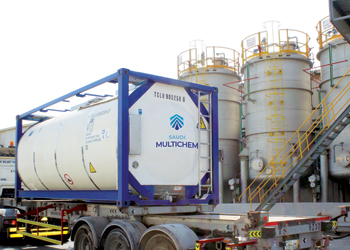
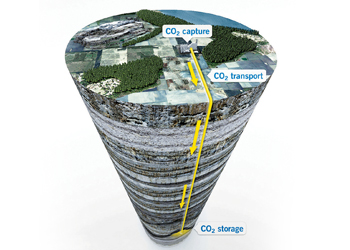
The global CCS industry must grow exponentially by 2050 to achieve the Paris Agreement targets. This means building 70-100 facilities a year at a total investment between $655 billion and $1,280 billion, says a report by Global CCS Institute
The carbon capture and storage project pipeline is growing more robustly than ever. From 75 million tonnes a year (Mtpa) at the end of 2020, the capacity of projects in development grew to 111 Mtpa in September 2021 – a 48 per cent increase.
A recent report, 'The Global Status of CCS: 2021', by Global CCS Institute, says the CCS project pipeline mirrors climate ambition, growing steadily since the 2015 Paris Agreement.
![]() |
Offshore transport and storage of CO2 |
Civil society’s calls for governments and the private sector to align their policies and practices with climate stabilisation have grown in number and volume, especially since the Intergovernmental Panel on Climate Change’s (IPCC’s) special report in 2018.
Four pathways show how global anthropogenic emissions must change through this century to achieve a 1.5 deg C climate outcome. All require a rapid decrease in emissions to net zero by 2060.
The IPCC also estimated that 5-10 gigatonnes (Gt) of carbon dioxide (CO2) must be removed from the atmosphere each year in the second half of this century to:
• Offset residual emissions that are very difficult to avoid, such as those from agriculture and air travel.
• Reduce the total load of greenhouse gases in the atmosphere to below the carbon budget for 1.5 deg C of global warming.
The International Energy Agency (IEA) reports that, by late April 2021, 44 countries and the EU had announced net zero emissions targets. These commitments cover approximately 70 per cent of global CO2 emissions.
The Climate Ambition Alliance, which brings together countries, regions, cities, businesses and investors to work towards achieving net zero emissions by 2050, has almost 4,000 participants, including over 2,300 companies and 700 cities.
The leaders of these organisations have pledged to reach net zero emissions by mid-century.
It is no coincidence that recent growth in net zero commitments has been accompanied by an unprecedented spike in CCS activity.
When organisations consider adopting net zero, they commonly do an analysis where they catalogue emissions, identify mitigation options for each, and then rank them for cost and efficacy. CCS often emerges as an essential part of the lowest cost pathway to net zero.
There is an increasing recognition by governments of CCS’s critical role. It now appears in 24 of 291 long-term Low Emissions and Development Strategies (LEDS) submitted under Article 4 of the Paris Agreement, as national governments decide how they’ll deliver their abatement commitments.
CCS is one of many climate mitigating technologies – commercially available and absolutely necessary to achieve a stable climate.
ECONOMIC & SOCIAL VALUE OF CCS
![]() |
Onshore transport can be done through gas-phase CO2 pipelines |
Emissions-intense industries often develop in clusters due to the availability of feedstocks; access to infrastructure, such as ports and rail; the presence of a skilled workforce; and a critical mass of specialist suppliers of engineering and other goods and services.
Many local communities rely upon a cluster like this for a large proportion of their employment and local economy. They would suffer severe economic and social dislocation if their emissions intense industries were shut down.
CCS can help transform high emissions-intensity industries to near-zero emissions industries – continuing support for economic prosperity, but also helping achieve climate imperatives.
Put simply, CCS protects jobs in industries and communities.
It is one of the reasons why networks centred on existing industrial precincts are emerging as a preferred model for CCS development.
CCS also creates new high value jobs. CCS facilities begin as large engineering and construction projects that take years to plan, design, construct and commission. They require a significant development and construction workforce.
At its peak, the Boundary Dam CCS facility in Canada employed a construction workforce of 1,700. Similarly, up to 2,000 people helped build the Alberta Carbon Trunk Line. Ongoing jobs are then created to run and maintain the CCS facilities.
The global CCS industry must grow by more than a factor of 100 by the year 2050, to achieve the Paris Agreement climate targets.
