billion by 2027, making this a high-risk industry.
![]() |
Emerson offers a comprehensive line-up for terminal valvue safety |
According to Bill Dumasia, Business Development Manager MEA, Emerson, facility managers understand the need for increased capacity, as well as how safety plays a vital role in their work. Minimising these risks can affect the overall oil and gas supply chain.
"Facility managers are focused on three goals: reduce safety risk, increase their shell capacity, and reduce costs. Over the years, terminals have transformed into complex facilities, handling a wide range of liquid products – more than what they have previously controlled."
Valves now are expected to constantly change positions and require visibility for the operator to avoid cross-contaminations and potential incidents. For safe and reliable terminal operations, managers understand that it is important to be aware of the location of all products and their needed movements. However, the standard way of automating valves is a high-cost process.
As most of these dated facilities only have manual valves, technicians have a lot of work on their hands especially without any kind of feedback coming from these kinds of valves. They need to make sure that they are all in an appropriate position to be able to move the products through the storage terminal.
Without clear visibility into the real-time health and operational status of the assets required for movements within their facility, problems can occur for the users.
One operational risk is in the line-up of manual and automatic valves. Improper positions can result in unsafe conditions, unintended movements, or other operational issues. Line-up mistakes are time consuming and expensive to correct, and can lead to delayed in product transfer, and lead to costs around decontamination and clean-up activities.
Also, although the risks are well understood, the available solutions are not practical in legacy terminals where additional automation can be restricted by capacity limitations in existing control systems.
Emerson’s innovations around remote valve monitoring through Wireless HART’s reliable technology enables terminal operators to view valve position and verify accurate line-up without having to mobilise technicians to the field. This has proven to be the lowest cost monitoring solution that doesn’t require cabling or additional space in the control system. Further, the use of electric actuators with field mounted master stations allows operators to remotely drive manifold line-ups. These master stations can be placed in a safe area and this also significantly reduces mobilisation-based safety risks.
In ensuring terminal safety, Emerson recognises the challenges that users face and have several solutions and technologies to help in supporting their needs and goals. One example is in the improvement of storage tank protection from overfill and over-pressure risks.
High performance relief valves helps create an emergency protection loop that help protect critical tank assets during abnormal conditions where tank pressure exceeds design limits. Depending on terminal design, these valves are expected to perform in extreme conditions and may involve sticky applications.
Overfill protection is a well-known safety application in the terminals industry. However, the focus has frequently been on improving the reliability and accuracy of level measurement.
While extremely important, this measurement is a part of a certified SIL – 2 (Safety Integrated Level - 2) loop that consists of the measurement, the safety logic and a ESD valve that closes inlet lines during emergencies.
Several operating terminals still deploy traditional motor operated valves (MOV’s) for this application, which is a sub-optimal solution, since it cannot provide valve operation during power failure and needs to depend on battery backup.
Emerson provides an elegant solution for this with its electric fail-safe solution, which provides spring backup to achieve valve closure, and greatly contributes to the overall safety of this application. All these solutions improve safety, increase terminal reliability and add greater visibility on valve assets and their conditions, and this provides operators with a greater level of control on terminal performance.