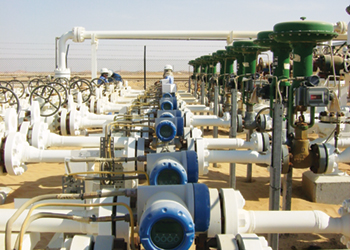
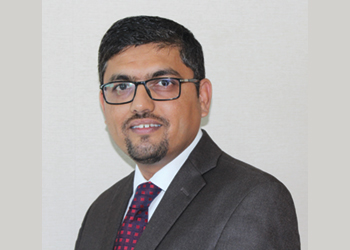
The company offered an end-to-end solution and employed its technology to enable the operator to save energy without compromising on performance and within the turnaround schedule
A leading petrochemical complex in the Kingdom of Saudi Arabia turned to Sulzer Chemtech for help and guidance when it wished to reduce the energy consumption in one of its large columns used in drying service. The existing column was already operating well in terms of product specifications.
According to Vinit Kale, Sales Manager Downstream, MEA region, Sulzer Chemtech: "The plant reached out to Sulzer Chemtech to suggest ways to reduce energy consumption without compromising on the column performance. There was also occasional vibration of trays in one section, and this was also requested to be solved."
After collecting required data and discussions to understand the full objective, Sulzer, performed a plant match simulation to develop the correct operating model.
Once the plant operating conditions and performance were confirmed by the simulation, Sulzer did further studies towards reduction of energy consumption by selecting proper internals and for ways to strengthen the trays causing suffering from vibration.
SELECTING THE RIGHT SOLUTION
![]() |
The company offered an end-to-end solution and employed its technology to enable the operator to save energy without compromising on performance and within the turnaround schedule |
Sulzer, with its decades of experience in revamping thousands of columns, proposed replacing trays in the top section with a combination of Sulzer’s AYPlusTM DC, one of the most advanced structured packing, and Sulzer’s well known MellapakPlusTM packing.
This hybrid solution offers the best solution for the drying application that the column operates for.
Kale says this combined bed of packing was proposed to replace 13 trays on the top section. "This, as per Sulzer’s study, would meet the requirement of reduction in steam consumption envisaged by the plant to a level of 31 per cent compared to the present operation."
In the bottom section, Sulzer studied the mechanical integrity of the existing trays and to alleviate the vibration problems.
The suggestion was to change the trays to Sulzer’s high performance trays, also mechanically designed to be more robust with advanced features.
Further, due to some other operational modifications in the plant, the temperature of the feed entering the column was expected to go up thus resulting in a possible two-phase feed as it enters the column. This necessitated the enlargement of the feed nozzle to a larger size to accommodate the two-phase flow.
END-TO-END SOLUTION
The plant operator was convinced about the feasibility of the solution to achieve the required energy savings.
However, it understood it could derive the full benefits only if such advanced internals are also installed correctly and if one organisation is undertaking the full responsibility.
This is where the Tower Field Services organisation of Sulzer, based locally in Saudi Arabia, stepped in.
Already well known for its support in providing local expertise for installation of advanced internals, Sulzer also presented to the plant operator its credentials for undertaking the nozzle enlargement job with its ASME certification for repairs on coded vessels.
After a detailed presentation and discussion, the plant operator was fully convinced that Sulzer is the most ideally suited partner to support it towards its goal.
Accordingly, it awarded Sulzer the full scope from design, fabrication and supply and installation of internals along with modifications in the column.
"Furthermore, Sulzer also presented a detailed work schedule to convince that the work could be completed during the ensuing turnaround of the plant," says Kale.
During the recently concluded shutdown, Sulzer mobilised its experts to complete the full scope to the satisfaction of the plant operator and within the turnaround schedule.
"The plant has been started up and the performance matches the prediction of the study thus helping the operator realise the ambitious goal of energy saving," concludes Kale.