This means building 70 to 100 facilities a year, up to 100,000 construction jobs and ongoing jobs for 30,000 to 40,000 operators and maintainers. Between $655 billion and $1,280 billion in capital investment is needed until 2050.
The size of the global CCS industry could approach that of the world natural gas industry within a few decades creating a significant engine of growth, alongside renewable energy, in the new low emissions economy.
Despite unprecedented growth in the CCS project pipeline for the last 12 months, there remains a massive gap between today’s CCS fleet and what is required to reduce global anthropogenic emissions to net zero.
Limiting global warming to 2 deg C requires installed CCS capacity to increase from around 40 Mtpa today to over 5,600 Mtpa by 2050.
The figure may appear daunting but investing around $1 trillion over almost 30 years is well within the capacity of the private sector.
As proof, in 2018, the sector invested approximately $1.85 trillion in just the energy sector.
![]() |
The process of injecting CO2 into existing oil fields is a well-known enhanced |
In addition to enormous financial resources, the private sector has the expertise and experience to develop projects.
More private investors now want CCS in their portfolios. There is increased interest in CCS as part of a broad suite of technologies and strategies that can help achieve net zero emissions solutions at the lowest possible risk and cost. Without CCS, net zero is practically impossible.
Furthermore, rapid growth of supporting infrastructure is required by 2030 to bring more projects into the development pipeline and get them operating by 2050.
Faster rates of CCS facility development demand additional CO2 transport and storage facilities.
North America’s CO2 transport pipeline network is estimated to need to grow from around 8,000 km today to 43,000 km by 2050. This scale is definitely achievable, being only slightly larger than Australia’s natural gas transmission network, which has over 39,000 km of pipelines.
A CCS network requires geological storage for CO2. Identifying and characterising a storage resource requires tens to hundreds of millions of investment dollars. All funds are at risk as there is no guarantee of success.
GLOBAL CCS FACILITIES UPDATE & TRENDS
There are 135 commercial CCS facilities in the pipeline in the Global CCS Institute’s database. In the first nine months of 2021, 71 projects were added.
The US again leads the global league table, hosting 36 of the added facilities. Other leading countries are Belgium with four, the Netherlands with five and the UK, eight.
The large increase in commercial CCS facilities in H1 2021, has led to project pipeline capacity levels not seen since 2011 – 149.3 Mtpa. The project pipeline capacity annual average growth rate since 2017 has been 30 per cent.
Most growth so far in 2021 was in early development (25.9 Mtpa) and advanced development projects (9.0 Mtpa).
As new projects are announced and developed, the range in the scale of facilities is becoming broader.
Individual capture plants are larger, with facilities like Shell’s Rotterdam hydrogen project developing in the megatonne range.
At the same time, networks like the US's Summit Carbon Solutions are making smaller capture viable; their smallest capture plant has a capacity of just 90,000 tonnes a year. Capacities this small would be difficult to justify without supporting network infrastructure.
The recently approved Norcem Brevik project, part of the Langskip network in Norway, has CCS expanding into a new sector – cement manufacturing.
As a significant global emitter with limited decarbonisation options, the cement sector’s use of CCS is an essential step towards net zero.
The Norcem project is expected to provide valuable CCS learning and insights.
THE RISE OF CCS NETWORKS
Historically, CCS projects tended to be vertically integrated, with a capture plant having its own dedicated downstream transport system.
This favoured large-scale projects, where economies of scale made downstream costs reasonable.
Recently, there has been a trend toward projects sharing CO2 transport and storage infrastructure: pipelines, shipping, port facilities, and storage wells.
These CCS networks mean smaller projects can also benefit from economies of scale.
The Porthos network in Rotterdam entered advanced development early in 2021. A shared pipeline will transport liquid CO2 from four new blue hydrogen projects – Air Products, Air Liquide, ExxonMobil and Shell – under development in the Port of Rotterdam region, to storage about 20 km offshore, beneath the North Sea. The Netherlands Government committed €2.1 billion ($2.38 billion) in grants to these four projects in support of this network.
Also in Rotterdam, TotalEnergies and Shell have partnered to develop the Aramis CCS Network; a world-scale network with a proposed capacity in excess of 20 Mtpa.
The project in early development proposes storage in the Rotliegendes Sandstones Formation beneath the North Sea at 3–4km depth.
Transport modes will be mixed: a combination of liquefied CO2 transported by barges, gas-phase CO2 by onshore pipelines, and dense-phase CO2 by offshore pipeline.
It is expected to receive CO2 from a range of hard-to-abate sectors such as waste to energy (WtE), steel, chemicals, oil refineries and cement.
When the Norcem Brevik cement plant in Norway was funded by the Norwegian government in late 2020, the Langskip CCS network also took a step forward.
Norcem Brevik will capture and liquefy 400,000 tonnes of CO2 a year which will be transported by ship to the Naturgassparken, then offloaded and pumped via pipeline to offshore storage beneath the North Sea.
The other capture project in this network – the Fortum Oslo Varme waste-to-energy capture project is in advanced development and also expected to capture and liquefy 400,000 tonnes of CO2 a year.
Langskip CCS network has been designed for an initial 1.5 Mtpa of storage (in one well) with plans for 5 Mtpa (multiple wells) in phase two.
Summit Carbon Solutions network, under development, is emerging as the world largest negative emissions network, with planned CO2 capture capacity of 7.9 million tonnes a year.
Supporting 31 separate bioethanol plants, it leverages the twin economies of low-cost capture (corn fermentation CO2 is high purity) and aggregation of CO2 streams, reducing transport and storage costs.
In recent years, the UK has seen considerable development over multiple regions. These include the Humber Zero network and the nearby Zero Carbon Humber and net zero Teesside networks – the latter two recently combining as the East Coast Cluster.
All are based in areas with heavy industry – including oil refineries, power stations and natural gas processing plants – with reasonable proximity to offshore storage.
CCS IN THE GCC REGION
The significance of the GCC region in the context of CCS deployment is often overlooked, both in terms of current scale and short-term prospects.
Three facilities in the UAE and Saudi Arabia already account for 10 per cent of global CO2 captured each year, about 3.7 Mtpa. Europe accounts for just four per cent.
The GCC region is poised for a significant take-off in CCS activity over the next decade.
If efforts to deploy CCS intensify as trends suggest, CO2 capture might reach 60 Mtpa by 2035 across the GCC region.
In late 2020, the leaders of the G20 endorsed the concept of the ‘circular carbon economy’ developed by Saudi Arabia’s King Abdullah Petroleum Studies and Research Center, which recognises and values all forms of CO2 mitigation.
The concentration of CO2 emission sources in the GCC region is also conducive to CCS.
More of 2025’s estimated CO2 emissions will come from power generation, rather than oil and gas operations, in four of five countries.
As well as reducing the number of CCS facilities needed to decarbonise industry, the geographical concentration of major emitters along the Gulf coast could support the building of CO2 infrastructure networks, reducing overall costs and providing incentives for new CCS projects.
CCS project activity is spread across Qatar, Saudi Arabia and the UAE (more specifically in Abu Dhabi). Around 3.7 Mtpa of CO2 is captured at three CCS facilities:
• Qatar Gas captures 2.1 Mtpa of CO2 from the Ras Laffan gas liquefaction plant.
• Saudi Aramco captures 0.8 Mtpa of CO2 at its Hawiyah Naturals Gas Liquids plant. The CO2 is used to demonstrate the viability of EOR at the Uthmaniyah oil field.
• In Phase I (of at least three phases) of Adnoc’s Al Reyadah project, 0.8 Mtpa of CO2 is captured at the Emirates Steel plant in Abu Dhabi.
Both the Ras Laffan and Al Reyadah projects are already developing expansion plans:
• Qatar Gas expects to expand its capture rate to 5 Mtpa by 2025.
• Adnoc estimates that Phase II of Al Reyadah could see capture of another 2.3 Mtpa of CO2 by 2025 and Phase III could add a further 2 Mtpa of CO2 from the Habshan and Bab gas processing facility by 2030.
Even without further CCS activity, these projects could raise overall regional CO2 capture to almost 10 Mtpa by 2030.
There are two regional CO2 utilisation facilities where permanence of storage is not assured:
• Saudi Basic Industries Corporation (SABIC) captures 0.5 Mtpa of CO2 at its Jubail ethylene facility for use in methanol and urea production.
• Qatar Fuel Additive Company captures 0.2 Mtpa of CO2 at its methanol refinery.
It is widely anticipated that planned new coal generation plants in Oman and the UAE be built with CCS to complement NDC ambitions. This could add another 5–10 Mtpa to the regional CO2 capture rate, taking it to 15–20 Mtpa even before any heavy industry CCS plans are added.